How to Improve Process in Manufacturing with PCB IPC Standard?
By:PCBBUY 10/11/2021 09:23
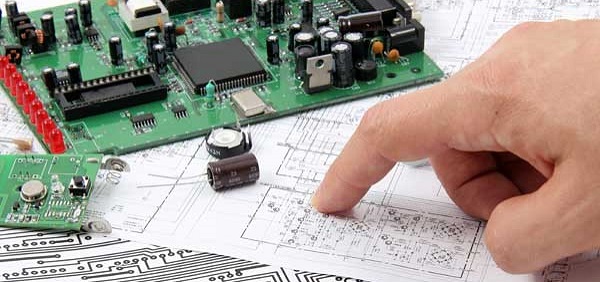
IPC is the trade association for the electronic interconnection industry. It provides industry standards for the assembly and protection of electronic equipment, as well as training, market research and public policy advocacy.
IPC is a member-driven organization and has more than 3,000 member companies around the world. Its members include companies in all aspects of the global electronics industry, including designers, suppliers, board manufacturers, assembly companies and original equipment manufacturers.
In this passage, we are going to provide you everything about PCB IPC standards and how to improve the manufacturing process. Check and read this passage for more information in the content below.
What is the importance of IPC standard in PCB manufacturing?
It’s tedious to read through pages of IPC standards, however, they are there for good reasons, particularly for PCB layout designs. The IPC was established in 1957 and at the time was known as the Institute of Printed Circuit. Today, thousands of companies that are part of the PCB design supply chain are members.
IPC produces and maintains standards that serve as a common guideline for PCB design, fabrication, assembly, test, and other areas of concern. For PCB designers, complying with the relevant IPC standards for PCB layouts can make a difference in a product’s success or failure.
What are the PCB IPC standards?
PC is the official name of the association which produces PCB-related standards. The association was formerly called the Institute for Printed Circuits (hence the acronym "IPC"), but is presently called the Association Connecting Electronics Industries—even though it retains the IPC moniker.
IPC, itself, is an international industry association consisting of more than 4,000 member companies that make, use, specify, and design PCBs and assemblies, including:
· Advanced microelectronics
· Aerospace and military
· Automotive
· Computer
· Industrial equipment
· Medical equipment and devices
· Telecommunications industry
What are the definition and content of IPC PCB?
Since IPC creates standards for the electrical and electronics industry, it also plays a crucial role in producing standards for PCBs. You can find IPC standards for PCB manufacturing at every stage of the PCB production process, including design and manufacturing.
IPC PCB standards also set requirements for soldering electrical and electronic work in PCBs. These soldering standards often relate to reflow and wave soldering, as well as solder splices. Companies also rely on them to see if their electrical and electronic assemblies are acceptable during manufacturing. IPC standards also cover cable and wire harness assemblies. Finally, they set acceptability standards for the manufacture, inspection and testing of electronic enclosures before the PCB is released as a final product.
What are the related IPC standards of PCB manufacturing?
There are many sections of the IPC standards, and not all sections are applicable to every circuit board design. In addition, each standard is a very long document that includes a range of requirements for designers, manufacturers, or both. Some of the important IPC design standards include:
· IPC 2221: Establishes some generic design and performance requirements in PCBs and other forms of component mounting or interconnecting structures.
· IPC 4101: Defines material requirements for PCB laminate materials and other materials used to build stackups.
· IPC 2152: A newer standard that defines current carrying requirements in copper traces and planes in a number of different applications.
· IPC 4761: Covers design guidelines for via protection to ensure reliability, manufacturability, and quality.
· IPC 6012: Defines generic performance requirements as compiled from IPC 2221, IPC 4101, and other quality requirements. The related IPC 6013 standard applies the same ideas to flex circuit boards.
· IPC-A-600 series: Defines acceptance metrics for printed circuit boards, as well as the three standard IPC Classes for various printed circuit board assemblies.
· IPC 7351: Specifies footprint and land pattern requirements for SMT components. Component manufacturers use these specifications when designing their land patterns to ensure solderability and reliable electrical connections.
· IPC-1752A: Material Declaration Management standard defines reporting formats for data exchanged between designers, distributors, and manufacturers.
Industry Category