How to Decide Trace Width in PCB Design and manufacturing?
By:PCBBUY 06/25/2022 10:05
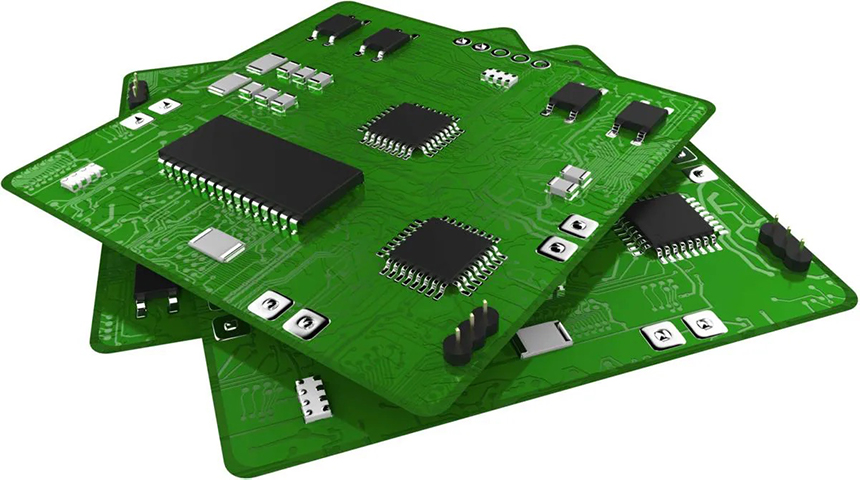
In today’s PCB layouts, each net may have different and unique routing characteristics that have to be applied to it in order for it to function as designed. In addition to specific areas that nets can be routed in or layers that they can be routed on, there are also different PCB trace width and spacing rules that have to be managed as well.
Do you know the methods of deciding trace width in PCB design? If you are searching for the information about ir, please check and read the content below for more knowledge.
What is the importance of determining PCB trace width?
During the production of PCBs, you may trace a PCB successfully and then later discover that it will not be able to carry the needed amount of current effectively. Consequently, the printed circuit boards intended application experiences a setback. This is due to the inadequate current capacity.
Making use of your PCB trace width calculator ensures the conductance of the right current value. Using this circuit calculator, you may utilize the highest current rating you desire to know the width of your trace. In addition, you may influence the rise in temperature which your PCB records. This is possible by making use of your PCB trace width calculator.
The important factors to consider when selecting a trace width include:
· The current capacity of the trace
· Space availability and manufacturing limitations
· Trace termination · Impedance
What are the rules of standard PCB trace width?
So far, we have looked at how trace width and spacing restrictions affect the performance of the board electrically, but there are also manufacturing concerns as well. Traces that are too close to each other or to other metal features of the board could potentially develop shorts during fabrication. Each fabricator will have its own minimum trace width that they will build, but 3 mils is a common minimum spacing value. Copper weight also must be factored in here as well.
Here are some other manufacturing considerations for trace width and spacing restrictions:
· Traces running between the pads under small surface mount components may have the minimum trace to metal spacing, but can still cause manufacturing problems. The part may not sit squarely resulting in tombstoning, or form a solder bridge with a trace and cause damage if the part is lifted for re-work.
· Metal that is too close to the edge of the board could present depanelization problems. Additionally, exposed copper could come into contact with other conductive elements and cause a short on the board.
· Traces that are too wide on the surface mount pads could form solder bridges with adjacent pads or traces. These could cause excess current or shorts.
· It is also important that drill hole sizes match the traces to which they connect. Although vias run through the board they serve the same function as traces that run along the surface. In many cases, they are extensions of them.
How to choose the right PCB trace width?
These trace width calculators will prompt you to enter design specifications such as the thickness of copper, the maximum amperage that will pass through the trace, the length of the trace, and the acceptable increase in temperature due to the resistance of the trace dissipating power. After entering these values you will be presented with a calculated trace width. It is important to note that this value is a minimum width required to meet the design criteria inputs.
Determining the width of a trace based on the current demands is important for most power traces and high power signals, however, most traces on PCBs pass signals which draw negligible current. For these low power signal traces, we must look at other characteristics of the PCB to determine the width.
The size of a PCB is directly connected to the cost of the PCB, so in general PCBs are kept as small as possible. The downside of reducing board size is that it can limit the available space to route traces. For low power signal traces it is generally advised to keep traces small to increase the available space available for routing. Excessively large traces consume valuable PCB space while offering highly diminished returns. 6 to 30 mils is typical for most signal trace widths.
MacroFab offers a minimum of 5mil traces as a standard and if smaller traces are required, the extended manufacturing option will allow traces all the way down to 3mil.
Industry Category