Difference between SMT and through-hole technology
By:PCBBUY 07/13/2021 17:48
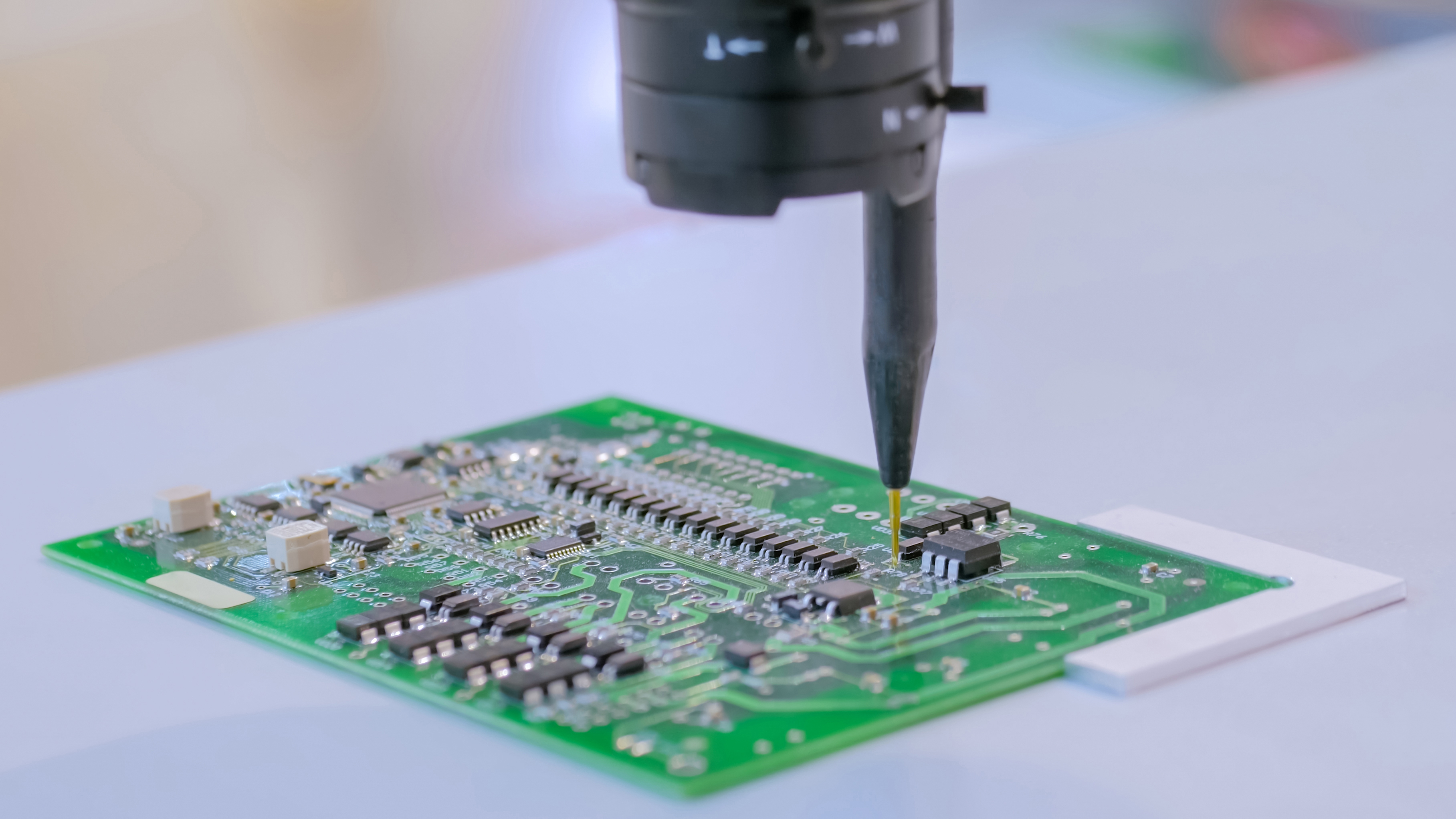
During the whole PCB manufacturing process, SMT and through-hole technology are very important steps. But what are the differences between SMT and through-hole technology? In this passage, we are focus on the topic and please follow us to check the content below.
What is through-hole technology?
Through holes are considered to be one of the older designs by many, whereas surface mount is pretty new. And to some extent, it is undeniably true, but if we think about practical applications, the through-hole technology is still significantly better in specific scenarios. In the 1950s, printed circuit boards came with tracks written on only one side.
When you insert the leads of a component into the board, you increase the drilled holes. Therefore, the negative electrode side has an element soldered to the copper on the board. The later stages saw the introduction of tracks on both sides of the boards and inner layer tracks of the printed circuit board. It gave way to plated through-hole technology, making it possible to attach components to the inner layer of the circuit board, improving the concept of through-hole PCBA assembly.
What is SMT?
Surface mount technology became known in the 1960s, and the applicability slowly rose in the 1980s. This technology was known as planar mounting in the beginning. The technique of surface mounting involved SMDs or surface mound packages. Components in this board have lead surrounding or underneath.
What separates surface mount from through-hole technology is that there is no need to drill holes in the circuit board to connect the tracks and the components. Establishing relationships through leads. The ingredients are in direct touch with the PADs of the circuit board And add solder paste to PAD with the help of stencil solder. There is also a pick and place machine responsible for placing the components on the solder paste set initially above the PAD. After setting these components, they have to be placed in a reflow oven or introduced in a vapor phase to be soldered permanently in the surface mount PCB assembly.
What are the differences between them?
In the case of surface-mounted technology, the PCB can mount more components due to two factors. First, the elements of the SMT are smaller themselves, and then they can also be placed on either side of the board. The space problem prominent in the through-hole is overcome in the surface mount technology so space can get smaller, lighter, faster, and more powerful.
Higher pin count In SMT sssembly than through-hole technology
SMT beats THM in this regard because they can hold much higher pin count. Pin count on a component board is simply the lead count of the component, which is the total number of the part leads that a printed circuit board can fit.
The leads of through-hole components have become replaceable with the invention of smaller parts called vias. They allow conduction between the various levels of the PCB, and by doing so, eliminate the need for through-hole leads. On the other hand, surface mount components are much higher in performance, have shorter points, and the pins are much more interconnected, which leads to better speed.
SMT Assembly Components Are Usually Cheaper Than Through-Hole Components
The through-hole method requires drilling holes in the empty side of the board. It is a task that takes a lot of time and costs a hefty amount. THM also makes the routing area limited in any board that has multiple layers. It is only because the holes should pass through all these layers. When we look at the through-hole PCBA, the assembly side comes at a fraction of a cost for placing components than a surface mount.
On the other hand, the surface mount assembly has a plurality of terminals soldered to the tubular body. Compared with flat chip vias used, the cost of these components is much cheaper.
Surface Mount Technology Is More Helpful For Assembly Automation
SMT can be produced in high volume at much lower costs because the SMT has the possibility of assembly automation. It also results in lower costs during production.
Automated assembly can save PCB assembly time even more. Many PCB suppliers currently have production machines with surface mount technology. It can be assembled accurately and quickly.
From this point of view, it is faster and more advanced than through-hole technology. If you are looking for assembly speed and need to produce PCBs in large quantities, you can choose surface mount technology. Ask your PCB supplier if they can provide it.
Through-Hole Technology Pays More Attention To Performance
The way through-hole components are soldered makes it durable in high heat and shock scenarios. The through-hole elements have long led, and these can be inserted through the drill holes, ultimately being fastened to the copper pads underneath. It is a secure process that is much more reliable than the mounting style in SMT. It also makes it possible for through holes to endure higher stress conditions.
The through-hole components are also more significant, and while that makes space an issue, it helps with high power applications. Parts can also be easily removed and replaced in urgent situations, which is not right in SMT PCBA. So, performance-wise THM has a lot of advantages over SMT.
The Technical Cost Difference Between Through Hole and Surface Mount
Undeniably, the THM issue is the drilling cost, which makes it more expensive and time-consuming than the SMT. The components also have to be hand soldered on the board. Since the SMT PCBA offers much higher volume and soldering can be automated, they are cheaper.
Industry Category