How to Calculate Thermal Resistance of PCB?
By:PCBBUY 01/15/2022 09:23
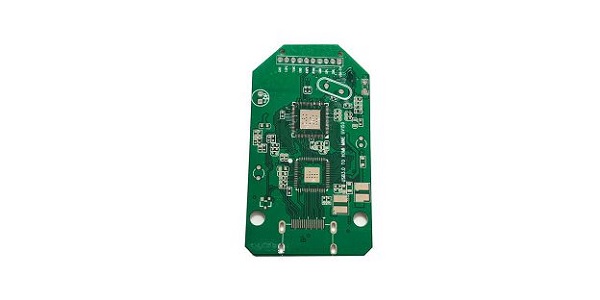
With the right circuit board substrate material and component choices, you can devise a thermal management strategy that can help control heat transport in your board. Using proper arrangement of copper elements, components, and interior plane layers, your thermal management strategy can remove transport heat away from each heat source and bring your printed circuit board temperature closer to ambient temperature. You should inform these design choices through measurements of thermal resistance of your PCB and try to reduce the thermal resistance as much as possible.
In this passage, we will provide all the information of thermal resistance of PCB. If you are searching for the professional knowledge of thermal resistance of PCB, please check and read the content below.
What is the basic definition of PCB thermal resistance?
Thermal conductivity is sometimes incorrectly interchanged with thermal resistance. Just like resistivity and conductivity of electrical components have an inverse relationship, the same goes for PCB thermal conductivity and thermal resistance. The thermal resistance of your PCB is determined by the material properties of your substrate and the arrangement of copper elements in your board. Overall, this defines the rate of heat transfer between hot a cold regions of your PCB.
As copper is a conductor, it also has high thermal conductivity (this is the case with most electrically conductive materials), and the copper elements in a printed circuit will provide a low thermal resistance path for heat to move away from a heat source. As the thermal conductivity of FR4 and other common substrates is quite low, copper in a printed circuit will transport heat through the board much faster than heat will naturally conduct through the substrate. This combination of a high thermal resistance material (FR4) and a low thermal resistance material (copper) determines the effective thermal conductivity of a printed circuit board.
What is the function of PCB thermal resistance?
Heat management plays a crucial role in keeping components cool during operation. Arguably, FR4 is the commonest substrate material. However, it features a low thermal conductivity. This causes heat to remain close to hot components. Overheating in electronic devices can cause damage. Therefore, the need for a thermal management strategy. This will help dissipate heat from important components.
Thermal resistance in printed circuit boards is very important. Heat sinks and FR4 are a crucial part of thermal management. However, it is important to design your board to ensure thermal resistance. PCB manufacturers must use the right materials to achieve this.
It is crucial to understand what thermal resistance is. FR4 thermal resistance depends on its thermal conductivity. FR4 conductivity enables the transfer of heat from a warmer area to a cooler area at a quicker rate. Hence, the PCB will have a lower thermal resistance.
The various components and parts on a circuit board contribute to thermal conductivity. These components all feature different thermal conductivity. Hence, they conduct heat at different levels. To determine a PCB thermal resistance, consider the thermal resistance in each component. Therefore, FR4 thermal resistance and low thermal resistance copper determine PCB thermal conductivity.
How to calculate PCB thermal resistance?
You are probably familiar with the terms thermal pad, thermal relief pad or thermal via. These all refer to connections to a copper plane (or pour) and impact thermal resistance. However, thermal relief pads are intended to evenly distribute heat to achieve a constant temperature and aid the soldering process, while thermal vias are intended to dissipate heat away from components. Thermal relief and via locations are determined by heat distribution and dissipation concerns. This contrasts with component or footprint pad layouts that are based on design preferences and DFM rules and guidelines for your contract manufacturer (CM), such as spacing and clearances.
Thermal reliefs also differ in primary function from other heat dissipation elements like heat sinks, which are intended for operational usage. Reliefs are intended to aid in board manufacturing, specifically printed circuit board assembly (PCBA) during the soldering of component steps. As such, they should be an essential part of your design for assembly (DFA) plan.
PCB Thermal Resistance
PCB thermal resistance may be broadly defined as the inverse of the board’s thermal conductivity, which along pure (≅ 100% Cu) copper through-holes is 386 W/m-K. To find the total thermal resistance for your board, you must include all layers of the board and the associated heat parameters for the type of material through which heat will flow. There are several ways to determine your PCB thermal resistance explicitly; however, these can be quite cumbersome and are best performed with thermal analysis software.
For Thermal Vias
Resistance for thermal vias may be estimated as opposed to directly determined, using a calculator. For most PCB thermal resistance calculators, you will need to know the following:
· Trace (copper) thickness and thermal resistivity
· Laminate (insulation) thickness and thermal resistivity
· Substrate (core) thickness and thermal resistivity
With these parameters, you can estimate the PCB thermal resistance along any path by simply summing the values for the material(s) along the trace path.
Industry Category