How to Calculate Thermal Conductivity of PCB?
By:PCBBUY 08/21/2021 09:24
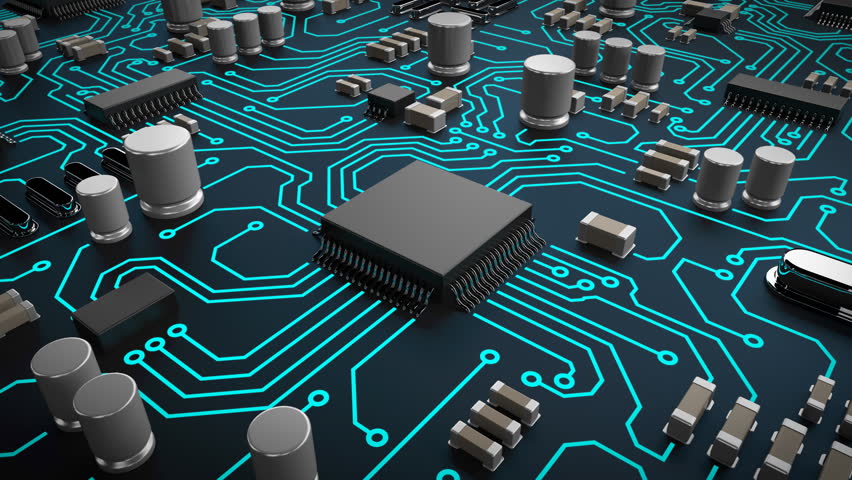
Many mass-manufactured boards will be placed on FR4, which has very low conductivity compared to a number of alternative materials. The thermal conductivity of a PCB substrate is often considered an afterthought. There are a number of design tradeoffs that should be considered when choosing a substrate that spans beyond thermal conductivity, and you might be better off using a substrate with low thermal conductivity alongside some passive or active cooling methods.
In this article, we will talk about thermal conductivity of PCB. If you are going to learn more PCB knowledge, please check and read the content we provide for more information.
Why thermal conductivity is important to PCB?
Heat management is crucial for PCB performance, reliability, and longevity. Inadequate heat management may lead to delamination, damage, or device failure (Figure 2). Thermal conductivity plays a vital role in heat management, and thus it is a key parameter for PCB design. The C-Therm Trident thermal conductivity platform is a useful tool in obtaining rapid, precise, and accurate measurements of PCB component thermal conductivity.
The “hot” topic in PCB design is high-speed signal integrity. But on another front, PCB designers may be interested in how hot (literally) an individual PCB trace becomes. Trace temperature is directly related to reliability. In the extreme, a trace that is too hot can melt the solder or cause a board to delaminate. But generally we want trace temperatures to be a lot lower than that. The trace reaches a stable temperature when the heating of the trace equals the cooling of the trace. The heating of the trace is caused by the I2R (power) drop across the trace. It is only in the last 10 years that the industry has recognized the importance of the dielectric in the trace cooling process.
How does thermal conductivity influence PCB?
Choosing a substrate with an appropriate thermal conductivity is one of many important aspects of PCB design. Thermal management in PCBs becomes particularly important in smaller boards with active components that switch at high speed. It is also important in boards that will carry high current as resistive losses in a trace will generate heat, which then transfers into the substrate.
If you know that your board will generate a large amount of heat during operation, or if your board will operate in a high-temperature environment, then you may need to use a substrate with higher thermal conductivity. You may also need to implement passive cooling, active cooling, or both in order to keep the temperature of important components within their safe operating range. It is also important.
Component Size
As components become smaller, so does the ability to dissipate heat naturally. For example, a MOSFET with a SOT-23 package will have less area for its heat pad than one in TO-220. Therefore, the size of components mounted on a PCB will influence its ability to propagate heat.
Thermal Vias
Thermal vias are holes intentionally placed to dissipate heat off a component. It’s kind of like providing more opportunity for the steam to escape from your porridge instead of trapping it in a container. So, naturally, this means that the more thermal vias there are in an area, the more they will increase the effective thermal conductivity of a PCB.
Internal Layers
The presence of internal copper layers can also change the rate and direction of heat dissipation. The thermal conductivity for copper is 355 W/m-K, while FR-4 is 0.25 m-K. With multiple inner-layers of copper, the effective thermal conductivity of the PCB would decrease. Of course, the presence of thermal vias could help to move the heat to the inner layers more efficiently.
How to calculate thermal conductivity of PCB?
As a fundamental property of any material, thermal conductivity defines the heat flux between hot and cold regions in your PCB. The thermal conductivity of your substrate material can be found in material datasheets. However, once you have an idea of your stackup and copper weight in your layout, you will want to calculate the effective thermal conductivity of your substrate. Formulas for calculating this directly vary depending on who you ask, although there are a number of lumped models in the literature. The simplest method is to use a weighted average based on the volume of copper and substrate material in your PCB:
Effective thermal conductivity estimation
Effective thermal conductivity estimate based on a volume weighted average of your PCB material parameters
The above equation shows a simple volume weighted average for calculating the effective thermal conductivity, where “s” indicates the substrate and “c” indicates copper. However, this is just a rough estimate, and you’ll get much more accurate results if you use a specialized 3D multiphysics simulator. Once you’ve determined the effective thermal conductivity of your PCB, you’re ready to calculate the thermal resistance in your board, which will give you some idea of how heat will transfer through your stackup.
What is effective thermal conductivity of PCB?
Effective thermal conductivity refers to the ability of a material to conduct and transfer heat. When we’re talking specifically about a PCB’s effective thermal conductivity, we’re talking about how well the PCB can move the heat generated from its components to its surrounding area. Effective thermal conductivity is represented by the symbol and values are expressed in W/m•K.
In PCB design, effective thermal conductivity is an important aspect used in thermal modeling and analysis because it allows engineers to predict how well a populated PCB would conduct heat based on specific assumptions and models. With electronic modules continuing to shrink in size, it is a parameter that deserves attention amongst designers.
Industry Category