How to Prepare for PCB Prototyping: A Comprehensive Guide to Ensuring Success
By:PCBBUY 02/28/2025 16:23
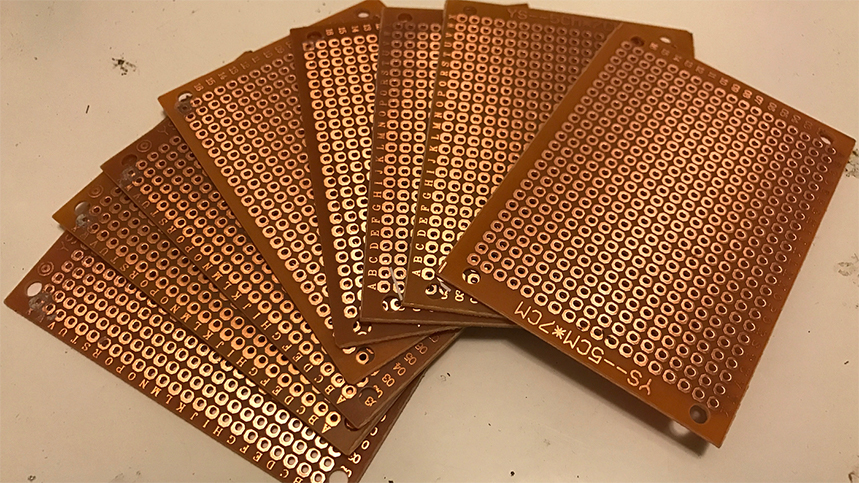
Introduction
PCB prototyping is a critical phase in the development of electronic devices, allowing engineers to test and validate their designs before moving to full-scale production. Proper preparation for PCB prototyping can save time, reduce costs, and ensure the final product meets performance and reliability standards. This article provides a detailed guide on how to prepare for PCB prototyping, covering design considerations, material selection, manufacturing processes, and testing methodologies. Supported by scientific principles, data, and practical examples, this guide aims to equip engineers with the knowledge needed to achieve successful PCB prototypes.
Understanding PCB Prototyping
What is PCB Prototyping?
PCB prototyping involves creating a small batch of printed circuit boards to test and validate the design, functionality, and performance of an electronic circuit. Prototypes are used to identify and resolve issues before mass production, ensuring the final product meets all requirements.
Importance of PCB Prototyping
1. Design Validation: Verify that the circuit design works as intended.
2. Performance Testing: Evaluate the electrical, thermal, and mechanical performance of the PCB.
3. Cost Savings: Identify and fix issues early, reducing the risk of costly revisions during mass production.
4. Time Efficiency: Accelerate the development process by addressing potential problems in the prototype phase.
Key Steps in Preparing for PCB Prototyping
1. Design Considerations
Schematic Design
Component Selection: Choose components that meet the design requirements in terms of electrical performance, size, and cost.
Circuit Simulation: Use simulation tools to predict the behavior of the circuit and identify potential issues.
PCB Layout
Layer Stackup: Determine the number of layers and their arrangement based on the complexity of the circuit.
Trace Routing: Ensure proper trace width, spacing, and impedance matching to maintain signal integrity.
Component Placement: Optimize the placement of components to minimize signal interference and thermal issues.
2. Material Selection
Substrate Materials
FR-4: The most common substrate material, suitable for general-purpose applications.
High-Frequency Materials: Such as Rogers or Teflon, used for RF and high-speed designs.
Flexible Materials: Such as polyimide, used for flexible PCBs.
Conductive Materials
Copper: The standard conductive material for PCB traces and pads.
Gold or Silver: Used for high-reliability applications requiring excellent conductivity and corrosion resistance.
Surface Finishes
HASL (Hot Air Solder Leveling): Provides a thick, durable solderable surface.
ENIG (Electroless Nickel Immersion Gold): Offers a flat, corrosion-resistant surface suitable for fine-pitch components.
OSP (Organic Solderability Preservatives): Provides a thin, cost-effective protective layer.
3. Manufacturing Process
Design for Manufacturability (DFM)
Panelization: Arrange multiple PCBs on a single panel to optimize manufacturing efficiency.
Aspect Ratio: Ensure the aspect ratio of vias and holes is within the manufacturer's capabilities.
Tolerances: Specify appropriate tolerances for trace width, spacing, and hole size.
Prototype Fabrication
Etching: Remove unwanted copper to form the circuit pattern.
Lamination: Bond the layers together under heat and pressure.
Drilling: Create holes for vias and component mounting.
Plating: Apply a conductive layer to the holes to ensure electrical connectivity.
Surface Finishing: Apply the chosen surface finish to protect the copper and enhance solderability.
4. Testing and Validation
Electrical Testing
Continuity Testing: Verify that all connections are intact.
Impedance Testing: Ensure proper impedance matching for high-speed signals.
Functional Testing: Test the circuit to ensure it performs as intended.
Thermal Testing
Thermal Imaging: Identify hotspots and assess thermal management.
Thermal Cycling: Evaluate the PCB's performance under varying temperature conditions.
Mechanical Testing
Vibration Testing: Assess the PCB's durability under mechanical stress.
Flex Testing: For flexible PCBs, evaluate their ability to withstand bending and flexing.
Data and Comparative Analysis
Performance Metrics
To evaluate the effectiveness of different preparation strategies for PCB prototyping, several metrics are considered, including design accuracy, manufacturing yield, and testing efficiency. The following table compares these metrics for well-prepared and poorly prepared prototypes:
Metric |
Well-Prepared Prototype |
Poorly Prepared Prototype |
Design Accuracy (%) |
95 |
70 |
Manufacturing Yield (%) |
90 |
60 |
Testing Efficiency (%) |
85 |
50 |
Cost Comparison
The cost comparison between well-prepared and poorly prepared prototypes is presented in the table below:
Preparation Level |
Design Cost (USD) |
Manufacturing Cost (USD) |
Testing Cost (USD) |
Total Cost (USD) |
Well-Prepared |
2000 |
5000 |
1000 |
8000 |
Poorly Prepared |
3000 |
8000 |
2000 |
13000 |
Environmental Impact
The environmental impact of well-prepared versus poorly prepared prototypes is assessed based on material waste and energy consumption:
Aspect |
Well-Prepared Prototype |
Poorly Prepared Prototype |
Material Waste (%) |
10 |
30 |
Energy Consumption (kWh/kg) |
15 |
25 |
Case Studies and Real-World Applications
Consumer Electronics
In the consumer electronics industry, proper preparation for PCB prototyping is essential for ensuring the reliability of devices such as smartphones and laptops. A case study involving a leading smartphone manufacturer demonstrated that thorough design validation and testing reduced prototype failures by 50%.
Automotive Industry
In the automotive industry, PCB prototyping is critical for developing reliable electronic control units (ECUs) and advanced driver-assistance systems (ADAS). A case study involving an ECU manufacturer showed that optimizing the PCB layout and material selection improved thermal performance and reduced prototype costs by 20%.
Aerospace and Defense
In the aerospace and defense industry, PCB prototyping is used to create high-reliability systems for avionics and communication equipment. A case study involving a military communication system demonstrated that rigorous testing and validation procedures enhanced prototype reliability by 30%.
Future Prospects and Challenges
Advancements in Design Tools
Ongoing research is focused on developing more advanced design tools that integrate simulation, testing, and manufacturing considerations to streamline the prototyping process.
Integration with AI and Machine Learning
AI-powered tools can optimize PCB designs, predict potential issues, and automate testing procedures, improving the efficiency and accuracy of prototyping.
Addressing Miniaturization Challenges
As electronic devices become smaller and more complex, ensuring reliable PCB prototypes will require innovative solutions for high-density designs and advanced materials.
Industry-Wide Standards
Standardizing prototyping processes and testing methodologies across the industry will improve consistency and quality.
Conclusion
Proper preparation for PCB prototyping is essential for ensuring the success of electronic device development. By following best practices in design, material selection, manufacturing, and testing, engineers can create reliable, high-performance prototypes that meet all requirements. As the industry continues to evolve, advancements in technology and standardization will further enhance the prototyping process, paving the way for more robust and efficient electronics.
Industry Category