How to Design PCB Creepage with Standards?
By:PCBBUY 02/22/2024 16:20
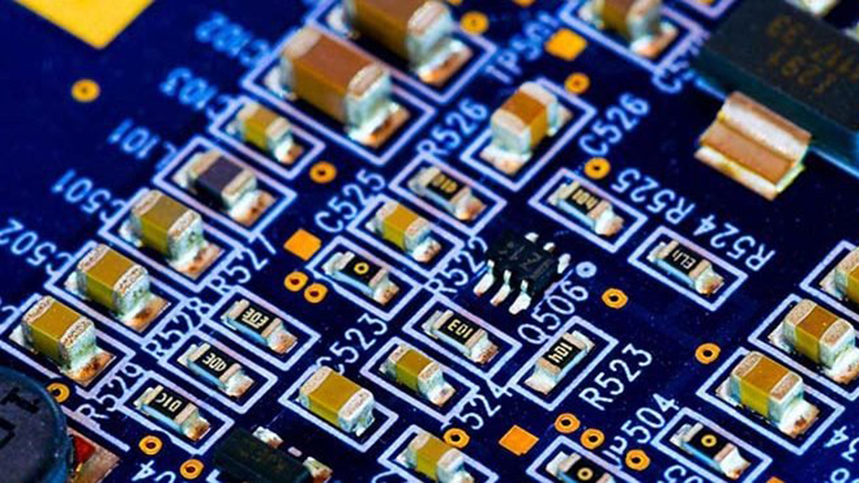
Printed circuit boards that conduct high voltages can be victimized by an electrostatic discharge between exposed metal if that metal is too close together. This discharge can potentially cause damage to the board and its components, and it is important for PCB designers to observe proper spacing between metal conductors on the board. Conductor spacing on a circuit board is measured in two ways—creepage and clearance:
In this passage, we are providing all the details information of creepage distance in PCB. If you are curious about creepage distance in PCB, please check and read the content below for more professional knowledge.
How to calculate PCB creepage distance?
The measurement of clearance depends on factors such as the applied voltage, air pollution, and temperature variations. Additionally, humidity decides the breakdown voltage of air and affects the likelihood of arcing. On the other hand, along with board material and environment conditions, moisture, and contamination due to particulate accumulation shorten the creepage distance.
Designers are unable to solve issues related to clearance at PCB layout design stage since the measured distance is along the air pathway (line of sight). Component placement will likely reduce errors occurring during spacing. However, key factors, such as the usage of insulating materials and the adoption of double-sided assembly, play a critical role while determining PCB component spacing requirements.
Insulating materials acts as a sheet barrier between the high-voltage nodes. They also sleeve or cover overexposed high-voltage leads. There is a high proportion of PCB components belonging to the surface-mounted category, allowing designers to place circuits as per the requirement of clearance on opposite sides of the board. It is also important to maintain clearance from the bounding surface and through-hole connection points present on the board. Nodes within the same high-voltage circuits at the same potential do not require increased clearance or creepage. However, low-voltage circuits have to meet clearance requirements in relation to high-voltage circuits.
Few international standards have suggested the use of conformal coating for limiting issues related to the clearance. The conformal coating is applied as per the design requirement. Minimum creepage distance can solve tracking failures. Avoiding the conductive path along the insulator surface limits tracking failures. Several factors affecting creepage and clearance include:
· Working voltage
· Pollution degree
· Insulation
· Type of circuit
What are the PCB creepage standards?
For those of us who don’t want to learn about the importance of creepage and clearance from direct experience, there are a few standards to help us. Primarily you should look into IEC 60601 and IPC 2221. These two standards detail spacing between conductors for different voltages and scenarios.
Sometimes there will be gray areas where the standards won’t tell you exactly how to solve a problem or layout your conductors. Although, your CM’s DFM rules will ensure manufacturability you should have your boards tested to ensure the safety requirements for creepage and clearance are met. The most well-known testing service is Underwriter’s Laboratory (UL), which will validate your boards, give your customers confidence, and provide you with protection against a related contingency. At the end of the day, it’s important for you to know the principles of design for creepage and clearance so you can ensure your board is compliant.
How to Design PCB Creepage with Standards?
Once you have the spacing requirements the board will need for proper creepage and clearance, the next step is to set these values up in your PCB layout system’s design rules. Rules and constraints can be set up for metal to metal clearances, whether it is between traces, pads, copper pours, or any combination of the three. You will also want to set up the correct spacing for your component footprints, especially those larger parts that are conducting a lot of voltage. In some cases, you can even set up unique keep-out clearances around specific footprints to account for heat sinks and other unusual configurations. All of these rules will help you to maintain the necessary spacing between high voltage components that you need.
When you are placing the components in the layout, make sure to consider all aspects of the parts as you place them. This will include any metal conductors, such as heat sinks, that may overhang the part, especially if you aren’t able to set up a unique keep-out zone around it. During layout, you will also want to ensure that any edits or changes to the component placement don’t end up violating spacing that you have already carefully set up between the parts. Even rotating a component 90 degrees can cause an unusually shaped part to violate a voltage clearance.
Here are a couple of other techniques to consider during layout for spacing:
To help maintain the right amount of clearance spacing, try locating high voltage components on one side of the board and low voltage parts on the other. In some cases, high voltage parts may not have as stringent spacing rules between them as they do to low voltage parts.
Creepage will require another solution, as putting parts on the other side of the board won’t give you the separation you need through the surface of the board. Instead, you may want to install insulating barriers or cut grooves or slots into the board. The change in the contour of the board will increase the distance over the surface that the voltage has to travel, giving you the creepage separation you need.
Industry Category