How to Clean Flux off PCB Step by Step?
By:PCBBUY 01/14/2022 09:34
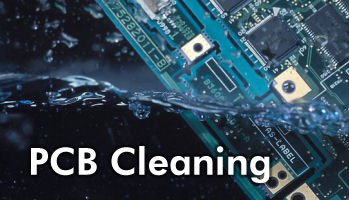
Encapsulated harmful residues from the no-clean soldering process could be released from rosin/resin when the PCB (printed circuit board) is cleaned only partially. Flux is used when soldering electrical components to a printed circuit board. Depending on the components and type of solder used, flux is applied to solidify the electrical connection.
The residue left by applying flux paste, or solder flux is usually removed to prevent inhibition of printed or etched wiring, and to avoid obscuring other components. Removing flux from a PCB is a simple task. If you are looking for more about flux off PCB, please check and read the content below.
Why We Need to Clean Flux from PCB
Printed circuit boards, commonly referred to as PCBs, are not only found in electronic gadgets but can also be bought for custom usage. By custom usage, it means you can get one of those PCBs and try different customized circuits by soldering electrical components onto the board. In most cases, solidifying such a soldered electrical connection requires the use of flux. After all, is done, you need to clean the flux before assembling the components.
Improve the Reliability of PCB
The reliability of an item is solely driven by the nature of the final product. With computer keyboards, no one loses a life if it stops functioning. In such a case, an EMS supplier can forgo the cleaning process and use no-clean flux. On the other hand, board failure could even lead to death requiring strict requirements. In such a case, cleaning should be done after assembling the components, a process that requires thorough testing for effectiveness.
Prevent Corrosion On the PCB
The flux residues left on the circuit boards are acidic. If left to sit on the board for long, they draw in moisture from the air, leading to corrosion of the components on the PCB. You can also place your PCB safe from pollution by setting them in enclosures or apply a conformal coating that will prevent air from being trapped into the board. With the coating, moisture can escape on the underside. The only disadvantage of this coating is that if you need to work on your PCB again, you will need to strip it off and reapply a fresh coating.
Improving the Aesthetic Appearance of the PCB
The visual appearance of a PCB translates into a manufactures work. A greasy looking residue on your PCB around the components can raise questions among your customers. If there are flux residues on the board, your customers might see it as a defect in your work, which would be turn off.
Avoid Adhesion Problems with Conformal Coating
The conformal coating might be the right solution for preventing corrosion, but if some flux residues are left on the PCB before the coating process, it can start to lift from the board. It is more evident if the pockets are further apart, not just on the overall surface. The coatings can be semi-permeable, meaning they can breathe to an extent some moisture can enter and settle on the flux residue and lead to corrosion.
How to clean off the flux off PCB?
Cleaning using Acidic Brush
It is doubtless the most economical PCB flux cleaner. This cleaning method uses tools such as an acid brush, liquid spray can, solvent, and a paper wipe. Isopropyl alcohol is the favorite solvent due to its cost-effectiveness and also how easy it is to get it. It also dries up on the PCB after use. The process requires a few steps that include:
· Cut the acidic brush to angle the wire to have both small and extended sides. The smaller side is important for scrubbing the PCB. The extended side is to take out the flux from areas that are difficult to reach.
· Dip the brush into the chemical solvent and scrub the flux remnants away from the board. The area where the flux is could be wet.
· The cleaned area is then wiped by the paper to enable dryness of the solvent. The PCB is then clear and free from flux.
Your success rate of cleaning the soldering residues from the electrical components will depend mostly on the type of removal you use for the purpose. While several manufacturers produce some best flux remover using isopropyl, you can actually create a residual removal at home.
You will require the following things to make the homemade flux remover-
· 95% pure ethyl alcohol. It needs to be 850ml.
· 95% pure and tested 100ml isopropyl alcohol.
· Ethyl acetate solution of 50ml.
You can use a measuring bottle to measure the essential amount of the three chemical liquids correctly. It will help you achieve the desired proportion better. Since the purity of the chemical fluids is critical, always buy them from trusted shops.
Also, store them in the proper container and make sure the cap is sealed. Otherwise, air may contaminate the solutions. Furthermore, ethyl tends to evaporate if the lid is open.
Now let’s get into the mixing procedure. Thank god, it is secure.
Just take a proper mixing container, then, first, pour the ethyl alcohol on it. After that, add the isopropyl alcohol and ethyl acetate solution on it. That’s it, and your homemade flux remover is all set to go.
Since you won’t be using the entire liquid in a single go, pour some (approximately 100 ml of solution) in a spray bottle and use it. The mixture works on both resin and non-resin based flux as well as no-clean flux too.
Note: Always wear gloves before you handle the ethyl and isopropyl solutions and start mixing them. It helps you prevent unwanted happenings.
Industry Category