How to Design a Rigid Flex PCB Step by Step with 7 Effective tips?
By:PCBBUY 01/21/2022 09:13
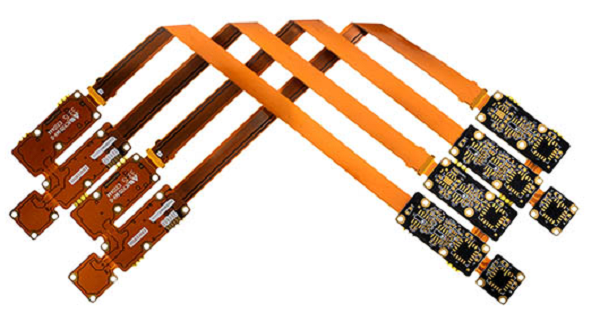
Broadly speaking, a rigid flex design will closely resemble a hardboard design, with the flexible layers fully extending into the rigid areas of the board. Similarly to hardboard layouts, a rigid flex fabrication package will include Gerber layers, along with drill files, solder mask layers, nomenclature, perimeter/rout files, etc. Avoid placing pads and vias on the bending area of the flex part of a PCB. Areas near the bending line will deliver mechanical stress that could jeopardize the structure of the plated holes.
How to Design a Rigid Flex PCB? In this passage, check and read the content below for more information about Rigid Flex PCB design.
What are the advantages of rigid flex PCB design?
By combining the properties of rigid and flexible PCBs, rigid-flex PCBs come with a host of benefits for both manufacturers and consumers.
· Mechanical stability- Their basic structure consists of interchanging layers of rigid and flexible PCBs. This ensures that they're both stable and flexible, facilitating easy installation in small spaces.
· Connection reliability- With rigid-flex PCBs, you get greater stability and polarity, making connections easier and more secure with other components. You will also require fewer connector components with each application.
· Dynamism- Along with repeatability and precision, you'll enjoy greater flexibility with packaging.
· Cost-effective- By using rigid-flex PCBs, you can cut down on the total expenditures.
· High-density applications- Arguably, the best benefit of rigid-flex PCBs is that they can be used for a high-density device population. This is due to their flexibility, stability, and low space use.
· High shock and vibration resistance- Electronic components are used in a wide range of items, some of which experience constant vibrations. With such devices, you won't have to worry about damage as rigid-flex PCB is highly resistant to shock and vibration.
What are the guidelines of rigid flex PCB design?
Broadly speaking, a rigid flex design will closely resemble a hardboard design, with the flexible layers fully extending into the rigid areas of the board. Similarly to hardboard layouts, a rigid flex fabrication package will include Gerber layers, along with drill files, solder mask layers, nomenclature, perimeter/rout files, coverlayer, etc.
However, there are some key differences between the fabrication packages for rigid flex PCB’s and hardboard applications:
· A rigid flex print generally has many more dimensions on it, and should carefully define the requirements, as these boards are generally used in 3D applications. It should also accurately define the rigid to flex transition areas, as these are not always apparent when viewing the Gerber layers alone.
· The material layup in rigid flex boards is critical, and should be worked out in collaboration with your fabricator. Your fabricator can help you make the right choices in materials based your requirements such as UL flammability rating, minimum bend radii required, mechanical considerations, impedance control on both flex and rigid layers, RoHS certification, lead free assembly compatibility, and other considerations.
· Rigid flex boards usually require additional layers in the Gerber files. Layers 1 and X will have solder mask layers, but you will also need artwork layers that define the coverlayer and bondply sections (if required) of the board, and how much each go into the hardboards. IPC 2223 recommends 0.100″ but your fabricator may be able to accommodate less than that.
The IPC-2223 Sectional Design Standard for Flexible Printed Boards is an excellent resource for wise practices in both flexible circuit and rigid flex circuit design. An electronic download of the IPC 2223 can be purchased here.
How to choose rigid flex PCB material?
Polyimide is the primary material used for both flex core layers and coverlay layers. Flex materials offer better material properties when compared to rigid PCBs. The thickness of flex materials is uniform with an improved Dk value ranging between 3.2 and 3.4. The lack of woven glass reinforcement eliminates variations in Dk. Polyimide is also extremely uniform in its thickness due to its “cast” manufacturing process. The typical layer thickness ranges from 0.5 to 4mils.
Polyimide flex cores are cladded with either electro-deposited or rolled annealed copper. This copper is very thin and is suitable for both dynamic and static applications. 0.5oz (0.7mils) copper is commonly used in flex PCBs. The most common flex PCB copper weights are 0.5oz and 1oz. The maximum copper weight is 2oz. This gives the best combination of the thinnest possible construction.
There are two major types of flex materials:
· Adhesive-based where the copper is bonded to the polyimide with acrylic adhesive.
· Adhesive-less where the copper is cast directly onto the polyimide.
Industry Category