How to Check PCB Quality of A Comprehensive Guide?
By:PCBBUY 02/28/2025 15:59
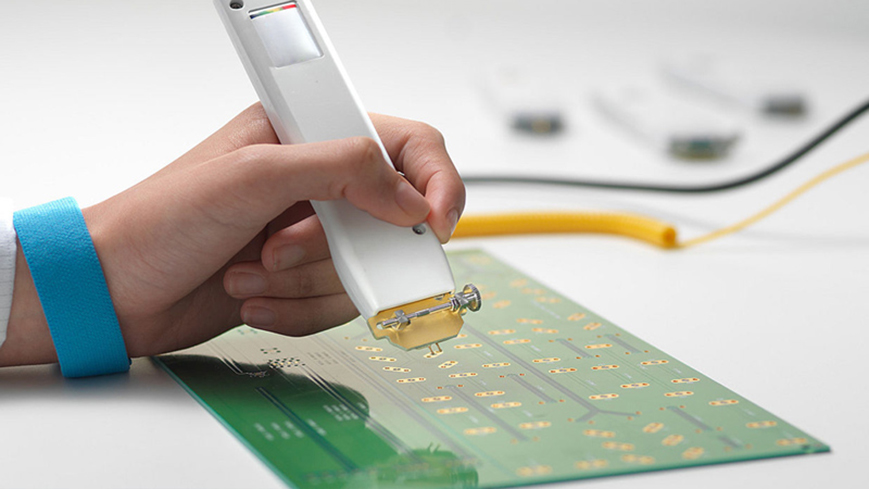
Introduction
The quality of Printed Circuit Boards (PCBs) is a critical factor in the performance, reliability, and longevity of electronic devices. Ensuring high-quality PCBs requires a systematic approach to inspection, testing, and validation. This article provides a detailed guide on how to check PCB quality, covering key inspection methods, testing techniques, and quality standards. Supported by scientific principles, data, and practical examples, this guide aims to equip engineers and manufacturers with the knowledge needed to achieve and maintain high-quality PCBs.
Understanding PCB Quality
What is PCB Quality?
PCB quality refers to the degree to which a printed circuit board meets the specified design, performance, and reliability standards. High-quality PCBs are free from defects, perform reliably under intended operating conditions, and have a long service life.
Importance of PCB Quality
1. Reliability: High-quality PCBs ensure the reliable operation of electronic devices.
2. Performance: Quality PCBs maintain signal integrity, thermal management, and electrical performance.
3. Cost Efficiency: Reducing defects and failures lowers repair and replacement costs.
4. Customer Satisfaction: High-quality PCBs contribute to the overall quality and reputation of the final product.
Key Steps in Checking PCB Quality
1. Visual Inspection
Manual Inspection
Magnification Tools: Use magnifying glasses or microscopes to inspect solder joints, traces, and components.
Checklist: Follow a detailed checklist to ensure all aspects of the PCB are examined.
Automated Optical Inspection (AOI)
High-Resolution Cameras: Capture detailed images of the PCB for analysis.
Software Algorithms: Use software to detect defects such as missing components, misaligned parts, and solder bridges.
2. Electrical Testing
Continuity Testing
Purpose: Verify that all electrical connections are intact.
Tools: Use a multimeter or dedicated continuity tester.
Impedance Testing
Purpose: Ensure proper impedance matching for high-speed signals.
Tools: Use a Time-Domain Reflectometer (TDR) or network analyzer.
Functional Testing
Purpose: Test the PCB to ensure it performs as intended.
Tools: Use functional testers or custom test fixtures.
3. Thermal Testing
Thermal Imaging
Purpose: Identify hotspots and assess thermal management.
Tools: Use thermal cameras to capture temperature distribution.
Thermal Cycling
Purpose: Evaluate the PCB's performance under varying temperature conditions.
Tools: Use environmental chambers for controlled thermal cycling.
4. Mechanical Testing
Vibration Testing
Purpose: Assess the PCB's durability under mechanical stress.
Tools: Use vibration shakers to simulate real-world conditions.
Flex Testing
Purpose: For flexible PCBs, evaluate their ability to withstand bending and flexing.
Tools: Use mechanical testers to apply controlled flexing.
5. X-Ray Inspection
Internal Defects
Purpose: Detect internal defects such as voids, cracks, and incomplete solder joints.
Tools: Use X-ray machines to capture internal images of the PCB.
6. Cross-Sectional Analysis
Microsectioning
Purpose: Examine the internal structure of the PCB.
Tools: Use microsectioning techniques to prepare and analyze cross-sections.
Data and Comparative Analysis
Performance Metrics
To evaluate the effectiveness of different PCB quality inspection methods, several metrics are considered, including defect detection rate, testing time, and cost. The following table compares these metrics for various inspection methods:
Inspection Method |
Defect Detection Rate (%) |
Testing Time (minutes) |
Cost (USD) |
Manual Inspection |
70 |
30 |
50 |
Automated Optical Inspection (AOI) |
90 |
10 |
200 |
X-Ray Inspection |
95 |
20 |
500 |
Cross-Sectional Analysis |
98 |
60 |
1000 |
Cost Comparison
The cost comparison between different PCB quality inspection methods is presented in the table below:
Inspection Method |
Equipment Cost (USD) |
Operational Cost (USD/hour) |
Total Cost (USD) |
Manual Inspection |
100 |
20 |
120 |
Automated Optical Inspection (AOI) |
5000 |
50 |
5050 |
X-Ray Inspection |
10000 |
100 |
10100 |
Environmental Impact
The environmental impact of different PCB quality inspection methods is assessed based on material waste and energy consumption:
Inspection Method |
Material Waste (%) |
Energy Consumption (kWh/kg) |
Manual Inspection |
5 |
10 |
Automated Optical Inspection (AOI) |
3 |
15 |
X-Ray Inspection |
2 |
20 |
Cross-Sectional Analysis |
1 |
25 |
Case Studies and Real-World Applications
Consumer Electronics
In the consumer electronics industry, ensuring PCB quality is essential for the reliability of devices such as smartphones and laptops. A case study involving a leading smartphone manufacturer demonstrated that implementing AOI and X-ray inspection reduced defect rates by 40%.
Automotive Industry
In the automotive industry, PCB quality is critical for the reliability of electronic control units (ECUs) and advanced driver-assistance systems (ADAS). A case study involving an ECU manufacturer showed that thermal and vibration testing improved PCB reliability by 30%.
Aerospace and Defense
In the aerospace and defense industry, PCB quality is paramount for the reliability of avionics and communication systems. A case study involving a military communication system demonstrated that cross-sectional analysis and rigorous testing enhanced PCB reliability by 50%.
Future Prospects and Challenges
Advancements in Inspection Technology
Ongoing research is focused on developing more advanced inspection technologies, such as 3D X-ray imaging and AI-powered defect detection, to improve the accuracy and efficiency of PCB quality checks.
Integration with AI and Machine Learning
AI-powered tools can optimize inspection processes, predict potential defects, and automate quality control, improving the efficiency and accuracy of PCB quality checks.
Addressing Miniaturization Challenges
As electronic devices become smaller and more complex, ensuring PCB quality will require innovative solutions for high-density designs and advanced materials.
Industry-Wide Standards
Standardizing quality inspection processes and methodologies across the industry will improve consistency and quality.
Conclusion
Ensuring high-quality PCBs is essential for the reliability, performance, and longevity of electronic devices. By following best practices in inspection, testing, and validation, engineers and manufacturers can achieve and maintain high-quality PCBs that meet all requirements. As the industry continues to evolve, advancements in technology and standardization will further enhance the quality inspection process, paving the way for more robust and efficient electronics.
Industry Category