How to Calculate PCB Price during the Manufacturing Process?
By:PCBBUY 01/18/2022 09:28
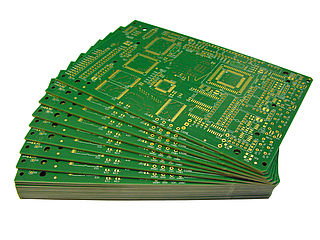
It continually faces stiff competition and regulations. The PCB Manufacture processing itself is driven by many variables that can independently affect the overall board price. Manufacturers and the users control some of the factors that affect the cost. But then, some elements are beyond the reach of both. Among such factors are conditions like exchange rates, utility tariffs, material cost, among many others.
In this passage, check and read the content below for more information about calculating PCB price.
What factors affect PCB cost?
To calculate the cost of PCB, it is necessary to know the manufacturing process and estimate the factors that affect PCB cost.
Material Choice
The materials used in a circuit board will invariably affect its cost.
The factors that can impact material selection include:
Thermal Reliability: Will the board be capable of performing under the range of temperatures expected for the tasks in question? Certain boards require materials of a higher thermal rating than standard boards.
Temperature Reliability: Can the material withstand an expected range of atmospheric conditions within a controlled setting without overheating? PCBs intended for high-temperature working operations require materials that pass these tests.
Heat Transfer: Will the board withstand high-intensity loads without transferring undue levels of heat to attached and adjacent components? The right material will need to pass this test for the uses in question.
Signal Performance: Will the material facilitate uninterrupted electrical signals throughout each operating cycle of a given machine? Will the signal withstand a necessary range of temperatures and other environmental factors? These concerns are integral to the performance of a PCB.
Mechanical Properties: Does the material have sufficient physical composition to withstand a plausible range of physical stresses? Can the board be pressed into a tight slot without cracking?
PCB Size
The size of a PCB and its panel utilization are two of the most crucial factors that affect the price. The size of a board will generally be determined by the number of circuits required for the corresponding device.
A PCB in something as small as a digital watch will require fewer components and ultimately be less costly to produce than a computer or laptop PCB. Likewise, the PCB in a large piece of industrial machinery will be larger than the boards contained in most home electronics.
The amount of space consumed by components on a board will also affect the price. Granted, some boards are designed with less consideration of efficiency and production costs.
What are the methods to reduce the PCB cost?
Reducing the cost of printed circuit boards is really about keeping things simple and effective, designed to achieve your goals and your needs in as direct a way as possible. PCBs are usually seen as a complex dance of getting everything to fit in the smallest space or trying to space everything out as much as possible to make them easy to read.
There is indeed a happy medium somewhere. You can reduce the cost of PCBs by looking for this middle ground. In this piece, we’ll present seven of those in-between spaces for reducing the cost of printed circuit boards.
Reduce Complexity
One of the easiest ways to reduce the cost of PCBs is to create a simple board and review your design to optimize it. Look for many different design options to make sure your board is as simple as possible. Not only do you want to optimize the elements of your board but you’ll also want it on a small form factor that still provides appropriate clearance for every element.
Size It Right
That clearance isn’t just about its relationship to other parts, but also for the assembly process. If your board is complex and tiny, it will take the manufacturer more time and effort for their assembly line to put your board together.
Getting very small and tight is going to get expensive. Save space when possible, but don’t narrow down so much that it takes multiple runs to put each board together. If you’re struggling with that spacing, remember that using common shapes is a way to reduce the costs of PCBs.
If it is possible, make your board a square or a rectangle. Complex shapes raise costs, especially if they’re very irregular.
Keep It Consistent
Reducing the cost of printed circuit boards gets a little easier if you have large orders or are getting multiple boards together. If you keep the overall board shape the same or have consistency in your overall design, you’ll be able to shave some costs off your whole order.
Avoid Slots if Possible
Reducing the cost of printed circuit boards also comes with what you skip. Avoid internal cutouts unless you absolutely must have them to mount the PCB. Many people will charge you more when they have to cut a slot or do other cutouts in your boards. Some designers like the look and try to create something unique but uniform, which can be engaging for engineers but likely won’t make a significant difference in your functionality or brand recognition.
Industry Category