How silk screen printing works?
By:PCBBUY 07/24/2021 17:40
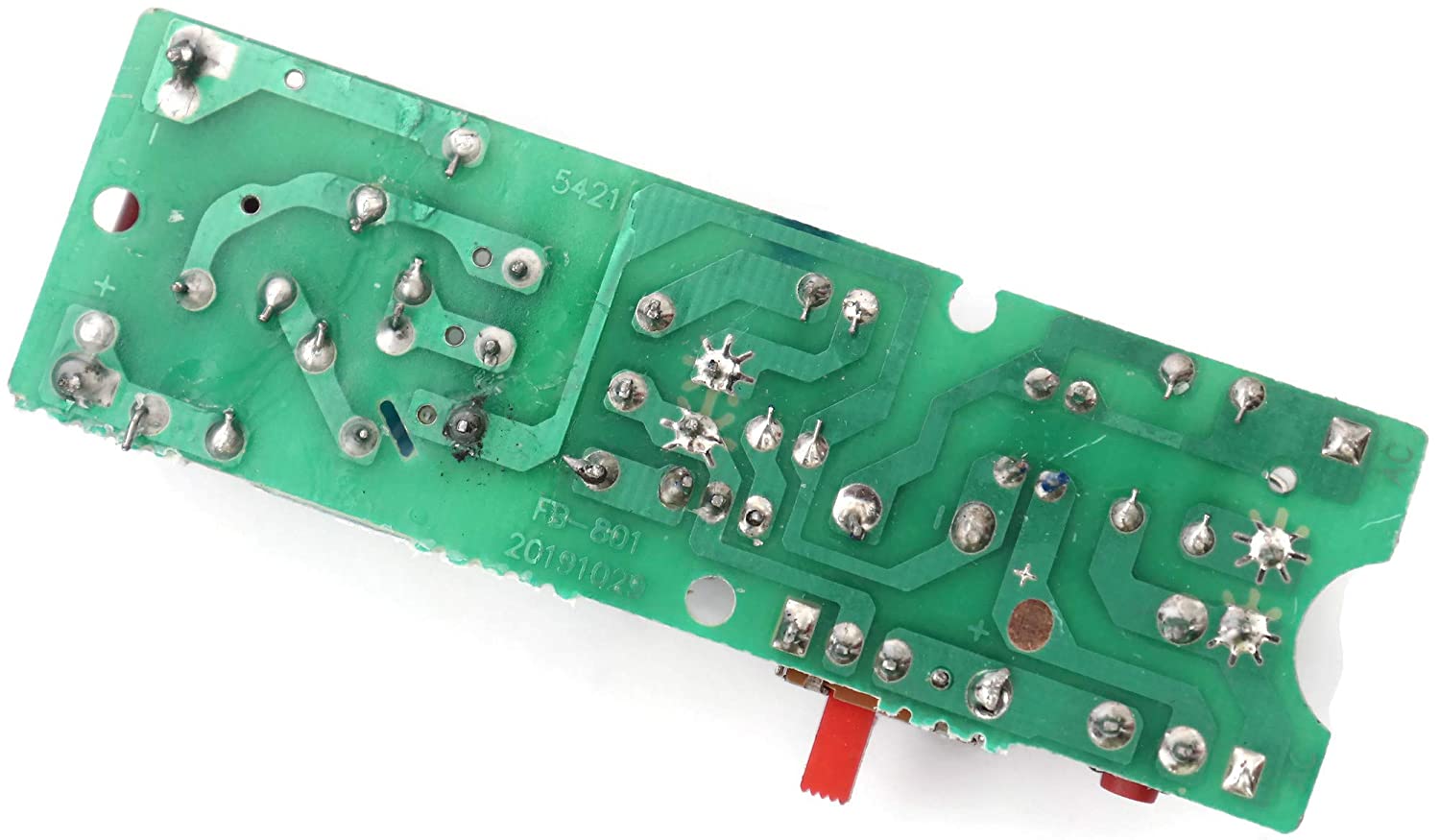
As one of the important process of PCB manufacturing, silk screen plays a role to affect the performance and quality of the finished boards. In this passage, we are going to tell you the working process of silk screen, please check and red the content for more professional information.
How to choose materials for silk screen?
Stencil
Stencil is the most important part of this process, this is because it is a key factor in controlling the flow and thickness of the printing ink, and it also determines the durability of silkscreen printing. In addition, stencil and the photosensitive materials have excellent combination is also an important factor in the production of high-quality, high-precision silkscreen printing. In order to ensure a good combination of stencil and photosensitive materials, the traditional approach is to the new stencil coarsening and degreasing treatment, so as to ensure the quality of the stencil, colleagues can also extend the service life of the stencil.
Light-sensitive Materials
Printing light-sensitive materials commonly used are diazo photosensitive agent, photosensitive film, etc. Diazo emulsion is widely used in silkscreen printing. The film thickness is uniform and controllable. High resolution image force, high resolution, wear resistance, strong adhesion with the screen and other characteristics, in the printed board character printing has been a wide range of the silkscreen printing process.
Stencil Frame
The material and section shape of the stencil frame is very important, relative to a certain specification of the stencil frame, if the stencil frame strength is not enough, it cannot ensure the consistency of tension. Now the general use of high tension aluminum stencil frame.
What is the key process of silk screen?
So how does Screen Printing work? Well, it’s not like DTG that’s for sure. Instead, a thin mesh is stretched tightly over a frame (originally the screen was made from silk, however, mostly made from polyester today). A negative of the design is printed onto the screen to be placed against the shirt. Once set correctly, ink is rolled over the screen, only the areas where the design has been printed allows ink to slip through. The ink then sets on the t-shirt and is put aside to dry.
We’ll be honest with you, it’s a lot more complicated than that. There’s a lot of separate chemicals, inks, and techniques that go into making your shirts, but that’s the jist. While it may not be as quick as DTG printing, it can result in a thick and bold design.
Silkscreen Printing Process overview:
Make soldering film negative → Punch position holes for the film negative → Surface cleaning → Configure printing ink → Print both sides of PCB → Preheat the board → Exposure → Develop → Hot-set
Preheating
Preheating is to evaporate the solvent contained in the ink, so that the soldering film becomes a non-sticky state. For the different ink, its preheating temperature, time is not the same. If the preheating temperature is too high or the drying time is too long, it will lead to poor development and reduce the resolution. Of course, if the preheating time is too short or the temperature is too low, the film will stick to when it is on the exposure, and then, in the development stage, the solder resistance film will be eroded by the sodium carbonate solution, which will result in the loss of luster on the surface or expansion and peeling of the solder resistance film.
Exposure
Exposure is the key to the whole process. In the case of positive images, due to light scattering, soldering film on the edge of the graph or line reacts with light (mainly photosensitive polymer in the soldering film reacts with light) to generate residual film in the case of overexposure, resulting in reduced resolution, smaller graphics and thinner lines. If the exposure is insufficient, the result is contrary to the above situation: the developed figure becomes larger and the line becomes thicker. This situation can be reflected by the test that if the exposure time is long, the measured line width is negative tolerance. On the contrary, if the exposure time is short, the measured line width is positive tolerance. In the actual process, the "light energy integrator" can be used to determine the best exposure time.
Ink Viscosity Regulation
Liquid photoresist ink viscosity is mainly controlled by the ratio of hardener and main agent and the amount of diluent added. If the amount of hardener added is not enough, may produce ink characteristics of the imbalance. After the hardener is mixed, it will react at room temperature. The viscosity changes are as follows.
Within 30min: the ink main agent and hardener have not fully integrated, liquidity is not enough, which will block the stencil when printing.
30min~10h: ink main agent and hardener have been fully integrated, the flow is appropriate.
After 10h: the ink itself has been the reaction between the material has been active, resulting in greater fluidity, it is not easy to print, the longer the hardener mixture of time, resin and hardener reaction is more adequate, then the ink gloss is also better. In order to make the ink gloss uniform, good printing, it is best to mix the hardener after 30 minutes to start printing.
If the thinner added too much, it will affect the heat resistance and hardening of ink. In short, liquid photosensitive soldering ink viscosity regulation is very important. For example, if the viscosity is too thick, silkscreen printing is difficult. If the viscosity is too thin, the amount of volatile solvent in the ink is more, which will be more difficult to precure.
Industry Category