How to Prevent PCB Warpage with 9 Basic Important Tips?
By:PCBBUY 02/27/2024 16:21
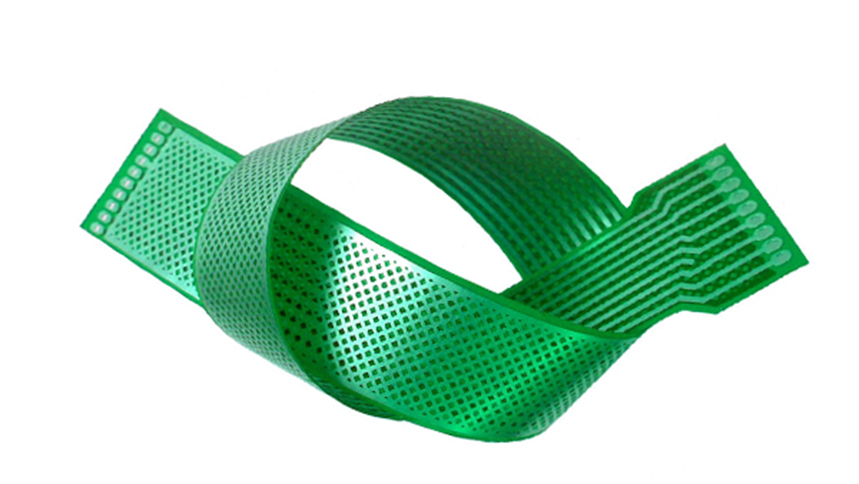
How to distinguish the latitude and longitude? The rolling direction of the rolled prepreg is the warp direction, and the width direction is the weft direction; for the copper foil board, the long side is the weft direction, and the short side is the warp direction. If you are not sure, please check with the consumer or supplier.
Do you know how to prevent the PCB warpage? If you are curious about the methods to prevent the PCB warpage, please check and read the content below for more information.
What Are the Causes of PCB Warpage?
In the automatic insert line, if the printing board is not smooth, it will cause inaccurate positioning, and the components cannot be inserted into the hole and surface of the plate, and even break the automatic insert machine. The welded plates with the components are bent, and the component feet are difficult to be cut in order. The boards can’t fit into the case or the socket, so it’s equally annoying for an assembly plant to get stuck on the board. At present, the PCB has entered the era of surface mounting and chip mounting, and the assembly plant must be more and stricter.
According to IPC – 6012, specification for the identification and performance of rigid PCB, the maximum permissible warp and twist for surface mounting of PCB is 0.75%, and other boards allow 1.5%. This is an improvement over IPC – RB – 276. Currently, the warping degree approved by each electronic assembly plant, whether double-sided or multilayer, is 1.6mm thick, usually 0.70~0.75%, and many SMT, BGA boards require 0.5%. Some electronics factories are agitating to increase the standard of warpage to 0.3% and test the warpage using gb4677.5-84 or ipc-tm-650.2.4.22b. Put the printing plate on the platform to be checked, and insert the test pin into the place with the maximum warp.
However, there are ways to detect warpage earlier. One of the ways is by using trace mapping technology, to predict warpage. This procedure is done by mapping the copper constituent. Observing this process makes it easier for the creator in arriving at the correct answer.
How to prevent PCB warpage?
1. PCB warping is caused by design and manufacturing issues. The PCB with obtuse and concealed holes needs multiple layering. Most constructors need to be aware of this issue to be able to know what to do and how to do it. This is also one of the common causes of PCB warping. Sizes and shapes of the PCB can as well cause warping. Bigger and larger tabs on the panel structure can cause PCB warping. Also, if the plate you’ll be using isn’t smooth, it causes imperfect positioning. This can cause the construction plant to get stuck thereby causing PCB warping.
2. In addition, trying to make the PCB thicker than its normal weight can cause the PCB to warp. Sometimes the manufacturers don’t remember to de-stress after layering. This causes PCB to warp after manufacturing. In addition, using DFM check is a good technique used to detect possible PCB warping. When warping occurs in PCB it causes lots of damage that most times can’t be repaired.
3. Immediately warping is detected it should be addressed instantly. But if repair is not possible it can be discarded. Most times, when soldering, the solder machine may pick up solder and spread it all through the PCB. This can cause PCB warping. Another solution for avoiding PCB warping is by deducting the copper weight.
4. Pallet design during reflow: Thin PCBs require palletization during reflow. Rush PCB recommends the following design for the pallet:
· Minimize the temperature difference between PCB and pallet
· Minimize the clearance between PCB edge and pallet edge
· Use low spring force for holding down the perimeter and corners of the PCB
· Provide adequate support across the span of the pallet to prevent the PCB from sagging at elevated temperatures.
5. Boards are to be baked for a couple of hours above the tg temperature of the material during the fabrication process using heavy steel platens to protect the top and bottom of the stack. If the boards are secured properly during the baking process there should not be warping. Are the boards quick turn prototypes that are being processed too quickly for adequate curing? Another possibility is an unbalanced board design. An uneven inner layer ground plane design could be to blame. Not to mention the variability of laminate types and the affects that non uniform heating and cooling may have on the board. This is an issue you may want to communicate with your board supplier. Bottom line, boards should be cured properly at the board manufacturer prior to you receiving them.
6. Because in the PCB board making process, the substrate has to be subjected to heat and many chemical substances. For example, after the substrate is etched, it needs to be washed with water, dried and heated, and the thermal shock experienced by the hot air spraying tin is large. These processes may cause the PCB board to warp. Solution: Since stress is the main cause of substrate warpage, if the copper clad laminate is baked before the copper clad laminate is put into use, the role of the bake plate is to fully relax the stress of the substrate and help reduce the warpage of the substrate in the PBC making process.
After the prepreg is laminated, the warp and weft shrinkage rates are different, and the warp and weft directions must be distinguished during blanking and lamination. Otherwise, it is easy to form the warpage of the waste board after lamination, and it is difficult to correct it even if the pressure is applied to the baking board. Many reasons for the warpage of the multilayer board are caused by the fact that the prepregs are not distinguished in the warp and weft directions during lamination. How to distinguish the latitude and longitude? The rolling direction of the rolled prepreg is the warp direction, and the width direction is the weft direction; for the copper foil board, the long side is the weft direction, and the short side is the warp direction. If you are not sure, please check with the consumer or supplier. During fabrication of a PCB, there is even distribution among all dielectric layers. However, it is the uneven distribution of copper layers that causes PCB warpage to occur. To prevent warpage, the designer must balance the copper pattern on each layer of the board with the circuit area. The designer must also equalize the component layout, the assembly distribution, and the thermal distribution to decrease warpage.
Industry Category