5 Considerations of PCB CAF Failures for PCB Manufacturing Quality Control
By:PCBBUY 10/29/2021 09:29
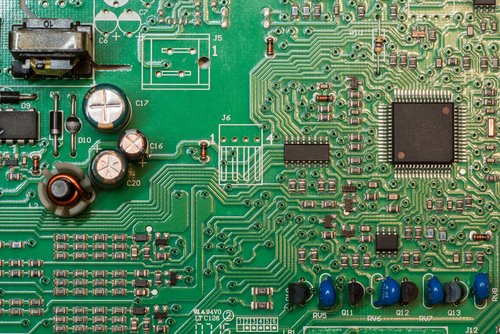
The concerns with board reliability and the possibility of conductive anodic growth in printed circuit board assemblies have increased in the last few years. Original equipment manufacturers have increased the design density, and are concerned with field failures due to conductive growth.
Do you know how to avoid PCB CAF failures? Are you going to learn more information of PCB CAF failures? In this passage, we are going to learn all the details of PCB CAF failures, if you are interested in it, please check and read the content for more.
If you want to order PCB product, please check and custom your order online.
1. What is the historical basic of PCB CAF?
CAF was first identified in 1976 by researchers at Bell Lab. The first studies involved tests of different coatings of UV-cured resins using FR-4 fine-line flexible printed circuits. Further failure-preventing variables were also studied, including the number of glass-reinforcement layers, cover coat and the thickness of the epoxy butter coat layer. Researchers found they could model time to failure on a log-normal plot and identified temperature, humidity and bias as factors that sped up the process. They also described four substrate-related failures.
In 1979, researchers first used the term CAF to refer to these failures. The paper that first used it focused on how materials and conductor orientation related to CAF formation. That same year also saw the introduction of the two-stage model. Investigations into CAF has continued to this day, with researchers testing how humidity, temperature, bias, materials, conductor orientation and other factors influence its formation.
Most of this research has focused on traditional laminates, such as FR-4, G-10, BT and MC-2. More recently, though, some have applied newer materials, namely CAF-resistant or halogen-free laminates, which typically have improved thermal properties.
2. How to identify PCB CAF?
Identifying CAF once it occurs is challenging, making it difficult to inspect and study. CAF often occurs in layers buried within PCBs. It also can appear alongside other contributing failure factors, making it hard to realize when CAF is a solely-responsible failure mode.
IPC Electrochemical Migration Testing:An IPC standard test to measure the resistance to the flow of current across the surface of a PCB substrate.
Temperature-Humidity-Bias (T-H-B) Testing: A SIR test that takes into account the processing temperature, relative and aging humidity and voltage bias.
You can also use various methods to image CAF formation on a PCB. These techniques include:
Scanning Electron Microscopy (SEM): This method involves the use of a primary electron beam gun that sends electrons toward the positively charged anode in a vacuum through electromagnetic lenses. You can operate this device in either secondary electron (SE) mode — which is ideal for surface-topography imaging — or backscattered electron (BSE) mode, which allows for atomic number contrast.
3. What are the factors of PCB CAF?
· Electrolyte – Water
· Voltage bias – Force that drives the reaction
· “Pathway” – A way for the ions to move from the anode to the cathode
· The following factors accelerate CAF formation
· Higher water content
· Higher Voltage levels
· Higher temperature (increases reaction rate of corrosion
4. What is CAF resistance in PCB?
Conductive Anodic Filament (CAF) has been increasingly concerns on printed circuit boards in the last few years. The major factors are current trend toward smaller size, lighter weights, thinner and higher performances that the density of PCB shall be designed with more closely spacing conductors, much smaller pitches and single-ply dielectrics such as mobile telephones, notebook computer and camcorder. In the other hand, some electrical applications must be exposed in extreme environment. For example, the safe necessity of automotive like engine control and brake control system. There cannot occur electrical shorts phenomenon, so the insulation resistance of material becomes very importance. These factors are pushing the demand for anti-CAF materials.
CAF is an electrochemical corrosion process that causes electrical shorts, when copper metal is dissolved at the anode and migrates to the cathode through the resin matrix/ glass fibers interface. CAF can occur between any two oppositely adjacent conductors when the conductors are in contact with the glass fibers. There are four ways that include hole-to-hole, line-to-line, hole-to-line and layer- to-layer. (See above diagram).
5. What is CAF formation?
·Electrical-charge carriers, which enable the formation of an electrochemical cell.
·Water, which occurs due to humidity and moisture build-up and dissolves the ionic material, sustaining them in their mobile ionic state.
·An acid environment near conductors to enable corrosion at the anode.
·A voltage bias, which is the force that drives the reaction.
·A pathway for the ions to take as they move from the anode to the cathode.
Many other factors are believed to accelerate the formation process including high temperatures, high humidity, repeated thermal cycles, high voltage gradient between anode and cathode, some soldering flux ingredients and more. Other problems, such as component failures and exceeding maximum operating temperatures might also contribute to a CAF-related failure.
Industry Category