5 Challenges of Flexible PCB Manufacturing Process
By:PCBBUY 09/18/2021 09:49
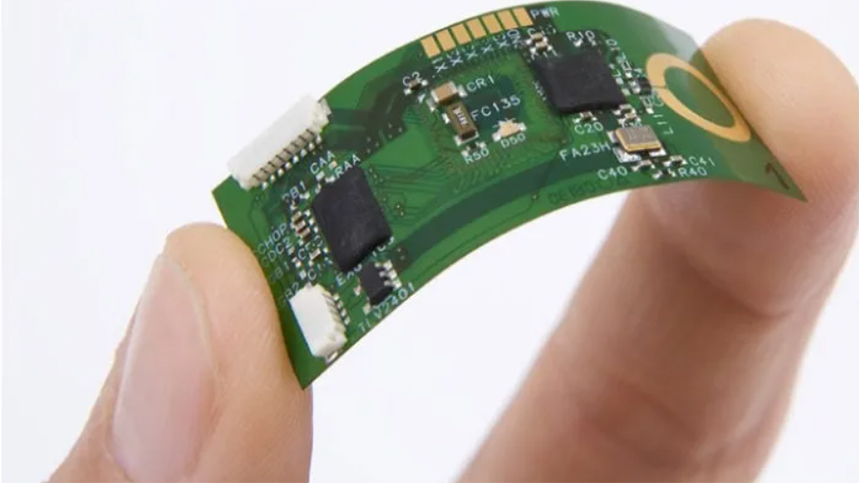
Flexible PCB, also known as flex circuit boards, flex PCBs, flex circuits, or flexible printed circuits, features a combination of several printed circuits as well as components that are positioned on a flexible substrate. The introduction of flexible PCBs has revolutionized the legacy electrical interconnection techniques, traditionally used to connect multiple parts of the same circuit or of multiple electronic devices.
In this passage, we will talk about the knowledge about the challenges during the flexible PCB manufacturing process, if you are interested in flexible PCB manufacturing, please check and read the content we provide below.
What are the 5 challenges during flexible PCB manufacturing process?
1. Knowing the structure of flexible PCB
As happens for rigid PCBs, FPCs can be divided into single layer, double layer or multi- layer circuits. The main elements of a single layer flexible printed circuit are the following:
· Dielectric substrate film: the base material of the PCB. The most commonly used material is polyimide (PI), characterized by high resistance to traction and temperature;
· Electrical conductors: made of copper, they represent the traces of the circuit; protective finish, made with cover lay or cover coat;
· Adhesive material (polyethylene or epoxy resin), used for joining the various parts of the circuit together.
2. Getting into the importance of flexible PCB
The statistics are clear, and they pinpoint that the production of flexible printed circuit boards increases every day. Intriguingly, they've become popular now, even though flexible circuits were first used in the 1950s. Have you ever thought about what the secret of their popularity is?
A large number of users considers them attractive for the following reasons:
• The ability to bend – the primary benefit is obvious, but it is also the most important.
• Improved reliability – the low number (or elimination) or connectors, solder joints, and other interface connections makes these boards more reliable.
• Thin and light – while ensuring flexibility, the manufacturers also found a way to reduce the size and weight of flexible PCBs. Thanks to that, it is easier to fit them in restricted spaces.
3. Disadvantages of flexible PCB
Although there are several and meaningful advantages, the FPC technology has also some drawbacks, or disadvantages. First of all, compared to traditional rigid PCBs, FPCs have a high one-time initial cost. Since flexible circuits are designed for very specific applications, the initial costs related to circuit and prototype design are higher than for rigid PCBs. Another disadvantage is the difficulty of repairing or modifying the multilayer PCB when it needs to be reworked. In this case, in fact, it is first necessary to remove the protective film that wraps the circuit, perform the intervention and then restore the protection.
4. Choose the proper material of flexible PCB
The performance of a printed circuit board always has a lot to do with the materials used when designing it. That is why identifying new and improving the existing materials is a way to enhance a flexible PCB.
The printed circuit board industry always works on implementing seemingly small innovations.
It is important to note that the manufacturers do not consider the same things when choosing materials for flexible and rigid printed circuit boards. When it comes to flex PCBs, thermal management becomes integral, as well as the capability of bending the material.
Apart from using improved materials, another way to enhance flexible boards is to come up with new technologies for the design and assembly process. The micro via technology is one of the latest major innovations in the industry.
5. How to control the size of flexible PCB?
The size of the microcircuit depends on the application but some of the key items that are important to many customers are:
· Keeping a very tight outline tolerance.
· Impedance values that can be held to +/-5% even in high volume applications.
· Gold plating for use in connector terminal applications.
· Using LPI solder mask on flexible substrate to keep solder mask damns intact.
· Adding small stiffeners to allow one end of the material to be rigid.
· Microcircuits require very fine line and spaces which requires specialized etching equipment.
· In-house punch press and tooling manufacturing capabilities improves our time to market.
Industry Category