How to Choose the Right Material for PCB Insulation?
By:PCBBUY 03/25/2025 16:16
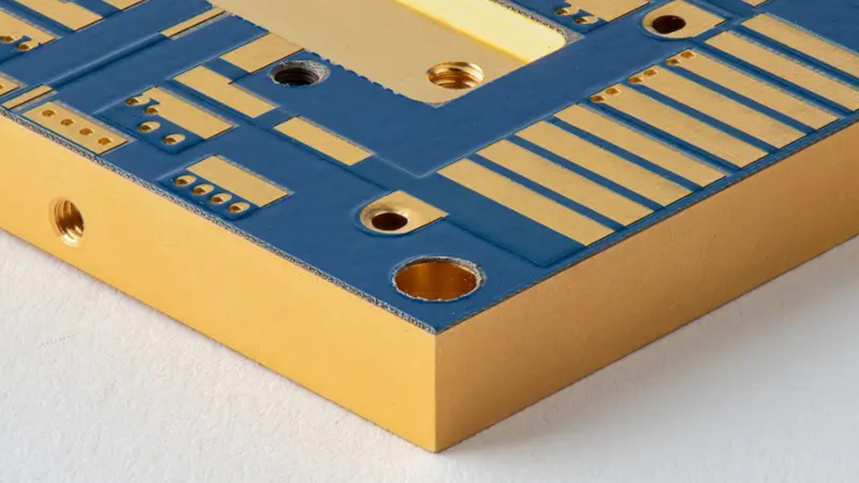
Printed Circuit Boards (PCBs) serve as the backbone of modern electronics, enabling the interconnection and functioning of various components. A critical yet often overlooked aspect of PCB design is insulation—the material that provides electrical isolation between conductive elements while maintaining thermal stability and mechanical integrity. This article will explore the principles, materials, and considerations involved in choosing the right insulation for PCBs, supported by reliable data and comparisons.
Understanding PCB Insulation: The Basics
What is PCB Insulation?
PCB insulation refers to the dielectric materials that separate conductive layers and elements within a PCB. These materials prevent short circuits, ensure signal integrity, and enhance the overall reliability of the circuit.
Importance of Insulation in PCBs
The role of insulation in PCBs is multifaceted, including:
-
Electrical Isolation: Preventing unintended electrical paths.
-
Thermal Stability: Managing heat dissipation to avoid component damage.
-
Mechanical Support: Providing structural integrity to withstand environmental stresses.
-
Signal Integrity: Reducing electromagnetic interference (EMI) and cross-talk between circuits.
Key Factors to Consider When Choosing Insulation Material
Selecting the right material for PCB insulation depends on several critical factors:
1. Dielectric Constant (εr)
The dielectric constant affects signal propagation and impedance. A low εr value is preferred for high-frequency applications to minimize signal loss.
Material |
Dielectric Constant (εr) |
Typical Application |
FR-4 |
4.5 |
General-purpose PCBs |
PTFE |
2.1 |
High-frequency PCBs |
Polyimide |
3.5 |
High-temperature PCBs |
2. Thermal Conductivity (k)
Efficient heat dissipation is essential to prevent overheating, especially in high-power or densely packed PCBs. Materials with high thermal conductivity are ideal.
Material |
Thermal Conductivity (W/mK) |
FR-4 |
0.3 - 0.4 |
Ceramic-filled |
>2.0 |
Polyimide |
0.4 - 0.5 |
3. Glass Transition Temperature (Tg)
Tg is the temperature at which the insulation material transitions from a rigid to a rubbery state. A higher Tg ensures better performance in high-temperature environments.
Material |
Tg (°C) |
FR-4 |
130-180 |
Polyimide |
>250 |
PTFE |
200-260 |
4. Coefficient of Thermal Expansion (CTE)
Low CTE values are crucial to avoid warping or cracking during thermal cycling.
Material |
CTE (ppm/°C) |
FR-4 |
14-17 |
Polyimide |
~10 |
PTFE |
30-50 |
5. Environmental and Regulatory Compliance
The insulation material must meet industry standards such as RoHS, REACH, and UL94 for safety and environmental sustainability.
Common PCB Insulation Materials and Their Properties
1. FR-4 (Flame Retardant-4)
-
Composition: Epoxy resin reinforced with woven glass fabric.
-
Applications: Widely used in consumer electronics and general-purpose PCBs.
-
Advantages: Low cost, good mechanical strength, and moderate thermal stability.
-
Limitations: Not suitable for high-frequency or extreme-temperature applications.
2. Polyimide
-
Composition: Synthetic polymer with excellent thermal stability.
-
Applications: Aerospace, automotive, and high-temperature PCBs.
-
Advantages: High Tg, low CTE, and resistance to chemicals.
-
Limitations: Higher cost compared to FR-4.
3. PTFE (Polytetrafluoroethylene)
-
Composition: Fluoropolymer with exceptional dielectric properties.
-
Applications: High-frequency and RF PCBs.
-
Advantages: Low εr and excellent thermal resistance.
-
Limitations: Difficult to process and expensive.
4. Ceramic-Filled Substrates
-
Composition: Ceramics combined with organic polymers.
-
Applications: High-power and microwave PCBs.
-
Advantages: High thermal conductivity and low thermal expansion.
-
Limitations: Brittle and costly.
Practical Guidelines for Material Selection
Step 1: Define Application Requirements
Identify the electrical, thermal, and mechanical needs based on the application.
Step 2: Evaluate Material Trade-offs
Use data tables and comparisons to balance cost, performance, and manufacturability.
Step 3: Perform Simulation and Testing
Run simulations to predict performance under operational conditions, followed by prototyping and testing.
Step 4: Ensure Regulatory Compliance
Verify that the chosen material meets industry and environmental standards.
Case Study: Material Selection for High-Frequency PCB
A company designing a 5G base station PCB required insulation with the following:
-
Dielectric constant: <3.0
-
Tg: >200°C
-
Thermal conductivity: >1.0 W/mK
After evaluation:
-
FR-4: Insufficient due to higher εr and lower Tg.
-
PTFE: Chosen for its low εr and high thermal stability.
Simulation results:
Parameter |
FR-4 |
PTFE |
Signal Loss (dB) |
-2.0 |
-0.5 |
Thermal Stability |
Moderate |
High |
Cost |
Low |
High |
Conclusion
Choosing the right material for PCB insulation is critical for ensuring the performance, reliability, and longevity of electronic devices. By understanding the properties and trade-offs of various materials, engineers can make informed decisions tailored to specific applications. Incorporating advanced simulations and adhering to industry standards further enhances the design process.
References
-
IPC-4101: Specification for Base Materials for Rigid and Multilayer Printed Boards.
-
UL94 Standards for Flammability of Plastic Materials.
-
Rogers Corporation. "High-Frequency Laminates."
-
Lee, C. H., & Kim, S. "Thermal Conductivity of Polyimide Films," Journal of Applied Polymer Science, 2021.
-
IEEE Standards Association. "PCB Material Guidelines for High-Speed Circuits."
Industry Category