How to Prevent Solder Balls with 7 effective tips?
By:PCBBUY 09/17/2021 09:44
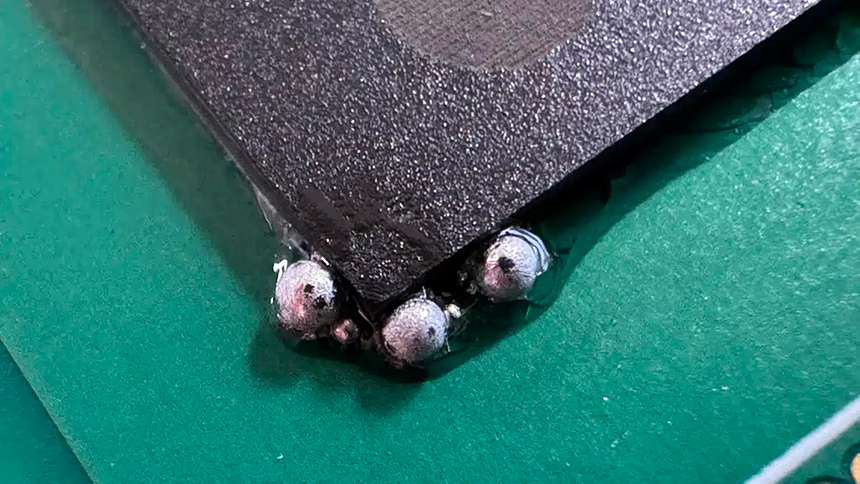
Solder balls are some of the most common PCB manufacturing defects. Solder balls after SMT reflow soldering are almost a common defect that occurs in the printed circuit board (PCB) assembly process. Several tinny balls surrounded along with the peripheral edge of the flux residue after reflowing is known as solder balls.
In this article, follow us and get into the professional knowledge about solder balls. If you are curious about the methods of preventing the solder balls, please check and read the content to learn more information about it.
What are the main reasons of solder balls?
· Environment: The air humidity in the workshop is too high
· People: tin remains during repair; tin beads are brought into the repair area; the steel plate is not clean by manual testing; the solder paste is not sufficiently stirred
· Material: PCB is damp; solder paste metal content; solder paste particles are small and oxidized
· Method: The amount of tin at the bottom of the component welding terminal is too large; the thickness of the steel mesh is too thick and collapses; the solder paste is turned on and the use time is not properly controlled, which absorbs water
· Machine: The temperature rise slope of the reflow soldering is too high; the pressure during mounting is too high; the printing wipe is not clean; the printing squeegee pressure is too high
How to Prevent Solder Balls with 7 effective tips?
1. Open the steel mesh
There is a lot of tin at the bottom of the component solder terminal, and it is squeezed on the solder mask after mounting to form a solder ball. What are the preventive measures: the steel mesh opens the anti-tin bead hole to improve and reduce the amount of tin
2. Avoid the moisture of PCB
PCB can retain moisture for some causes. Sometimes, storage in humid conditions causes water retention. At other times, the preheat temperature is not hot enough. As a result, the flux doesn't dry properly.
To avoid the problems, store PCB in dry conditions. Take care so that moisture and water don't damage the PCB. Also, bake the PCB at 120 C for at least 4 hours before SMT manufacturing. The thickness of the PCB hole is also necessary. It should be enough to prevent the trapping of water.
3. Process PCB aging control
The PCB board is exposed to the air for too long 8-12H to absorb moisture and damp, which causes the moisture in the board to splash and form tin balls during reflow soldering. What are the preventive measures: increase the aging control 4H of the PCB board after opening to avoid moisture.
4. Process the solder paste aging control
When the solder paste is opened, there is a temperature difference between the solder paste temperature (0-10℃) and the ambient temperature (23±3℃), which can easily absorb moisture. When the solder paste is used, it is exposed to the air for too long for 8-12H to absorb moisture; it causes the moisture in the solder paste to be heated and splashed to form solder balls during reflow
The solder paste is taken out from the refrigerator to 4H before opening, so that the temperature is consistent with the ambient temperature. During the use of tin green, follow the principle of small amounts and multiple times (addition in 1-2 hours).
5. Pay attention to the missing solder mask
It is the simplest mistake in SMT manufacturing. The absence of a solder mask between adjacent pads can lead to solder balls. Any manufacturer will not want that!
The solution to this simple problem is also straightforward. You need to apply the solder paste properly on the PCB. Make sure you don't miss out on areas like spaces between pads. Using quality equipment can reduce the chances of this problem. It would help if you also used a slow preheat temperature rate. That will help spread the solder paste evenly on the PCB surface. It reduces the likelihood of creating gaps.
6. Mention the proper pad spacing
Proper pad placement is crucial for SMT manufacturing success. Otherwise, it can lead to the failure of your project. Additionally, you also have the risks of solder balls. The solder balls can cause shorts or even fall off. For this reason, proper placing of pads is essential.
You need to adopt caution during the design phase. Design the pads in a way to maintain the required gaps between one another. Using a PCB designing solution makes the job easier. The stencil opening should also match the PCB design.
7. Avoid stencil dimensions issues
It would help if you used the right stencil for SMT manufacturing. The thickness of the stencil is of utmost importance. Stencils that are too thick can hamper soldering. It will also lead to the formation of solder balls.
It would help if you chose the right stencil thickness. Consider your SMDs to select the right stencil width. Don't go for stencils that are too thick. Use relatively thin stencils. Additionally, keep an eye on stencil opening ratios and shapes. Any discrepancy here can result in solder balls.
Industry Category