How to Check PCB Soldering during the Manufacturing?
By:PCBBUY 02/16/2022 10:51
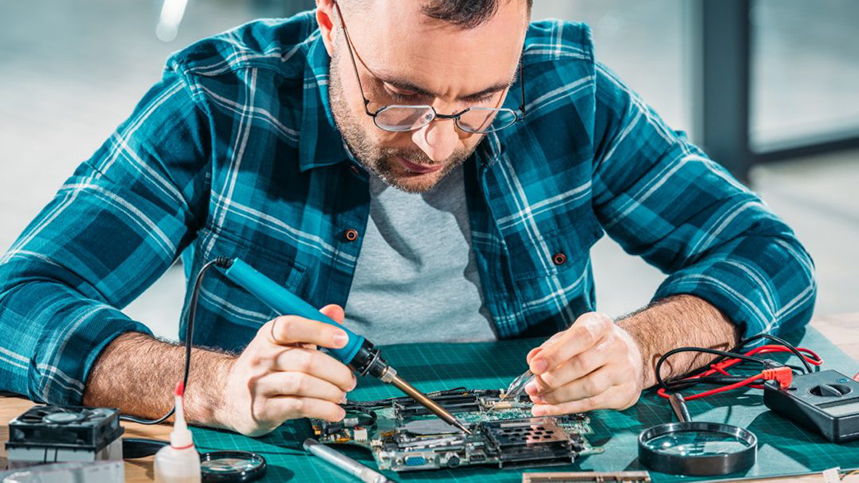
High reliability assembled PCB prototypes as well as novel surface mounted devices (SMD) and mixed systems must be assessed according to well defined qualification test plans. Such high reliability verification programmes are not limited to just evaluate the robustness, reliability and performance of the product but they also address the verification of tools, fabrication procedures and involved materials, as well as the confirmation of product integrity. For instance, “European Cooperation for Space Standardization” (ECSS) standards used in space programs
In this passage, we are looking for more information about PCB soldering, if you are searching for more professional knowledge, please check and read the passage.
What are the essential factors in PCB soldering?
Solder Paste Printing technology primarily aims to solve problems concerning incompatibility of solder paste printing amount (filling amount and transferring amount of solder paste). Based on professional statistics, with PCBs correctly designed, 60% of PCBs for rework are caused as a result of bad solder paste printing. In solder paste printing, three important "S"s must be remembered: solder paste, stencil and scraper. If correct selections are made, excellent printing effect can be obtained.
Quality of solder paste
As a necessary material for reflow soldering, solder paste is a kind of paste solder evenly mixed by alloy powder and paste flux (rosin, diluents, stabilizer etc.) among which alloy powder is the key element to composition of solder joints. Flux is the critical material to eliminate surface oxidation, increase wettability and ensure quality of solder paste. In terms of quality, generally speaking, 80% to 90% of solder paste belongs to metal alloy while it accounts for 50% in terms of volume. Solder paste quality insurance comes primarily in two aspects: storage and application. Solder paste is usually stored between 0 and 10°C or stored according to requirement of manufacturers.
Stencil design
The key function of stencil lies in uniform solder paste coating on PCB pad. Stencil is a must-be in printing technology and its quality directly influences quality of solder paste printing. Up to now, there are three methods to manufacture stencils: chemical corrosion, laser cutting and galvanoformung. Stencil design won't be ensured until the following aspects are fully considered and suitably dealt with.
What are the features of soldering finished PCB?
Although it is possible for anyone to throw down solder onto PCBs, whether you get classy solder joints or downright caveman quality ones is a different matter altogether. With components becoming smaller and more compact, the chances of soldering issues occurring have become higher. When soldering the PCB, try to make the finished product have the following characteristics:
· The soldering surface is kept clean;
· The solder joints must have sufficient mechanical strength to prevent the soldered parts from falling off or loose under vibration or impact;
· The soldering must be reliable and ensure electrical conductivity This is not only a guarantee for the product’s function but also to prevent the product from being burned out by a short circuit.
What are the preparations before of PCB DIP soldering?
First Article Inspection
We will cross check and record all the supplied components’ quantity, item number, dimension, cathode direction, component silkscreen number, value, etc.
Components outline processing
Some components outline should be processed ahead of time because of their own design or for the PCB DIP soldering requirements and the whole PCB plan.
Requests. The horizontal witch of the processed pins should be the same as the locating holes, the tolerance should be < 5%, the silkscreen upward.
Components management
Preparation before DIP soldering: Every operator should follow team leader’s arrangement, prepare their WI content in their own station and receive all the components which match the WI completely. Put the received components into the part box and mark them well, including the defect parts if there is. Check if there is any cathode components, and compare with the WI picture, should be familiar with the part appearance and find out the pin position.
Industry Category