How to Process Ground Plane in High Speed PCB Design?
By:PCBBUY 02/17/2024 15:50
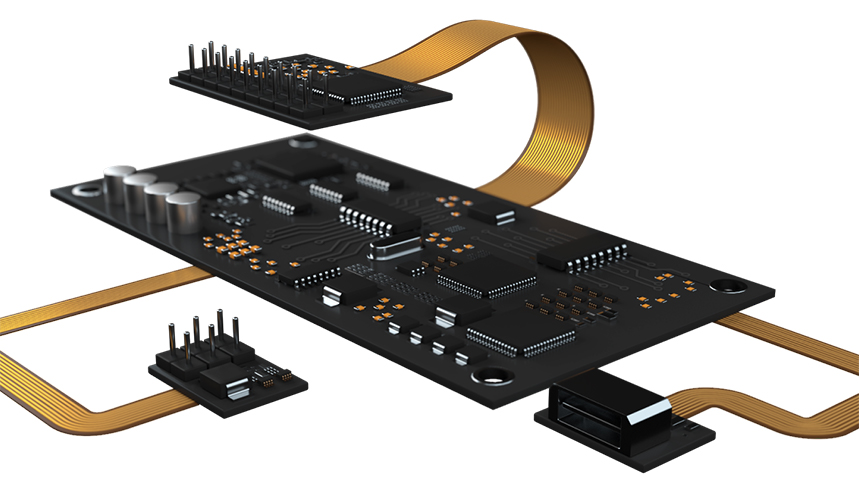
Knowing a design software that is capable of advanced options. High-speed designs require many sophisticated features in your CAD software. Many programs intended for hobbyists may not have these. Web-based suites also don't usually have advanced options. So one needs to learn and be skilled at a power CAD tool.
Do you know how to design high speed PCB? If you are searching for the knowledge about high speed PCB design, please check and read the content below for more information.
What Are the Common Problems of High Speed PCB Design?
You might be wondering, how in the world do you ever know if you’re working on a high speed project without discovering it through EMI issues? There are several schools of thought here, and we’ll break down the top 3:
Frequency
The first thought is that high speed design is categorized based on the frequency of a PCB and its ability to affect circuit performance. For some, this means anything above 50 MHz. Others categorize it into several buckets for low speed (<25 MHZ), moderate speed (25-100 MHz), high speed (100-1000 MHz), and anything above that is ultra-high speed, reserved for RF designers.
Traces
There’s also the school of thought that you can use the physical dimensions of your trace to determine if you’re working with a high speed device. This guideline states that once a trace is more than ⅓ the rise time of your device’s switching speed, then you’ve got high speed.
Separation
The last perspective takes a general approach, looking at your circuit design as a whole and asking the following question – does your system physically work together uniformly? Or do you have a bunch of sub circuits that are all organized into one larger circuit with everything working together separately? The latter puts you into the realm of high speed design.
Got your upcoming project classified as high speed? That’s all the background noise you need to worry about, let’s now dive into our top 10 tips for a successful design process.
How to Process Ground Plane in High Speed PCB Design?
There is much more to discuss than can be covered here, but we’ll highlight some of the key features and encourage the reader to pursue the subject in greater detail. A list of references appears at the end of this article.
A ground plane acts as a common reference voltage, provides shielding, enables heat dissipation, and reduces stray inductance (but it also increases parasitic capacitance). While there are many advantages to using a ground plane, care must be taken when implementing it, because there are limitations to what it can and cannot do.
Ideally, one layer of the PCB should be dedicated to serve as the ground plane. Best results will occur when the entire plane is unbroken. Resist the temptation to remove areas of the ground plane for routing other signals on this dedicated layer. The ground plane reduces trace inductance by magnetic-field cancellation between the conductor and the ground plane. When areas of the ground plane are removed, unexpected parasitic inductance can be introduced into the traces above or below the ground plane.
Because ground planes typically have large surface and cross-sectional areas, the resistance in the ground plane is kept to a minimum. At low frequencies, current will take the path of least resistance, but at high frequencies current follows the path of least impedance.
Nevertheless, there are exceptions, and sometimes less ground plane is better. High-speed op amps will perform better if the ground plane is removed from under the input and output pads. The stray capacitance introduced by the ground plane at the input, added to the op amp’s input capacitance, lowers the phase margin and can cause instability. As seen in the parasitics discussion, 1 pF of capacitance at an op amp’s input can cause significant peaking. Capacitive loading at the output—including strays—creates a pole in the feedback loop. This can reduce phase margin and could cause the circuit to become unstable.
How to Remove Parasitic Capacitance in high speed PCB design?
Given how circuit density continues to increase in many PCB designs, it’s impossible to remove parasitic capacitance. You can, however, reduce its effects by applying these strategies.
Increase clearance between conductors
If possible, allow for a higher clearance between traces in the design. Capacitance is inversely proportional to the distance between conductors. A larger clearance will reduce parasitic capacitance and effects like cross-coupling.
Use ground plane appropriately
While an inner-layer ground plane is recommended for reducing stray inductance, EMI, and heat dissipation, keep in mind that it could also increase the parasitic capacitance. Consider the pros and cons before covering the entire inner-layer with a ground plane.
Reduce vias
Vias are useful when building a compact PCB, but having too many of them can introduce significant parasitic capacitance. Use vias sparingly, and try to avoid any on high-speed traces.
Low-parasitic capacitance design is easier with the right PCB software. OrCAD PCB designer allows you to set design rules and tools to keep parasitic capacitance at bay in high-end circuit board design. You can also use InspectAR to accurately assess and improve PCBs using augmented reality and intuitive interaction. Inspecting, debugging, reworking, and assembling PCBs has never been faster or easier.
Industry Category