Etching Pcb Process
By: 03/26/2024 13:44
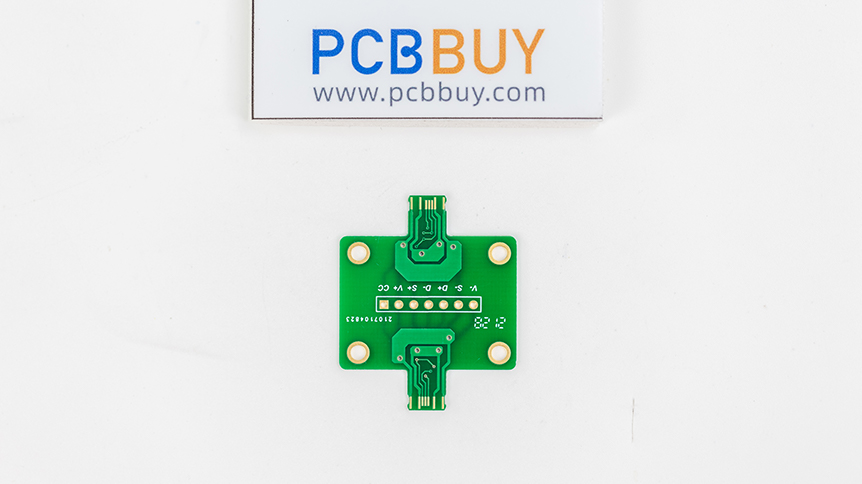
Circuit boards, as indispensable core components of modern electronic devices, each step in their manufacturing process appears crucial. Among them, the circuit board copper etching process stands out as a key juncture to ensure the performance and quality of circuit boards. This article will delve into the process of circuit board copper etching, potential issues that may arise, their solutions, and elucidate their impact on the overall performance of circuit boards.
The circuit board copper etching process is a critical step in ensuring the performance and quality of modern electronic devices, as every step in its manufacturing process is crucial. This process involves chemically or physically treating copper layers to remove excess copper and form the required circuit patterns. It plays a pivotal role in circuit board manufacturing as it directly affects conductivity, line accuracy, and overall reliability.
Typically, the circuit board copper etching process employs chemical etching methods. Initially, a corrosion-resistant layer, usually photoresist, is applied to the surface of the copper layer on the circuit board. This corrosion-resistant layer has excellent resistance to chemical corrosion, protecting the copper layer from etchant solution erosion. Next, the desired circuit pattern is transferred to the corrosion-resistant layer through photolithography techniques. In this step, specific light sources and masks are used to accurately project the circuit pattern onto the corrosion-resistant layer, forming a patterned resist layer. Subsequently, the circuit board is immersed in etchant solution, and the unprotected copper layer is dissolved by the etchant solution, exposing the desired circuit pattern.
Common Issues in Circuit Board Copper Etching Process
Despite the relatively simple theoretical concept of the circuit board copper etching process, various issues may arise during practical operation. Among them, over-etching and under-etching are the most common problems.
Over-etching refers to excessive removal of the copper layer, leading to deviations from the designed specifications such as line width and spacing on the circuit board. This problem may be caused by factors such as high concentration of chemicals in the etchant solution, prolonged etching time, or elevated temperature. Over-etching not only affects the conductivity of the circuit board but may also result in severe issues such as short circuits or open circuits.
In contrast, under-etching refers to incomplete removal of the copper layer, leaving behind residual copper layers. This may occur due to factors such as low concentration of chemicals in the etchant solution, insufficient etching time, or low temperature. Under-etching similarly impacts the performance of the circuit board, such as increasing resistance or reducing signal transmission efficiency. Moreover, under-etching may lead to reliability issues during subsequent use of the circuit board.
Addressing Issues in the Circuit Board Copper Etching Process
To avoid issues like over-etching and under-etching, strict control of various parameters during the etching process is necessary. Firstly, it is essential to ensure the etchant solution has an appropriate chemical concentration, neither too high nor too low. Secondly, precise control of etching time and temperature is necessary to ensure uniform and adequate etching of the copper layer. Additionally, proper selection and treatment of circuit board materials are required to ensure factors such as surface flatness, texture direction, and thickness meet requirements.
In addition to strict parameter control, advanced technological means can be employed to enhance the precision and reliability of the circuit board copper etching process. For example, computer-aided design software can be used to precisely design circuit patterns, high-precision lithography machines and masks can ensure accurate pattern transfer, and advanced etching equipment and processes can control uniformity and stability during etching.
Impact of Circuit Board Copper Etching Process on Performance
The impact of the circuit board copper etching process on the performance of the circuit board is evident. Firstly, by precisely controlling the etching degree and shape of the copper layer, high-precision layout of circuit board lines and excellent conductivity can be achieved. Secondly, the copper etching process also affects performance indicators such as thermal stability and mechanical strength of the circuit board. For example, in high-frequency high-speed circuits, minor changes in line width and spacing may significantly reduce signal transmission efficiency; whereas in high-power applications, good heat dissipation performance relies on precise layout and thickness control of the copper layer.
Furthermore, the circuit board copper etching process also has a significant impact on the reliability and durability of the circuit board. If the copper layer is not completely etched or over-etched, it may cause issues such as short circuits, open circuits, or performance degradation during the use of the circuit board. Therefore, strict quality control and technological innovation in the copper etching process are essential in the manufacturing of circuit boards.
Conclusion and Outlook
As a critical step in circuit board manufacturing, the circuit board copper etching process plays a decisive role in the performance and quality of circuit boards. By delving into the process, potential challenges, and solutions, we can better understand the importance and complexity of this process. With the continuous advancement of technology and the application of new materials, we have reason to believe that the circuit board copper etching process will become more precise, efficient, and reliable in the future. This will provide strong support for improving the performance and expanding the functionality of electronic devices, thereby driving continuous innovation and development in the entire electronics industry.
Industry Category