4 Essential Factors of Multilayer Metal Core PCB in PCB Layout
By:PCBBUY 11/11/2021 09:17
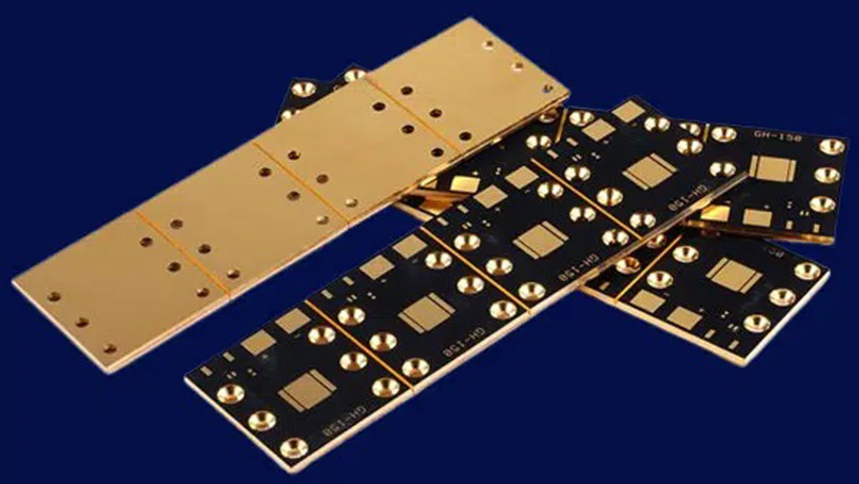
Accumulation of too much heat in printed circuit boards lead to malfunctions in the devices. Electronic devices that generate a considerable amount of heat cannot always be cooled using conventional fans. Conductive cooling through metal core boards is an ideal option. In conductive cooling, the heat is transferred from one hot part to a cooler part by direct contact. This works well since heat constantly seeks to move to any object or medium that is cooler.
Are you going to learn more about metal core PCB? Are you going to get into knowing the details about metal core PCB in PCB layout? Please check and read the content we prepare below.
1. What is the basic structure of metal core PCB?
In a multilayer MCPCB, the layers will be evenly distributed on each side of the metal core. For instance, in a 12-layer board, the metal core will be at the center with 6 layers on the top and 6 layers at the bottom.
The basic structure of MCPCB comprises of the following:
· Solder mask
· Circuit layer
· Copper layer – 1oz. to 6oz. (most commonly used 1oz. to 2oz.)
· Dielectric layer
· Metal core layer – heat sink or heat spreader
2. What are the main types of metal core PCB?
Aluminum substrate – The aluminum printed circuit boards offer good heat dissipation and heat transferring ability. Since they are light in weight, the aluminum core PCBs find their purpose in LED lighting, audio frequency apparatus, and communication electronic equipment.
Here, the thickness of the core ranges between 40 mils and 120 mils, with 40 mils and 60 mils being the most commonly used. Characteristics of the MCPCB with Aluminum substrate are as given below:
· Aluminum thickness: 2mm to 8mm
· Thermal conductivity: 5W/(mK) to 2.0W/(mK) (Watts per meter Kelvin)
· Peeling strength: >9lb/in
· Solder resistance: SF: 288℃, >180 sec.
· Breakdown voltage: >3000V
· Dielectric loss angle: 0.03
· Flammability: UL 94V-0
· Panel size: 18” x 24”
3. What are the applications of metal core PCB?
Metal core PCBs are quite useful in some specific applications, which usually generates a ton of heat in its process.
As we mentioned earlier, metal core PCBs are ideal for dissipating heat that builds up during operation. That’s why most manufacturers make use of it to maintain the solid performance of their devices. They also come in handy if you run a lot of long operational processes.
So, the major applications of the metal core PCBs are:
· Ideal for electronic communication equipment like electrical telegraphy, filter circuits, and frequency amplifiers.
· It’s a perfect fit for audio equipment like balanced amplifiers, input & output amplifiers, preamplifiers, power amplifiers, audio amplifiers, and many others.
· Power supply equipment like DC/AC converters, SW adjusters, switch regulators, and many others.
· Used for Computers and Computing components like CPU motherboards and power supply devices.
· Energy-saving lamps and lanterns, LED lamps.
· Power devices like converters, solid relays, bridges, rectifiers, and many more.
· Automation devices found in offices like motor drives.
4. What are the standards of metal core PCB?
Most PCBs used in consumer electronics, and even in more demanding applications like automotive and aerospace, use standard PCBs built entirely on glass-filled around epoxy resin laminates. Printed circuits on FR4 core materials are plated with copper foil on each side, and multilayer stackups are built by etching copper on each layer, followed by placing a low thermal conductivity resin layer as a prepreg between the next layer in the stack. This stack is then bonded using heat and pressure. After successive steps, you have a multilayer PCB.
These standard resins come with a narrow range of possible material properties that are determined by the resin content and type of resin impregnated in the PCB laminate. There are some drawbacks seen in standard FR4 laminates that are not ideal for certain applications:
· Low thermal conductivity compared to materials like copper or aluminum
· Losses in most FR4-grade laminates are too high for some RF applications
· These materials can have experience high expansion at high temperature
Industry Category