7 Common PCB Design Mistakes in PCB Design Process
By:PCBBUY 09/15/2021 09:26
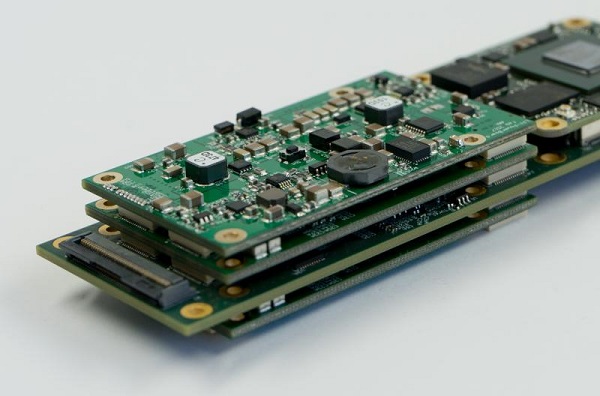
As an important process of the whole PCB manufacturing process, PCB design plays a pretty essential role to guarantee the quality and performance of the finished boards. Nut there are still lots of challenges during the PCB design process. Independent design reviews are one of the best ways to prevent costly errors such as the ones listed below.
In this passage we will provide you everything about common PCB design mistakes, and if you are curious about the topic, please check the content below to learn more information.
What are the 7 common PCB design mistakes?
1. Errors in landing patterns
PCB design software packages provide libraries of electronic components. These libraries include the schematic symbol and PCB landing pattern for each component. You won’t usually have problems if you stick to these components in your design.
However, if you use components outside of these libraries then you must manually draw the schematic symbol and the PCB landing pattern. It’s easy to make mistakes especially on the landing pattern. For instance, if the pad to pad spacing is off by as little as a fraction of a millimeter, the pins won’t align properly making soldering difficult or impossible.
2. Flexible circuit conductors arrangement
Conductors' arrangements are crucial distinguishing factors that differentiate the design process involved with a rigid and flexible course. Unlike wooden boards, flexible circuits can twist, turn, and bend. If the conductor arrangement is incorrect, it can lead to hazardous consequences, especially during board flexing.
Be cautious when you design the conductors' arrangement. One way to minimize the conductors' stress during flexing is to make sure they pass through curved areas.
3. Blind/buried vias used or non-manufacturable
Even if you only want to connect a trace from layer one to layer two, all other layers have the via too. The problem with this is it can increase the size of the PCB, because the via reduces routing space on every layer.
A blind via connects an external layer to an internal layer and a buried via connects two internal layers. However, it’s not that simple. Blind and buried vias have severe limitations based on how the layers stack up on the board. They also drastically increase prototyping costs so I don’t recommend them for most applications.
4. Sub-optimal wireless antenna layout
Layout of an antenna for wireless functionality is critical. For maximum power transfer between transceiver and antenna, must have matched impedance. Consequently,
There is proper micro-strip connecting the antenna and the transceiver. A microstrip is a type of transmission line fabricated on a PCB for carrying microwaves (high frequency radio waves). This is a conducting strip separated from a ground plane by a dielectric layer. Generally, the microstrip needs to be designed with a 50 ohm impedance for maximum power transfer with the antenna.
5. Insufficient power trace width
If a PCB trace will have more than roughly about 500mA flowing through it then the minimum width allowed for a trace probably won’t be enough. The required width of a trace depends on
· Internal or external layer
· Thickness or weight of the copper foil
For the same thickness, an external layer can carry more current for the same width than an internal trace (external traces have more air flow enabling better heat dissipation).
Then when calculating the current carrying capability of a PCB trace you must also specify the permissible temperature rise for that trace. Generally a 10C rise is a safe choice, but if you need to squeeze down the trace width more you can use a 20C or higher allowed temperature rise.
6. Wrong position of the decoupling capacitors
Decoupling capacitors are required on the PCB power supply lines to ensure a stable power supply free from transients or oscillations to all board components. It is absolutely necessary that these capacitors are always connected in parallel with the power supply and placed as close as possible to the pins of the components that require power.
The power line coming from the power source must be properly routed on the PCB quote, in order to get to the decoupling capacitor before going to the pin that needs a stable voltage. Note that, otherwise, the decoupling function cannot work properly; in fact, all voltage regulators use a feedback circuit which can oscillate if not adequately stabilized.
7. Minimizing Slithers
Slithers are undissolved copper chunks that may stick to the circuit board during the chemical etching process. These slither may cause short circuits and several other manufacturing failures. A PCB designer should always ensure that the minimum copper width is above the manufacturer’s requirement. This helps to minimize slithers, and produce properly working for circuit boards.
Industry Category