How to Get Good Tips of Power Supply PCB Design Guidelines?
By:PCBBUY 11/27/2021 09:33
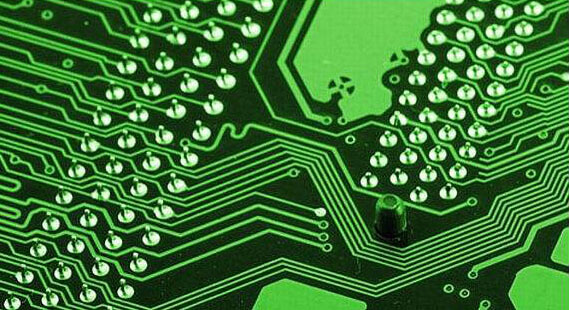
Different from a standard PCB, a power PCB also has to be designed so that everything is compact without sacrificing efficiency. It is especially true if the device that the circuit board supports is something like a smart phone, a tablet, or anything that can access data. While standard PCBs still have their place in electronics, the demand for more advanced electronics is greater than ever. Power PCBs are much more effective for these advanced electronics because it is only possible for a PCB to be compact yet powerful if it follows a power PCB design.
If you are going to learn more about power supply PCB design, please check and read the content in this passage for more professional knowledge.
What are the layout considerations for power supply PCB design?
You’ll have an easier time working with power PCBs if you know the differences in layout.
Although the organization is important in the layout of any given PCB, it is even more important in the layout of a power PCB. Remember that power PCBs deal need to handle a lot of energy for a very compact design that needs to handle larger currents.
Because of this, you will need to find a way to make sure that the reference points do not crowd the board, that the ground planes are not partial, and that you have proper cooling space even more than usual. The shortcuts you may have taken when laying out other PCBs cannot be taken when determining a layout for a power PCB. It would help if you considered everything.
You do not have the luxury of having a lot of room to work with when choosing a power PCB layout. You may need to give up a few things that are a quick fix when choosing a standard PCB layout. It is one challenge that you will likely face.
What are the options of power supply PCB design?
The first step in power supply is to choose the type of power supply you wish to use for your device. Unregulated power supplies are a down-and-dirty option for converting AC power from a wall outlet to a DC voltage. The output from these supplies will contain a ripple waveform as the output is not smoothed with a regulator. Modern applications use a regulated power supply, where this ripple is minimized.
There are two principal options for regulating DC output from power supplies: using a linear regulator or a switching regulator, which is sometimes called a switch-mode power supply. These types of power supplies pass the DC output from a full wave rectifier to a regulation circuit, which smooths the ripple waveform that is superimposed on the desired DC output. These regulators can also be used to directly regulate a DC power source like a battery. Linear regulators have very low noise, but they tend to be bulky due to the use of heatsinks or other active cooling measures required for thermal management. The significant heat dissipation in these power supplies is responsible for their low efficiency.
In contrast, a switched mode power supply provides much higher efficiency over a broad current range, allowing these power supplies to take on smaller form factor. However, these power supplies use a PWM circuit to smooth and regulate the output voltage, which requires the use of an active switching component (normally a MOSFET). This means that the system radiates strong EMI, and the output will contain spikes due to switching noise. This switching noise can appear as a ringing signal on the output (i.e., conducted EMI), and this noise needs to be filtered from the output.
How to process the power supply PCB design?
At the first stage, input AC voltage at 230VAC/110VAC is converted to an isolated DC voltage in the range of 6-12V. A buck-switching regulator is employed at the second stage which converts the 6-12V to 5V or 3.3V. Further, the 3.3V is converted to 1.8V or 1.2V using LDOs (Low Dropout regulators).
Before the advent of Switched-Mode Power Supplies (SMPS – switching power supplies) iron core transformers were used to convert high voltages 230VAC/110VAC to 12VAC. This was further rectified by diode bridge rectifiers to DC volts approximately 12 x 1.4 = 16.8 VDC maximum. Linear regulators were used in reducing the voltages to the required levels. The disadvantage of such circuits was poor power efficiency (less than 80%), high heat loss, larger PCB footprint, and poor power ripple. The use of switching power supplies has improved efficiencies of conversion of voltages to lower levels, reduced PCB footprint of power supplies (very small and light in size), and reduction in ripple.
In linear regulators, a larger amount of power was previously lost due to higher drop out voltages. For example, consider the linear voltage regulator LM7805. LM7805 (5V) typically has a drop out voltage of approximately 7.5V, requiring a minimum of approximately 2.5V difference between input and output voltage. Therefore for a 1A regulator, the power loss in the regulator at 7.5V input will be 2.5V x 1A = 2.5W.
With the low dropout regulator LM1117-5.0, the drop out voltage is 6.2V requiring an input voltage of Vout +1.2V at the input. For critical applications, a combination of switching regulators and LDO is used to increase efficiency. For example, from stage one if 7.5 volts is available this will be dropped to 3.3V with a buck converter and then dropped to 1.8V using a linear regulator LM1117-1.8.
Industry Category