How to Estimate PCB Cost with 5 Common Factors?
By:PCBBUY 10/12/2021 09:26
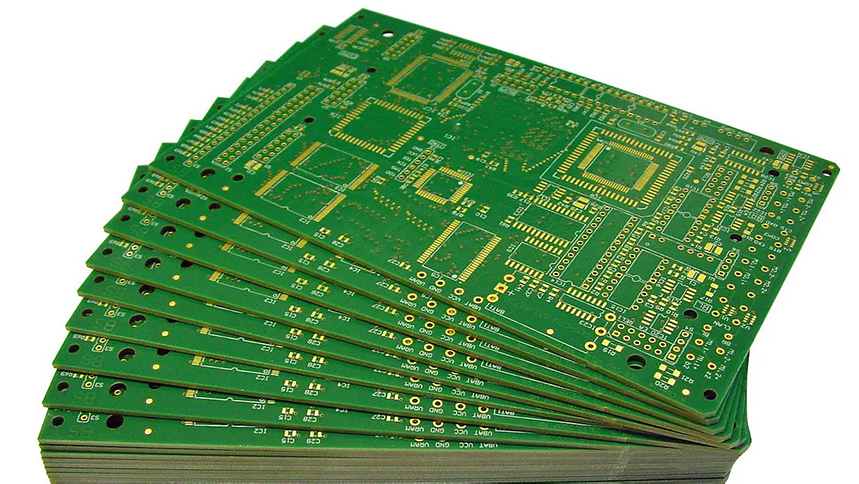
PCB manufacturing may be complicated and costly, but sourcing responsibly and partnering with solid suppliers can make a world of difference. By following the tips in this post, you can spend less and make more, all while growing your business the way you envision it.
In this passage we will tell you everything about estimating PCB cost. You can learn the professional information from the 5 common factors for estimating PCB cost. Please check and read the content below for more knowledge.
1. Getting to know the PCB material
PCBs are made out of different materials like fiberglass, polymer inks, and solder. The conductive layers are usually made of copper, gold, or silver. These materials can affect the way the board reacts to heat. PCBs need to have thermal reliability and temperature reliability. They also need to have other mechanical properties that affect the performance of the board and the device it powers. When PCBs need to have higher frequencies, the boards need to be made of higher-grade materials – like gold or silver – than the standard copper boards.
PCBs require raw materials like:
· Copper
· Gold
· Lead
· Nickel
· Silver
· Fiberglass
· Epoxy Resin
2. Getting to know the board size
A panel is one of the most important raw which is needed to produce a PCB. Size of the board is another huge price determining factors, as the bigger the board is, the more material will be required to build it. This point might sound straight forward but it’s not exactly as simple as that because, depending on the specified dimensions it is very much possible to have a board that takes up less area estate but is actually higher in cost.
This happens because the overall size of the panel used to manufacture the board; sometimes one dimension fits the panel a lot better than the other does. Let’s consider two parts with the same total square inches per board. Board A is 2sq.in x 6sq.in and board B is 3sq.in x 4sq.in. A panel of standard production will produce more of the 3sq.in x 4sq.in variety of boards then the 2sq.in x 6sq.in variety of board. Thus, the cost for each board would be reduced for the 3sq.in x 4sq.in boards.
3. Pay attention to surface finish
A minor factor to consider regarding PCB production involves the costs associated with a given finish. Some finishes boast higher grades and offer longer shelf life, thus adding to the overall cost of production. One of the more common and low-cost surface treatments is HASL, which offers good solderability but is rated unfavorably on other counts. ENIG, by comparison, scores favorably in most categories yet only commands a slight price difference.
Each of the surface treatment options offers unique features:
· HASL: Solderability
· LFHASL: Solderability
· OSP: Solderability
· IMM Ag: Solderability, Al wire bondable
· IMM Sn: Solderability
· ENIG: Solderability, Al wire bondable, contact surface
· ENEPIG: Solderability, Al wire bondable, contact surface
· Elec Au: Solderability, Al/Au wire bondable, contact surface
4. Pay attention to thickness of the PCB and aspect Ratio
Until recently, the thickness of a PCB had played only a minor role in the overall cost, though all that is liable to change in the coming years. Thicker material can be costlier to procure, laminate and form into a printed circuit board, especially if the design itself is highly intricate.
Thinner material will generally put a line of PCBs into a slightly lower cost bracket because less material is required for the production at hand. The costs of a board in regards to thickness can also be impacted by the type of material used in a given production.
The standard thickness for a PCB is 1.6mm (0.063″). In recent times, thicker boards have become more expensive, though an industry-wide going rate has never been established. Overall, it depends on the manufacturer whether a thinner board of 0.8 mm will cost less or equal to a board of standard thickness.
5. Pay attention to layer count and drill size
The number of layers is also a significant cost-determining factor. Single-sided or double-sided PCBs are roughly the same cost to manufacture. However multi-layer PCBs create additional costs in the materials and manufacturing process. Typically, moving to a 4 layer PCB from a 2 layer PCB will double the price. Adding additional layers to a multi-layer project will add additional cost but the price increase related to adding more layers is not as pronounced. For example, the cost to go from 4 layers to 6 layers may represent a 50% increase opposed to the 100% increase incurred when moving from a 2 layer to a 4 layer PCB.
Another factor to consider is the smallest hole size to be drilled and the total number of drilled holes. When the hole size is less than 0.015″ the cost of the PCB can increase between 5% and 10%. A large number of holes can increase the cost further by a similar percentage. This is due to the fact that the manufacturing process has to be adjusted for smaller hole sizes and large hole counts and the number of panels that can be drilled at one time decreases.
Industry Category