How Many PCB Manufacturing Defects Relate to Materials and Components?
By:PCBBUY 08/31/2023 16:58
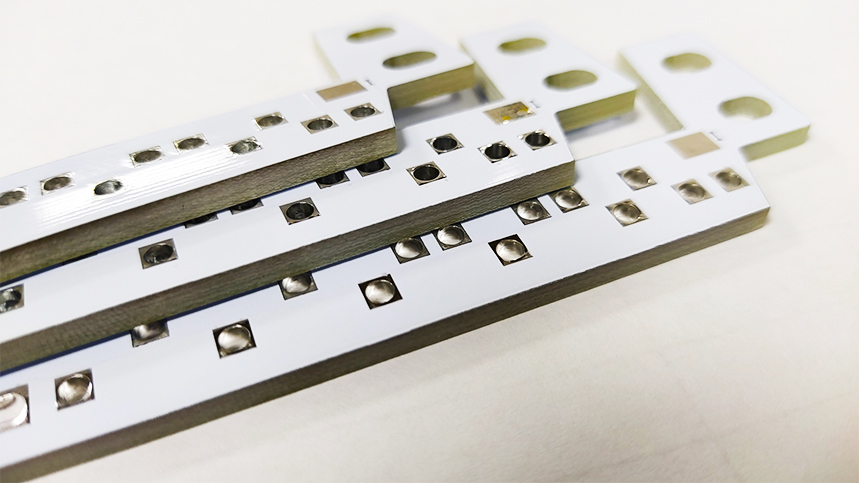
Anyone who’s ever constructed or built a prototype on a breadboard knows how easy it is to make mistakes placing package legs that can take hours to troubleshoot later. One might think the easy part would simply be “combining the pieces as instructed,” while this is certainly more straightforward than circuit design, it is also fraught with difficulties. The need for considerable and pervasive attention to detail is critical for circuits, and this extends to the PCB itself for the best manufacturing outcomes.
No matter how much a product has observed its design intent, it’s still necessary to closely monitor design details that could harm production. PCB manufacturing defects typically arise due to a failure to incorporate best practices or follow DFM best practices. However, an experienced engineering team can pore over a design to optimize areas needing refinement.
Many PCB Manufacturing Defects Relate to Materials and Components
All designs are not inherently DFM. While general design best practices and DFM overlap heavily due to industry standards focusing on production, many boards are built to assuage the validity of testing, assembly, or other manufacturing sub-processes. For PCB designers that don’t have as deep manufacturing expertise as they do design, the issues discovered in manufacturing may seem entirely divorced from design best practices. Through no fault of their own, they may miss design and component issues that will cause manufacturing problems. Quality CMs, on the other hand, have years and years of experience working on PCBs from various industries and can partner with you to help mitigate these issues.
Regarding PCB production, there are two key areas where manufacturing problems can arise:
Materials: Certain materials that are optimal for specific circuits. If materials specified in the board layer stackups are ill-suited for a particular function – say high-speed design – the result will be suboptimal performance. There are also cases in which the materials requested for the design aren’t suitable for the operating environments of the board or cost-effective in its manufacturing.
Components: Some components that designers choose for their designs may be legacy components enshrined in their libraries years ago, and they may not realize that the status of those components has changed over time. They may have longer lead times, or their end-of-life (EOL) status may render them unavailable. The CM will be able to verify the status of the components in the design and make recommendations on replacements, if necessary.
Specific Design Defects That Impact Manufacturing
Layer stackups and component issues are major design foci, but there are more subtle manufacturing defects that can be easy to overlook:
Fiducials: These markers serve as targets for computer vision systems to align fine pitch parts, such as QFPs or BGAs. Fiducials need to be placed in any three corners of an assembly side of the board to enable targeting in the x- and y-axes.
Proper clearance: For automated assembly and test equipment, components need enough clearance to features and board edges to prevent shorts, poor solderability, degraded signal integrity, and obstructions.
Component-to-component placement: Components that are too close to each other or rotated incorrectly can cause problems during wave soldering: taller components preceding shorter components result in a shadowing effect that reduces the strength of their solder joints. Chip components rotated perpendicular to each other can result in the same issue.
Tombstoning: This effect can happen when unequal heating is applied to a chip component during solder reflow, causing it to stand up on one end instead of both ends soldering down as expected. The unequal heating can be due to incorrect SMT land pattern sizes used for the part or different trace widths intersecting the pads.
All of these issues can potentially cause problems for a PCB during manufacturing. The key is to use good design for manufacturability (DFM) practices during the PCB layout to avoid these common pitfalls. Here is where an experienced CM shines: helping designers understand DFM practices that apply to the particular needs of their design.
Industry Category