How to Make Silkscreen from PCB with 4 Effective Tips?
By:PCBBUY 10/11/2021 09:31
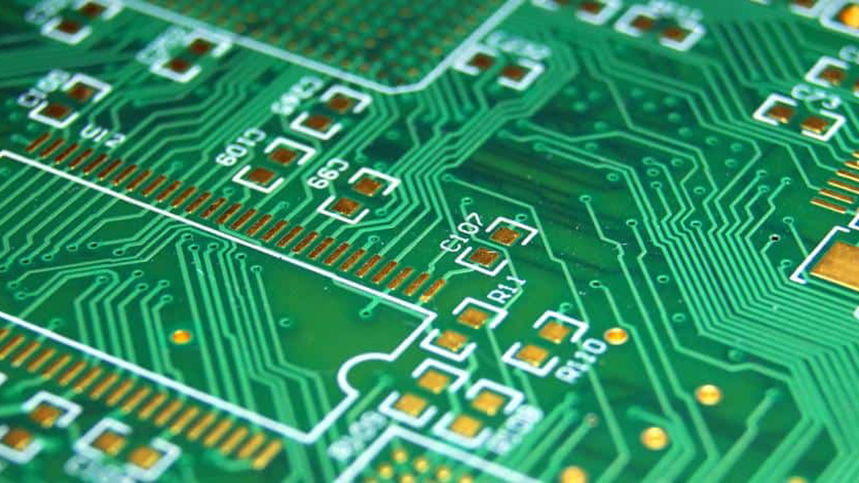
The Silkscreen is the topmost layer of a Printed Circuit Board (PCB) which is used as a reference indicator for placing components on a PCB Board. It requires a specifically formulated ink whose standard color is white, but it can also be Red, Black, Yellow, Blue and a number of other colors. The silkscreen is used to specify useful information on the PCB board that can help/assist users during assembly.
In this passage we will tell you everything about 4 methods to make silkscreen of PCB. If you are interested in how to make the silkscreen from PCB, please check and read the content to learn more.
1. What information does PCB silkscreen provide?
A silkscreen may not have any role in the functioning of a PCB; however, it is valued for the information that it delivers. For instance, it will help anyone to:
· Understand the warning symbols
· Polarity of parts
· Identify the test points
· Locate the parts through reference designators
· Identify the numbers that are unique to the printed circuit board.
· Identify manufacturer marks, version numbers, and so on
2. How to apply PCB silkscreen?
Manual Screen-printing
Manual screen-printing is done when the line widths are greater than 7 mil (0.007”) and the registration tolerance is 5 mil. For this method you require a stencil of the text and traces made of nylon. The ink is pushed through the stencil onto the laminate. Next the board is baked in a curing oven for the ink to cure.
Liquid Photo Imaging (LPI)
This method is used when the line widths are greater than 4 mil. Liquid Photo Imaging is quite like the process used for the application of solder mask. In this a liquid photo-imageable epoxy is coated on to the laminate and then exposed with UV light. After this the board is developed and cured. It is much more accurate than manual screening.
Direct Legend Printing (DLP)
DLP is the most accurate of all these processes but is more expensive. In this process an inkjet projector is used with acrylic ink that is applied onto the raw PCB directly from the CAD data. The ink is cured with UV light as it is printed. It should be noted though that the acrylic ink does not cure on boards with silver finishes.
3. What are the considerations for PCB silkscreen design?
As discussed earlier, using a silkscreen PCB layout is an important aspect of board design and not including it can cause serious problems for PCB assembly and testing. The silkscreen is also used for labeling, which may include manufacturer information, testing certifications, model or serial numbers. In order to be effective and useful, the silkscreen must have clearly readable text, provide sufficient image resolution and, most importantly, be accurate. Here are a few tips to help you ensure that your silkscreen PCB layout can be used for its important roles in PCB assembly, testing and identification:
· Only use fonts approved by your CM as some fonts, although easily created in software, are difficult to generate during board manufacture.
· Use white or black instead of other colors to provide the best contrast with your board’s solder mask color.
· Make sure to follow your CM’s clearance and dimension guidelines. This will ensure that your silkscreen items do not get covered by components and are easily visible.
4. What is the importance of PCB silkscreen?
Though the Silkscreen has nothing to do with the functionality of the Printed Circuit Board, the PCB Silkscreen provides information on
· Warning Symbols – The warning symbols indicate the parameters on the high voltage points that you need to avoid or handle.
· Polarity Indicators – It helps you to trace the polarized component’s orientation.
· Locating the parts via reference designators
· It helps in identifying the test points and unique numbers for each board.
· Reference indicators – It helps in identifying the component types via BOM. The Pin 1 indicator helps you to connect the pins to the suitable pads in the footprint. The leading pattern of the component outline would show the placement of a component. The polarity indicators provide you with the polarized component’s orientation
· Pin 1 indicator – It indicates the connection of pins on the correct pads of the footprints.
· Component Online – It enables you to place the components on PCB through indications.
Industry Category