5 Effective Tips for Signal Integrity PCB Layout Considerations
By:PCBBUY 10/16/2021 09:47
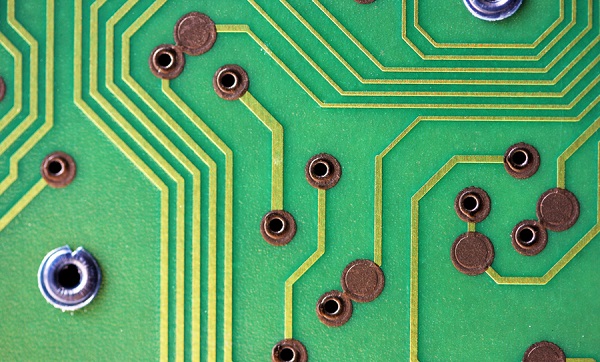
The faster signal speeds get in electronics, the more they are affected by crosstalk, impedance miss-matches, ringing, and ground bounce. Eventually, these effects will degrade the fidelity of the signals, or the signal integrity, to the point where transmission errors occur, causing failures in how the system operates. These failures may manifest themselves as intermittent problems, or they may completely shut down the system.
In this passage, we will provide you all the details about the tips of signal integrity in PCB layout. If you are interested in the PCB signal integrity, please check and read the content below more professional knowledge.
If you want to order PCB product, please check and custom your order online.
1. What are the common issues of signal integrity in PCB layout?
There are four main areas of circuit design and layout that must be taken into consideration to ensure that the signal integrity of a board or circuit design are maintained:
· Transmission line effects
· Impedance matching
· Simultaneous switching effects
· Crosstalk
To ensure that signal integrity is maintained, all the issues must be addressed to ensure that the signal is not distorted in any way and the data is corrupted. In this way the system is able to operate satisfactorily without errors and at the required speed.
2. What are the fundamentals of signal integrity in PCB?
A signal on a circuit board can have its quality degraded due to a number of different effects, and these can be categorized into different groups. Here are four main areas of poor signal integrity that you should be aware of.
Electromagnetic Interference (EMI)
High-frequency signals can radiate EMI if care isn’t taken with how they are routed on the circuit board. Not only can the length and configuration of the traces be a problem, but trace and via stubs can act as an antenna as well.
Unintentional Electromagnetic Coupling (Crosstalk)
High-speed traces that are too close together may inadvertently couple with one signal overpowering the other. This crosstalk can result in the victim signal mimicking the characteristics of the aggressor signal and not performing the task it was intended to do.
Simultaneous Switching Noise (Ground Bounce)
With the number of components switching between high and low states on a circuit board, the voltage level may not return all the way to the ground potential as it should when it switches low.
3. How to analyze signal integrity in PCB layout?
This portion is really about circuit design and component selection. There are three important analyses that tell you a significant amount of information about your board’s behavior.
Transient behavior
Transient responses can also be modeled in the time domain using transient analysis, or you can determine the behavior of transients from pole-zero analysis.
S-parameters and transfer function
Certain functional blocks in your board can be modeled as multiport networks, meaning their linear behavior can be described in terms of S-parameters at a particular frequency. You can determine the S-parameters from a reflection coefficient in the time domain.
Noise analysis
Components that exhibit rectification and saturation will respond differently to noise than they will to an intended signal. This aids filter and amplifier design in the presence of noise as low level noise may experience more or less transimpedance than your desired signal.
4. What are the applications of signal integrity in PCB layout?
In the process of PCB design, a lot of design rules have been summarized based on signal integrity theory. With reference of these PCB design rules, signal integrity can be obtained better. In the process of PCB design, design information has to be known in detail, including:
· Component layout position, whether there are special requirements on components with large power and heat dissipation on chip components.
· Classification of signals, speed rate and transmission direction and impedance matching requirement.
· Signal driving capacity, key signal and protection measures.
· Types of power, ground, noise limit requirement of power and ground, setting of power plane and ground plane and division.
· Type and speed rate of clock lines, source of clock lines, direction, delay requirement of clock and maximum routing requirement.
5. How does material affect signal integrity in PCB?
Choice of PCB materials affects the signal transmission. Signal losses occur due to attenuation. Dielectric material is an indispensable material in PCB. At high frequencies the molecules of the dielectric medium are excited. Excited molecules absorb some of the signal energy, leading to signal loss. This is termed as dielectric absorption. This can be reduced by careful selection of the dielectric material of the PCB.
Another issue in transmitting signals via conducting wires is the skin effect. At very high frequencies the signal power tends to travel on the surface of the conductor alone. This is Skin effect. Due to this the effective conductive area is reduced. Any discontinuities on the surface of the conductor will lead to signal attenuation. Signals traveling on the surface of the conductor results in self-inductance which results in increased inductive reactance. Skin effect can be minimized by increasing the width of the conducting surface.
Pre-Emphasis and receiver equalization techniques can also be used to reverse attenuation loss. In pre-emphasis, the high-frequency signal components are amplified and transmitted to withstand the signal attenuation and in receiver equalization, low frequency signals are specifically attenuated at the receiver end using dedicated circuit to compensate for the line losses.
Industry Category