Applications and Considerations of Large Area Copper Plating and Grid Copper Plating
By:PCBBUY 03/02/2024 10:51
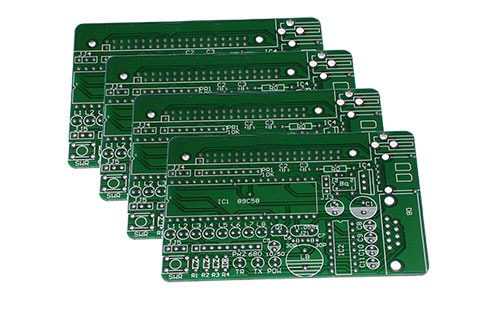
In the field of electronics manufacturing, PCB (Printed Circuit Board), as the cornerstone of connecting and supporting electronic components, its design and fabrication techniques directly affect the performance and quality of electronic products. Among them, copper plating, as a key technology in PCB fabrication, plays an important role in the conductivity, heat dissipation, electromagnetic shielding, and other aspects of the circuit board. This article will delve into the two basic methods of PCB copper plating—large area copper plating and grid copper plating—and analyze their advantages and disadvantages in different application scenarios.
Characteristics and Applications of Large Area Copper Plating
Enhancing Current Capacity and Shielding
Large area copper plating, with its excellent conductivity, is often used in applications requiring high current, such as power supply sections or power amplifiers. Additionally, large area copper layers can provide certain electromagnetic shielding, reducing the impact of external interference on the circuit.
Potential Issues with Wave Soldering
However, when PCBs with large area copper plating undergo wave soldering, issues such as board warping or bubbling may occur due to the differential thermal expansion coefficients between copper and the substrate. This not only affects the flatness of the circuit board but may also lead to poor soldering or component detachment.
Solution: Slotting to Alleviate Copper Foil Bubbling
To address this issue, engineers often create several slots on large area copper plating to alleviate the thermal stress during soldering. This approach maintains the conductivity and shielding properties of the copper foil while reducing the risk of warping and bubbling.
Characteristics and Applications of Grid Copper Plating
Primarily for Shielding
Unlike large area copper plating, grid copper plating is mainly used for electromagnetic shielding rather than conducting high current. Although its conductivity may not be as good as large area copper plating, it performs excellently in shielding electromagnetic interference.
Superior Heat Dissipation Performance
From a heat dissipation perspective, the design of grid copper can reduce the heated surface area of copper, thereby improving heat dissipation efficiency. This is particularly important for circuits requiring good heat dissipation, such as high-frequency circuits or high-power circuits.
Considerations for Operating Frequency and Electromagnetic Interference
It should be noted that grid copper consists of interlaced traces that generate certain inductance during operation. When the operating frequency is high or the effect of grid lines is significant, it may cause circuit interference, affecting the normal operation of the system. Therefore, when using grid copper, engineers need to select and optimize according to the actual situation of the circuit board to ensure stable operation even in high-frequency environments.
Selection for High-Frequency and Low-Frequency Circuits
Grid Copper Plating for High-Frequency Circuits
For high-frequency circuits, due to their high operating frequency and fast signal transmission speed, the requirements for electromagnetic shielding are correspondingly higher. Therefore, in these cases, grid copper plating is favored for its excellent shielding and heat dissipation performance. Additionally, engineers need to adjust the width and spacing of the grid lines to reduce the impact of inductance on circuit performance.
Large Area Copper Plating for Low-Frequency Circuits
Comparatively, low-frequency circuits have lower requirements for electromagnetic shielding but emphasize current conduction and heat dissipation performance. Therefore, in these scenarios, large area copper plating is more suitable. It can withstand large current loads and mitigate risks of warping and bubbling by implementing measures such as slotting.
Conclusion
In summary, the PCB copper plating techniques of large area copper plating and grid copper plating each have their advantages, disadvantages, and applicable scenarios. When designing circuit boards, engineers should choose and optimize them based on actual needs and circuit characteristics to ensure stable performance and reliability. Meanwhile, with the continuous development and innovation of electronic technology, we look forward to further enhancements and optimizations in copper plating technology, bringing more possibilities and development space to the field of electronics manufacturing.
Industry Category