How to Make A Comprehensive Guide of Understanding PCB Substrates?
By:PCBBUY 07/22/2024 16:23
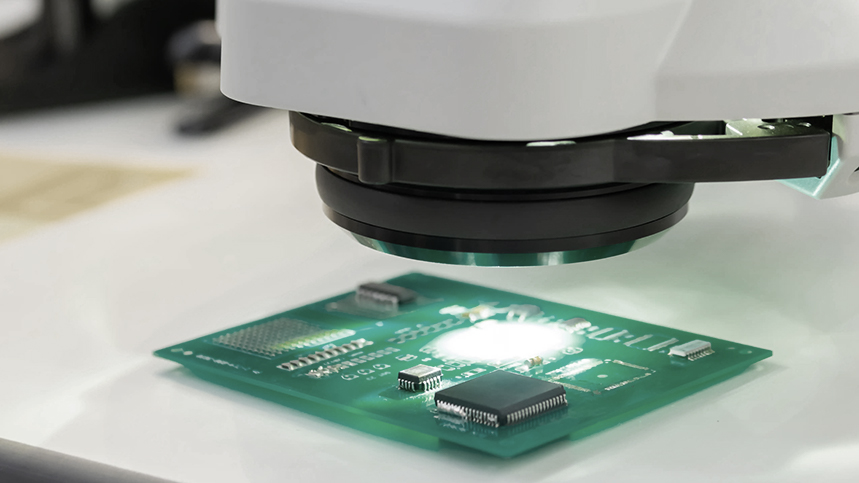
Printed Circuit Boards (PCBs) are the backbone of electronic devices, providing mechanical support and electrical connections to the various components. One of the most crucial aspects of PCB design and manufacturing is the choice of substrate material. This article delves into the various types of PCB product substrates, their properties, applications, and the latest trends in the industry. With detailed data, professional insights, and comprehensive tables, we aim to provide a thorough understanding of PCB substrates.
Introduction to PCB Substrates
What is a PCB Substrate?
A PCB substrate is the base material upon which the circuit is built. It provides the foundation for the conductive pathways and helps to maintain the structural integrity of the PCB. The substrate must possess excellent electrical, thermal, and mechanical properties to ensure reliable performance.
Substrate-like PCBs earn their name due to the resemblance they bear to the IC carrier board employed in semiconductor packaging. The IC carrier board is a high-tech circuit board carrying one or more chips and other circuitry that connects the semiconductor die to the package land pattern. Despite the fact that substrate-like PCBs are approaching the feature sizes witnessed in IC carriers, they are still regarded as PCBs since they possess both active and passive components.
Typical Feature Sizes
These components are regarded as the next generation of high-density rigid PCBs. Concerning linewidth and trace spacing, these components lie somewhere between standard HDI processing and the micron-scale features found in IC substrates. Substrate-like PCBs typically utilize thin wires for routing signals and internal planes for power and ground, much like in a traditional PCB. The primary distinction lies in the smaller length scales, as delineated in the table below.
HDI PCB | Substrate-like PCB | IC substrate | |
Layer count | 16+ | ~10 | ~10 |
Thickness | 1-2 mm | ~1.5 mm | ~1.5 mm or less |
Typical minimum linewidth/space | 40/40 μm | 30/30 μm | 10/10 μm |
Process* | UV LDI | MSAP, UV LDI | SAP, MSAP |
What Is the Importance of Choosing the Right Substrate?
The choice of substrate material can significantly impact the performance, reliability, and cost of a PCB. Factors such as dielectric constant, thermal conductivity, mechanical strength, and cost must be considered when selecting a substrate for a particular application.
What Are the Types of PCB Substrates?
FR-4 (Flame Retardant 4)
FR-4 is the most commonly used PCB substrate material. It is a composite material made of woven fiberglass cloth with an epoxy resin binder that is flame resistant (self-extinguishing).
Properties of FR-4
Dielectric Constant (Dk): 4.4 - 4.7
Thermal Conductivity: 0.3 W/m·K
Glass Transition Temperature (Tg): 130°C - 170°C
Moisture Absorption: 0.10% - 0.20%
FR-4 is favored for its balance of performance and cost, making it suitable for a wide range of applications from consumer electronics to industrial equipment.
High-Frequency Laminates
High-frequency laminates are used in applications that require minimal signal loss and high-speed signal transmission. These materials typically have a low dielectric constant and low loss tangent.
Common High-Frequency Laminates
Rogers RO4000 Series
Dk: 3.38 - 3.55
Loss Tangent: 0.0027 - 0.0037
Thermal Conductivity: 0.71 W/m·K
Taconic TLY Series
Dk: 2.2 - 2.5
Loss Tangent: 0.0009 - 0.0014
Thermal Conductivity: 0.20 W/m·K
High-frequency laminates are essential in RF and microwave applications such as antennas, radar systems, and communication devices.
Metal Core PCB (MCPCB)
MCPCBs incorporate a metal core, typically aluminum or copper, to enhance thermal conductivity. They are commonly used in applications where heat dissipation is critical, such as LED lighting and power electronics.
Properties of MCPCB
Thermal Conductivity: 1.0 - 3.0 W/m·K (aluminum), 3.0 - 5.0 W/m·K (copper)
Thermal Expansion: 24 ppm/°C (aluminum), 17 ppm/°C (copper)
MCPCBs provide superior heat dissipation, improving the reliability and lifespan of heat-sensitive components.
Flexible and Rigid-Flex Substrates
Flexible and rigid-flex substrates are used in applications that require flexibility, such as wearable electronics, aerospace, and medical devices. They can bend and flex, making them ideal for compact and dynamic applications.
Properties of Flexible Substrates
Material: Polyimide, PET
Dielectric Constant: 3.4 (polyimide), 3.2 (PET)
Tensile Strength: 200 MPa (polyimide), 250 MPa (PET)
Bend Radius: Minimum of 10 times the thickness
Flexible and rigid-flex substrates allow for innovative designs and enhanced durability in dynamic environments.
What Are the Factors Influencing Substrate Selection?
Electrical Properties
Dielectric Constant (Dk): Affects signal speed and impedance control.
Loss Tangent: Determines signal loss over distance.
Thermal Properties
Thermal Conductivity: Impacts heat dissipation.
Glass Transition Temperature (Tg): Indicates the temperature at which the material transitions from a rigid state to a more plastic state.
Mechanical Properties
Tensile Strength: Indicates the material's resistance to breaking under tension.
Flexural Strength: Measures the material's ability to resist deformation under load.
Cost Considerations
Cost is a critical factor in substrate selection, particularly for consumer electronics where large volumes are produced. Balancing performance with cost is essential to achieving an economical design without compromising quality.
What Are the Industry Applications?
Consumer Electronics
Consumer electronics require substrates that offer a balance of performance and cost. FR-4 is commonly used in smart phones, tablets, and laptops due to its affordability and adequate performance.
Automotive Electronics
Automotive electronics demand high reliability and thermal management. MCPCBs are widely used for their superior heat dissipation properties, making them suitable for LED lighting and power modules in vehicles.
Aerospace and Defense
Aerospace and defense applications often require high-frequency laminates for radar and communication systems. The materials used must withstand extreme temperatures and environmental conditions.
Medical Devices
Medical devices, particularly implantable and wearable devices, require flexible substrates that can conform to the human body. Polyimide and PET substrates are commonly used for their flexibility and biocompatibility.
What Are the Latest Trends in PCB Substrates?
Environmental Regulations
Increasing environmental regulations are pushing the industry towards greener materials. Halogen-free and lead-free substrates are gaining popularity to meet environmental standards.
Advanced Materials
New materials are being developed to meet the demands of high-speed and high-frequency applications. These advanced substrates offer lower dielectric constants and improved thermal properties.
Miniaturization
As devices become smaller and more compact, the need for high-density interconnect (HDI) substrates increases. These substrates allow for finer lines and spaces, enabling the miniaturization of electronic devices.
What Are the Integration of Embedded Components?
The integration of embedded passive and active components within the substrate is an emerging trend. This technology reduces the footprint of PCBs and enhances performance by reducing parasitic effects.
Conclusion
The choice of PCB substrate material is a critical decision that impacts the performance, reliability, and cost of electronic devices. Understanding the properties and applications of different substrates helps designers make informed choices that meet the specific requirements of their projects. As technology evolves, the PCB substrate industry continues to innovate, offering new materials and solutions to meet the growing demands of advanced electronic applications.
By staying informed about the latest trends and developments in PCB substrates, engineers and designers can ensure they are using the most suitable materials for their designs, ultimately leading to better-performing and more reliable electronic devices.
Reference
He Wei, PCB Basic Electrical Information Science and Technology, China Machine Press,20-26
Industry Category