7 PCB Manufacturing Defects & How to Solve PCB Problem?
By:PCBBUY 09/16/2021 09:32
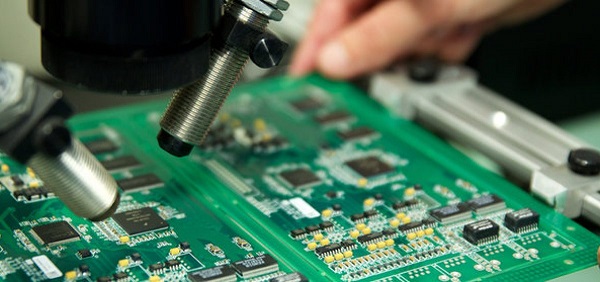
There are many challenges and defects during the whole PCB manufacturing process. PCB manufacturing defects and solutions being at the receiving end of a PCB failure can be annoying and dissatisfying. Understanding some of the common defects can help you perform some analysis and proffer solutions to ensure the quality and sustainability of cheap PCB.
In this passage we will lead you to learn the PCB manufacturing defects and how to solve them. If you are going to get into the topic, please check and read the content below for more information.
What are the main 7 PCB manufacturing defects and the solutions?
1. Temperature & Moisture
PCBs are affected by temperature, both in storage, and when they are installed in components. Extreme temperatures or large temperature fluctuations may cause components or joints to break or fail. Many people take the maximum or minimum safe temperature into consideration, without thinking about the fluctuations in temperature that may occur either during operation or in storage. Exposure to moisture, both during the manufacturing process and in storage, can cause shorts to occur and may lead to defects in components. Humidity in the air, as well as the moisture content in the solder can wreak havoc on printed circuit boards, causing corrosion.
2. Plating Hole Defects
Holes carry electricity from one side of the board to the other. Plating of the hole wall during manufacture. During this, If the copper deposition is incorrect, it will create plating voids, leaving gaps in the wall with no copper coating. It could happen due to air bubbles, contamination in the holes, contaminated materials, and other similar reasons. You can prevent this from happening by following the manufacturer’s direction and cleaning the equipment as instructed.
3. Soldering Defects
The bulk of printed circuit board defects can be traced back to a soldering issue. Soldering is a technical skill that becomes even more difficult when dealing with the extremely small components on a printed circuit board. Some of the most common soldering defects include:
Open joints, sometimes called “dry joints,” occur when the solder doesn’t bond correctly with the point of contact, typically the pad. Occasionally, open joints are caused by using too much solder, which causes the component to lift.
Shifts occur when the printed circuit board or component is not aligned correctly during the soldering process. Shifts can result in open joints, shorts, and crossed signal lines. Short circuits, often referred to simply as “shorts,” most often occur due to a soldering error called solder bridging.
4. Lack of Solder Mask
It is a common problem that accompanies PCB manufacturing at home or production PCB manufacturing. The error is small, therefore challenging to identify. If these shorts go undetected, they can damage the complete assembly by burning up the components. One standard solution is adding a solder mask between pads, so there is no gap between the stencil and PCB.
5. Electrostatic Discharge Defects
Defects caused by electrostatic discharge can be extremely frustrating, since they are not always easy to detect. Latent failures caused by electrostatic discharge, or ESD, can cause significant cost increases due to the return or repair of the damaged unit. Electrostatic discharge can even cause shorts to occur by creating enough heat to soften solder. Electrostatic discharge is caused by both human and machines, and can happen during nearly every point in the manufacturing and assembly processes.
6. Substrate Size Defects
The change in size of substrate weft/warp is difference in direction. This occurs because of not paying any attention to the direction of fiber which is resulting in residual stress inside the board’s base, when released its direct impact is on the shrinkage of size of substrate.
The best possible solution to this problem is determining the change rule of direction of weft/warp as per the compensation of shrinkage of the film. Trim it at same time as per the direction of processing of fiber.
7. Copper Foil Etching Defects
Sometimes a part of the substrate’ copper foil is etched away due to the restrictions because of changing the substrate for producing dimensional changes when stress is relieved.The best solution for the problem is during the process of designing the circuit board, it must be tried to make the board in even distribution. If this is not possible, then some space for transition must be left which would not affect the circuit. This is due to the reason that plank structure of the cloth of glass and density difference of weft is leading to the differences in intensity of longitude to latitude of plank.
Industry Category