How to Design Aluminum PCB and Improve the Quality of Products?
By:PCBBUY 12/24/2021 10:10
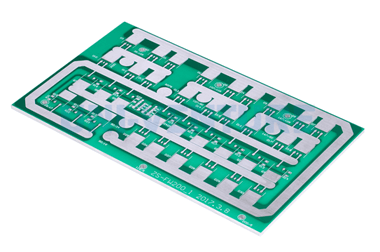
Since the emergence of aluminum PCB technology in the 1970s, several industries and individuals have augmented demand for production. Suppose you're planning on using applications that have heat dissipation and wish to control the temperatures. In that case, Aluminum PCB is the right choice for you.
How to design aluminum PCB? As a beginner of PCB industry, please check and read the passage to learn the information of aluminum PCB.
What is aluminum PCB used for?
Active components dissipate a significant amount of power, thus the use of a cooling fan on a CPU or other components with a large number of switching transistors. If the ambient temperature is excessively high, active cooling measures will only be useful for bringing the temperature of the board back down near the ambient level. In addition, you can only dissipate so much heat with active cooling. This is where some additional strategies need to be used to dissipate heat away from your active components.
Aluminum is one alternative material that can be used in the core of a PCB, commonly referred to using the misnomer “aluminum pcb”. Using aluminum as the metal core in a PCB allows it to easily dissipate heat away from active components thanks to its high thermal conductivity. The high thermal conductivity of aluminum or another metal in the core of a PCB allow heat to be distributed more uniformly throughout a board.
Contrast this with FR4, which is a relatively poor thermal conductor compared to a number of other alternative materials for PCB substrates. Hot spots on a PCB can form near active components, thus the use of active and passive cooling measures to dissipate heat and bring the temperature to a safe level. Heat generated from active components can also be transported away from the component layer and into an interior ground or power plane using thermal vias and lands.
In boards with an FR4 core, the ground/power planes are limited in the amount of heat they can transport around the board, as the cores have low thermal conductivity. Thermal vias and lands can help with heat dissipation, but other strategies often need to be used to bring the operating temperature of components down to a safe level.
What are the advantages of aluminum PCB?
Aluminum boards are one of the most thermally conductive PCB options. They keep as much heat away from vital components as possible to ensure minimal circuit damage. Thanks to their high heat tolerance, they can handle higher density circuits and larger power levels. Substrates created from aluminum alloys have a high level of physical durability that lowers the risk of breakage. Compared to other metals, aluminum has a lower environmental impact in addition to a reasonable cost.
On the other hand, aluminum PCBs tend to have more niche uses than standard boards. While they cost less than adding conductors to a copper board, they have a higher price than standard PCBs without those components. Investing in an aluminum core may not pay off if your application doesn’t involve high temperatures. If you plan on creating a flex circuit, an aluminum flex PCB can only flex into its initial position. It will bend to fit into smaller electronics, but it won’t withstand the stress of vibration.
Low Cost
Aluminum is a metal that can be found in a variety of climates, so it is easy to mine and refine. Therefore, the costs of doing so are significantly lower than other metals. In turn, this means that manufacturing products with these metals are less expensive as well.
Environmentally Friendly
Aluminum is non-toxic and recyclable. Manufacturing with aluminum is also conducive to conserving energy due to its ease of assembly. For printed circuit board a supplier, using this metal helps maintain the health of our planet.
What are the classifications and features of aluminum PCB?
Aluminum PCBs are essentially divided into three categories.
· Universal Aluminum PCB: the dielectric layer used here is made up of epoxy glass fiber pre-preg.
· High Thermal-Conductive Aluminum PCB:the dielectric layer is made up of epoxy resin. The resin used must have high thermal conductivity.
· High-frequency Aluminum PCB:the dielectric layer is composed of polyolefin or polyimide resin glass fiber pre-preg.
Thermal Dissipation
The performance of aluminum PCBs while dissipating heat is quite well as compared to ordinary FR4 PCBs. For example, a FR4 PCB that is 1.5mm thick will have thermal resistance of 20-22 degrees per watt whiles a aluminum PCB 1. 5mm thick will have a thermal resistance of 1-2 degrees per watt.
Thermal Expansion: each substance has its own coefficient of thermal expansion. The CTE of aluminum (22ppm/C) and copper(18ppm/C)is quite close. Since aluminum PCBs work well in terms of Thermal dissipation they do not have severe expansion or contraction issues. They work excellently and are durable and reliable.
Dimensional Stability
Aluminum PCBs show dimensional stability and stable size. For example, when they are heated from 30-140 degrees, their size only had a change by 2.5%-3.0%.
Others: Aluminum PCBs can be used in power device surface mount technology. They are effective for use in circuit design because of their performance in terms of thermal expansion of circuit design. They help to prolong products shelf life and product power density. They are also extremely reliable. They can help to shrink the overall volume of the product and is also a cheaper option. They show electromagnetic shielding and high dielectric strength.
Industry Category