How to manufacture PCB: 3 Tips of PCB Reflow Soldering Process
By:PCBBUY 10/19/2021 09:13
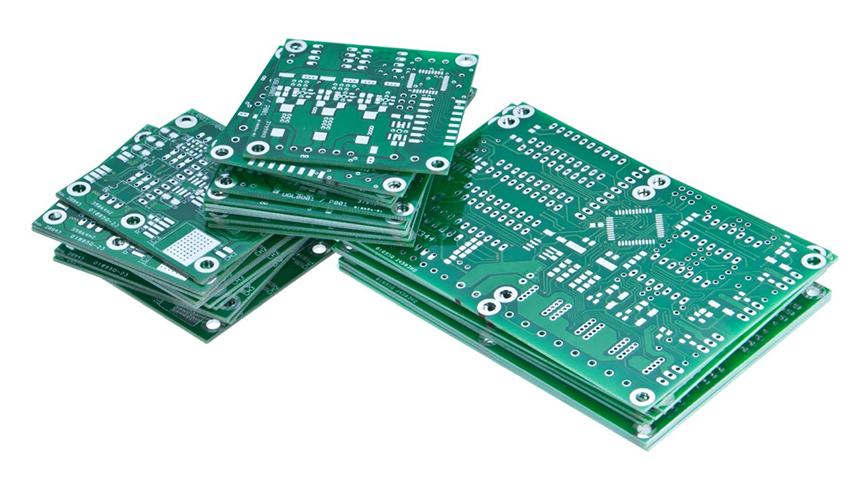
Reflow soldering is a process, which using the solder paste to connect one or thousands of tiny electrical components to their contact pads, and then it will control the whole assembly by heating. The solder paste reflows in a molten stage to create the permanent solder joints. What’s more, heating can be done by passing the assembly with the reflow oven as well as under an infrared lamp or by soldering individual joints with a desoldering hot air pencil.
Reflow soldering technology, making it possible to reliably solder surface mount components, especially the components with very fine pitch leads. And it’s the best for use with components used in mass produced electronics products. If you are looking for the information of PCB reflow soldering, please check and read the contents for more professional knowledge.
1. How to prepare for PCB reflow soldering?
The first stage in reflow soldering for PCB assembly is to apply solder paste and components to the board. These stages are covered in more detail in a separate page on this section of the website.
Solder paste
In essence solder paste is applied to the board. The paste is only applied to the areas that require soldering. While boards have solder resist layers added to them, it is necessary to only add solder paste to those areas where the solder is actually required. This is achieved by having a solder mask and solder paste "machine". This only allows the solder paste to be added to those areas of the board where it is needed. Once added the solder paste has been added to the board, it can move on to the next stage.
Pick and place
With the solder paste on the board the components can then be set in place. Normally an automatic pick and place machine is used because the numbers of components used these days and the accuracy required make manual placement non-viable.
The pick and place machine places the components onto the board, and they are held in place by the surface tension of the solder paste. This is quite sufficient for normal handling, although some care is obviously needed. It is possible for the components to be glued to the board, but this makes rework very difficult. Then with all the components in place they can be move to the reflow soldering machine.
2. What is the process of PCB reflow soldering?
The wave soldering process is composed of four steps: flux spraying, preheating, wave soldering, and cooling.
Flux Spraying
Cleanliness of metal surfaces is the basic element ensuring soldering performance, depending on functions of solder flux. Solder flux plays a crucial role in smooth implementation of soldering. Primary functions of solder flux include eliminating oxide from the metal surface of boards and component pins; protecting circuit boards from secondary oxidation during the thermal process; reducing surface tension of solder paste; and transmitting heat.
Pre-Heating
In a pallet along a chain similar to a conveyor belt, circuit boards travel through a heat tunnel to carry out preheating and activate flux.
Wave Soldering
As temperature constantly rises, solder paste becomes liquid with a wave formed from the edge boards that travel above. Components can be solidly bonded on boards.
Cooling
Wave soldering profile conforms to a temperature curve. As temperature reaches the peak in the wave soldering stage, it is reduced, which is called a cooling zone. After being cooled to room temperature, the board will be successfully assembled.
3. What are the advantages of PCB reflow soldering?
How do you know which type of soldering to use and when? It may depend on a variety of factors, such as pad shapes, the amount of time you have, component orientations, type of printed circuit board and more. In some ways, wave soldering is more complex. Issues like board temperature and time the board spends in the solder wave need careful monitoring. Failure to create the right wave soldering environment is much more likely to lead to board defects.
You don’t need to be nearly as concerned about controlling the environment when you’re utilizing reflow soldering to fabricate your printed circuit boards. However, even with that being the case, wave soldering tends to be faster and cheaper than reflow soldering. In more than a few cases, it’s the only practical way to solder a board. Reflow soldering is typically used in smaller-scale manufacturing products that don’t require a method amenable to fast, cheap mass production.
Keep in mind that you may be able to use both reflow soldering and wave soldering for certain situations. You might reflow solder parts on one side and then wave solder them on the other. Also, you can always manually solder or hand solder PCB components, but this will rarely be a good approach if you have access to one of the mechanical methods of soldering. Manual soldering would only be an alternative to reflow soldering, but reflow soldering is still far superior.
Industry Category