5 Effective Tips to Learn PCB Functional Testing Methods
By:PCBBUY 06/22/2022 10:43
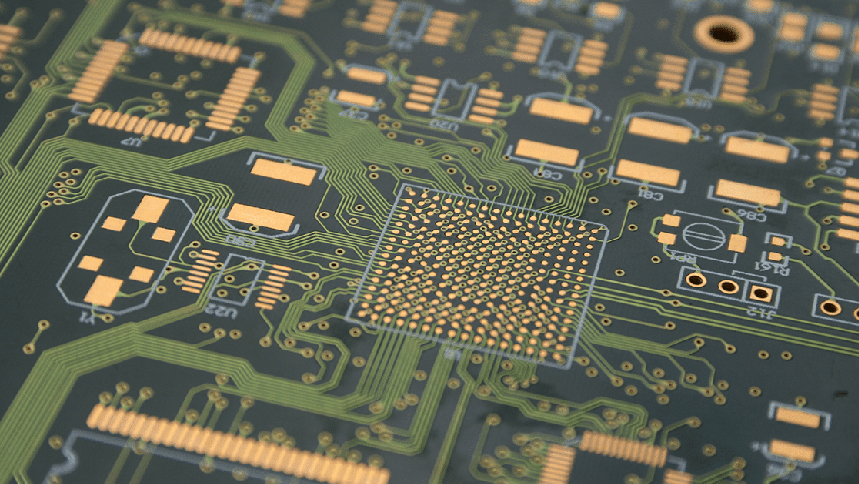
Testing can help identify critical errors early on, increase yield and reduce costs, and improve overall quality and safety. PCB functional testing is one of the best and most versatile tools for verifying a board for usage in the real world, but it is just one of many testing methods in a manufacturer’s arsenal. With each testing method having its advantages and disadvantages, it can be difficult to determine the best test method for your situation and budget. In this article, we will review 5 of the most common PCBA testing methods.
So it's necessary to carefully check and confirm the final design drawing provided by manufacturer prior to practical manufacturing so that manufactured PCBs conform to requirement of the last version. If you are looking for more about PCB functional testing, please check and read the content below.
What are the main types and advantages of PCB functional testing?
Before a circuit board gets to the functional testing stage of its manufacturing, there are many other tests and inspections that it will go. These include:
Manual inspections: Inspections are used to verify different aspects of the circuit board manufacturing processes. Some of these inspections use microscopes or close-up videos for detailed examinations.
Automated Optical Inspection (AOI): These inspection systems use different video capabilities to compare images of the board to known “golden” images. They are used to check for shorts between metal, spacing violations, drilled hole breakout, solder paste application, finished solder connections, and the location and orientation of components on the board.
X-ray: For circuit boards with complex and dense component placement, X-ray inspection systems are used to examine components such as BGA’s for solder defects.
Here are some of the systems that can do some or all of the functional testing of a circuit board:
Flying Probe: This system maneuvers between two and six probes around the board to contact tiny metal pads called test points built into the design. Primarily this machine is used to detect improper solder connections, but it can include some limited functional testing. However, with only six probes available at any one time, the range of testing is severely restricted.
In-Circuit Test (ICT): The ICT system accesses the same onboard test points as the flying probe test. The difference is that the ICT system uses a test fixture with probes arranged to contact each test point simultaneously. The resulting coverage of test points not only allows the ICT system to work very fast, but it can also run sophisticated functional tests making it ideal for production builds of circuit boards. On the other hand, the ICT fixture is time-consuming and expensive to develop or modify, and therefore is generally not used for prototypes or low-volume production.
CableScan: This testing system relies on connectors instead of test points to connect to the board and is a good fit for backplanes or other interface boards. CableScan will check every pin to each other through its connections, searching for assembly problems such as improper solder connections. Simultaneously, it will run functional test signals through the same connections.
Functional testing is an integral part of producing high-quality circuit boards by verifying the PCB as operational before it is shipped to the customer. Here is where the abilities of your local PCB contract manufacturer are essential to the success of your circuit board build.
What is the future of PCB functional testing?
Industry insiders believe future functional test platforms will need many of the features found in today’s in-circuit test systems. For example, modularity is increasingly important to functional testing. Manufacturers are moving from proprietary functional testers to modular test systems that can be reconfigured. This makes more economic sense for electronics manufacturers who built custom systems for each individual application.
Nolte predicts that functional testing will continue to move from hardware toward software. Today’s engineers "can make virtual test systems. Designers can pretty much grab what they need and convert these test systems from doing one job to doing another without having to replace hardware components," says Nolte.
Another in-circuit testing trend that promises to expand into functional testing is the availability of public "libraries" of different test routines. Component manufacturers, for example, will begin providing functional test parameters of their components. "Someone’s going to make an operating system where you can just plug in these components and create a library of different things. So the next time that you come out with a product, you won’t have to start from scratch," says Lowenstein.
Industry Category