How to Differentiate PCB Assembly Quality Practices?
By:PCBBUY 09/13/2023 16:48
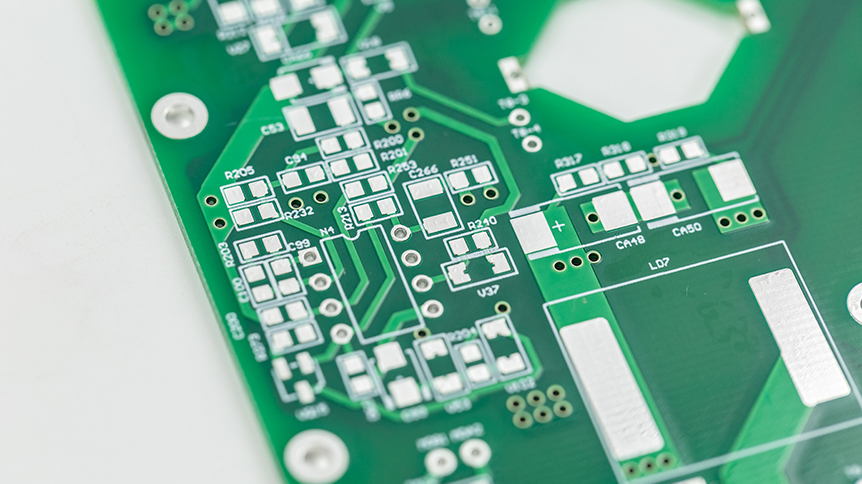
Whether in the backcountry or building PCBs, the choice of partner matters. While searching for a PCB contract manufacturer to partner with for building your circuit boards, establishing a high level of communication and trust is tantamount to a successful final product. Whether a novice or experienced in design, some subtle layout choices can develop into major manufacturing problems further down the road if left unaddressed.
Common Problems with PCB Contract Manufacturers
Given the high degree of technical expertise and equipment utilized in PCB production, it is a deeply involved service between client and manufacturer. There must be a rock-solid foundation between designers and CM, especially when a design is gradually building from proof of concept to NPI (and many prototypes).
Certainly, size alone can’t be the only determining factor when deciding upon a CM. Still, a larger workforce and facility also tend to contain better equipment, more proficiency, and higher-value experience. However, the largest PCB assembly factories may only be economically viable with large production quantities. That scenario amounts to putting the cart before the horse regarding an NPI.
Location is another important consideration. For example, is it possible to physically tour the facility before placing an order to assuage whether the shop is organized, professional, and knowledgeable enough to handle any challenges they may encounter during board design? While virtual tours have certainly bridged the gap during the height of the COVID-19 pandemic years, most prefer the accessibility and personability of a face-to-face meeting.
Unfortunately, not every CM builds equally. Look to spot any of these issues early that could suggest an ill-suited partnership for manufacturing:
Inconsistent manufacturing practices
Is there a high variance in the performance or yield of the board? Boards must retain tight tolerances to match their intended use and function. Manufacturing quality should not stray, and changes made to production should be carefully considered.
Undocumented changes
Speaking of changes, these should be well-communicated by the manufacturer without delay, alongside a justification for why the manufacturing process must be adapted. Poor documentation means having to discern informal changes for future revisions, which becomes especially troublesome if production is taken to another manufacturer.
End-customer returns
Technically, issues could arise due to poor design choices, but the manufacturer must submit boards to extensive testing to detect failure vectors. Before the boards are fit to leave the shop, designers must have confidence that they have been exhaustively probed and analyzed to minimize end-user frustration.
Poor documentation practices
As previously alluded, poor documentation can make working with multiple manufacturers a headache. However, it is still far from ideal, even when working with a single shop. Documentation acts as a checkpoint in design, allowing future revisions and layout teams to quickly and accurately resume where others have left off without skipping a beat. Fully-updated design documentation is crucial to maintaining the link between past and future board iterations.
Excessive respins. Sometimes design changes are completely out of the hands of the manufacturer. For example, designers may request or eliminate features and functionality, or suppliers may be experiencing component or material shortages. Even then, some manufacturing changes are unforeseeable and will dictate a redesign. Still, when it comes time for a manufacturer to review a design, designers should expect a comprehensive report incorporating as many DFM principles and changes as possible. Beware of the “Whack-A-Mole” manufacturing method, where poor practices are being resolved post-production rather than circumvented before fabrication and assembly.
Incompatible CAD tools/databases
Outdated or legacy software may lack standard design features and compatibility with common industry suites. Translating documents and files can take time and introduce errors at the initial design stages.
Problems like these can be avoided by choosing to partner with a CM that provides the level of quality necessary for a successful build. Not only do manufacturing and testing capabilities need to be top-notch, but they should also aim to reduce the number of re-spins for a product in the development stage. Minimizing the number of redesigns will save money and time, allowing designers to bring products to market sooner than a less experienced or rigorous assembly shop.
Industry Category