How to Improve Manufacturing with PCB Troubleshooting?
By:PCBBUY 10/29/2024 16:51
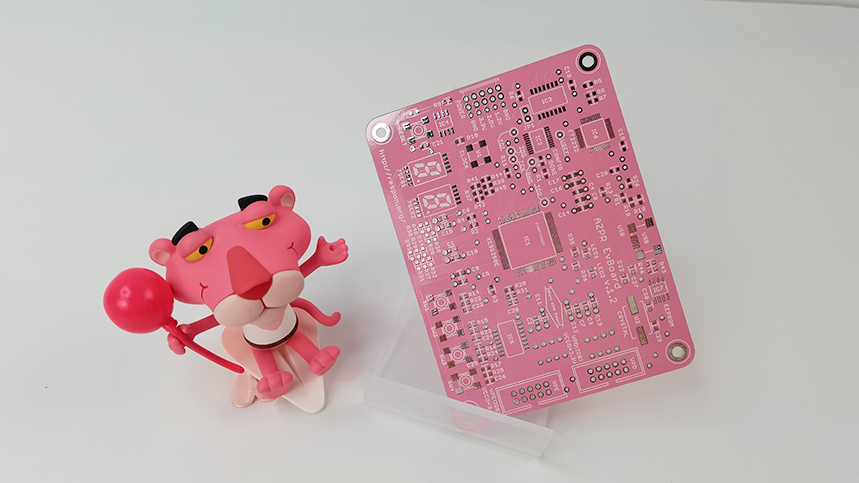
Printed Circuit Boards (PCBs) are the backbone of modern electronic devices, and their manufacturing processes are critical to ensuring product quality and reliability. PCB troubleshooting is an essential aspect of manufacturing that can significantly enhance production efficiency, reduce costs, and improve product quality. This article explores the various methods and techniques involved in PCB troubleshooting, emphasizing their importance in the manufacturing process.
How to Understand PCB Manufacturing?
1. The PCB Manufacturing Process
PCB manufacturing involves several key stages, including design, etching, plating, and assembly. Each stage presents unique challenges that can lead to defects if not properly managed.
Design Phase
The design phase involves creating the layout of the PCB using CAD software. Common issues at this stage include:
Design Rule Violations: These occur when the layout does not comply with manufacturing specifications.
Component Placement Errors: Incorrect positioning can lead to assembly problems.
Fabrication Phase
The fabrication phase includes processes like drilling, etching, and plating. Potential defects here include:
Insufficient Etching: This can result in short circuits.
Drill Hole Issues: Misaligned or improperly sized holes can affect component placement.
Assembly Phase
The assembly phase involves soldering components onto the PCB. Troubleshooting in this phase focuses on:
Solder Joint Quality: Poor solder joints can lead to failures.
Component Orientation: Incorrectly oriented components can cause operational issues.
2. Importance of Troubleshooting in PCB Manufacturing
Effective troubleshooting in PCB manufacturing is crucial for several reasons:
Cost Reduction: Identifying and resolving defects early can save costs associated with rework and scrap.
Quality Assurance: Continuous troubleshooting helps maintain high product quality, leading to better customer satisfaction.
Efficiency Improvement: Streamlined processes reduce manufacturing time and increase throughput.
What Are the Common PCB Defects and Their Troubleshooting?
1. Open Circuits
Causes
- Broken traces
- Poor solder connections
Solutions
- Visual Inspection: Use optical magnification to identify breaks.
- Continuity Testing: Employ multimeters to test circuit paths.
2. Short Circuits
Causes
- Unintentional connections between conductive paths
- Solder bridging
Solutions
- **X-ray Inspection**: Utilize X-ray machines to identify hidden solder bridges.
- **Rework**: Carefully remove excess solder and correct connections.
3. Insufficient Solder
Causes
- Incorrect solder paste application
- Poor heating during reflow
Solutions
Solder Paste Inspection: Use automated optical inspection systems to ensure proper paste application.
Reflow Profiling: Analyze and adjust reflow oven profiles for optimal heating.
4. Warpage
Causes
- Uneven thermal distribution during soldering
- Material expansion
Solutions
Material Selection: Choose materials with lower warpage tendencies.
Thermal Management: Implement better thermal profiling during assembly.
What Are Techniques for Effective PCB Troubleshooting?
1. Implementing Statistical Process Control (SPC)
SPC uses statistical methods to monitor and control manufacturing processes. Key benefits include:
Real-Time Monitoring: Continuous data collection helps identify deviations from the norm.
Predictive Analysis: Historical data allows for forecasting potential issues before they arise.
2. Utilizing Failure Mode and Effects Analysis (FMEA)
FMEA is a structured approach to identifying potential failure modes within a system. Its implementation involves:
Risk Prioritization: Assessing the severity, occurrence, and detection of each potential failure.
Mitigation Strategies: Developing strategies to reduce the likelihood of failures.
3. Continuous Training and Development
Investing in workforce training is vital for maintaining high manufacturing standards. Effective training programs should focus on:
Troubleshooting Skills: Hands-on workshops to enhance problem-solving capabilities.
Technology Updates: Keeping staff informed about the latest PCB technologies and troubleshooting techniques.
Conclusion
Troubleshooting in PCB manufacturing is an indispensable practice that significantly contributes to improved product quality, reduced costs, and enhanced production efficiency. By understanding common defects, implementing effective troubleshooting techniques, and continuously training personnel, manufacturers can create a more reliable and efficient production environment.
References
1. IPC. (2018). IPC-A-600: Acceptability of Printed Boards.
2. Schubert, E. (2017). Introduction to Printed Circuit Board Design. Wiley.
3. The Institute of Electrical and Electronics Engineers (IEEE). (2019). Troubleshooting Techniques in PCB Design. IEEE Press.
4. O'Rourke, P. (2020). Lean Manufacturing in PCB Assembly. Cambridge University Press.
Industry Category