How to Improve the PCB with 6 PCB Assembly Design Rules?
By:PCBBUY 11/29/2021 10:25
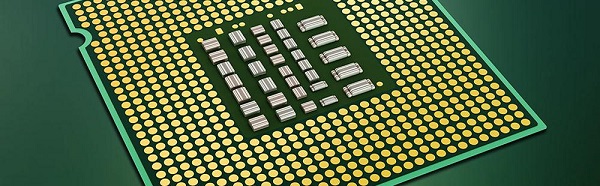
The problem that often emerges—at least, among those who are not yet PCB —is that the initial PCB designs does not fully take assembly into account. Instead, they focus exclusively on the board itself without broader context of how the board will be used within the product or application.
Overlooking PCB assembly can lead to significant complications. A PCB design may seem perfectly acceptable when viewed in isolation, but certain design decisions may make assembly difficult later on. For example, components may be situated too close to one another, which could lead to a non-functioning product, or cause performance issues. We’ll discuss this in-depth later in the article.
Check and read the content below for more information about PCB assembly design rules.
Why to follow the PCB assembly design rules?
Not only do we need our PCBs to work the way that we’ve designed them too, but those boards must be manufacturable for a reasonable price as well. There are several factors that can contribute to a board not being considered manufacturable. Here are the main categories of problems:
· Components: Parts that are unique or not readily available will have higher costs attached to them. Also if the lead times on some parts cause delays in the board build, that will add to the expense as well.
· Placement: How you place your parts can affect how the board is manufactured and drive up costs. Even simple things such as how a component is rotated can affect its solderability.
· Layout: Your PCB design will usually connect to other boards or interfaces. If these considerations haven’t been accounted for up front, it could add to the expense of manufacturing the entire system.
What are the 6 PCB assembly design rules?
1. Keep your BOM up to date while designing.
A BOM is a key aspect of both design and assembly. If there are any issues in your BOM, the assembly house will place the project on-hold until the issues have been resolved with an engineer. One way to make sure your BOM is updated is to review your BOM any time there is a change in your design. When you add new components to your schematic while the layout is in process, make sure you’ve also updated the BOM with the correct part number, description, and component values. During the design process, the engineer might change a component due to long lead-times, size, or availability and forget to update the BOM with the new part number. This can lead to various assembly issues and cause delays.
2. One pad for one connection.
Every connection to every component must have its own independent pad. Each pad must be commensurate in size with its mates. If two components share a pad—let’s say, a resistor and a capacitor—neither can be properly aligned during assembly. And if one pad is substantially larger than its mate for a component, component tombstoning can result from an imbalance of solder deposition. If a pour or plane will be a point of contact, there must be a mask-defined pad of appropriate size. If a device involves non-solder mask defined pads for connections as well as solder mask—defined pads a BGA matrix on a loose pitch in which some adjacent outer balls are common to a ground pour, for example—stipulate in a design note that the board fabricator shall not edit the solder mask apertures for those solder mask-defined pads.
3. Use standard and common components
Should ensure that the components you plan to use are readily available. Also, you should validate their continued production to avoid having components whose end of life (EOL) is approaching as it will minimize delays in the future. Standard and readily available components result in reduced costs, higher quality, and lower inventories. Unique parts lead to increased costs and high chances of poor quality.
4. Component Orientation and Handling
The board must be designed in a way that components consistently orient themselves when assembled. The orientation of components can cause issues. For instance, issues arise when polarized capacitors and diodes face different directions. The placing of the components determines whether the board can be assembled or not, the soldering techniques which will be used, and the types of thermal reliefs that are required. Also, it affects the quality of signals as some components generate electrical noise when placed too close to others. For instance, Drill holes should not be placed at the edge of the boards as they can cause cracks on the board.
5. Pay attention to part-to-part spacing.
One of the frequently asked questions posed by designers who are not yet PCB is in regard to the component-to-component spacing. Placing a component too close to another component can create various issues which may require redesign and refabrication, which results in a loss of time and money. PCB masters use several techniques to avoid part-to-part spacing issues during assembly. They design their footprint in such a way that there is always enough gap between component boundaries. This alleviates any potential issues that could arise from components being too close during placement.
6. Choose components during the design phase.
PCB choose components early in the design process, realizing that this is the best way to ensure there are no conflicts between the actual design and the components being assembled. If you factor in component sizes from the very beginning, component space and sizes are no longer a concern and the PCB assembly process can proceed without barriers. This also leads to the next tip.
The PCB designer should talk to the circuit designer and engineers to see if the component size can be reduced, creating additional space on the board. After all, a smaller part will mean a smaller footprint on the board.
Industry Category