How to Process Rigid Flex PCB Design Guidelines?
By:PCBBUY 05/06/2022 09:26
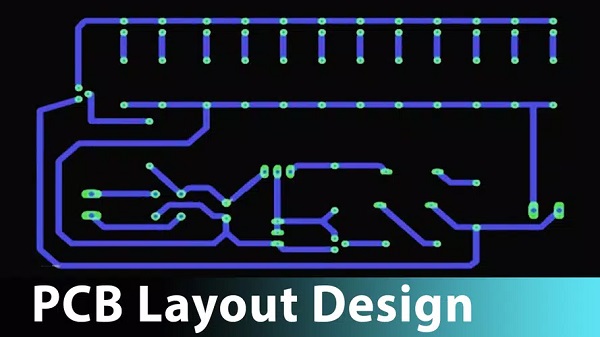
Rigid printed circuit boards consist of several types, such as phenolic cellulose paper copper-clad laminates, epoxide cellulose paper laminates, polyester woven glass fabric laminates, and epoxide woven glass fabric laminates.
A flexible circuit board is a kind of printed circuit board featuring high reliability and excellent bending performance. It uses polyimide or polyester film as the base material.
Rigid-Flex circuit boards consist of rigid and flexible circuit boards that are permanently bonded together.
If you are going to learn more about rigid PCB design, please check and read the content below for more professional knowledge in this passage. Let’s go!
What are the advantages of rigid flex PCB design?
Rigid-flex PCB design offers multiple advantages by integrating rigid and flexible PCB properties:
What is the main factor about rigid flex PCB manufacturing?
As is the case with any other PCB, the performance of rigid-flex PCB, to no small extent, is also determined by their substrate material.
Typically, a flexible dielectric film made of polyester is in the low-end products. In contrast, more advanced products like those used in the military and aerospace purposes use fluoropolymer and polyimide.
If we compare these three types of flexible materials, polyimide tops the list for having the highest dielectric constant. It can also withstand high temperatures and offers excellent mechanical and electrical properties. However, it can absorb moisture quickly and is quite expensive.
Talking about polyimide, it also performs well, but polyester offers pretty bad temperature resistance. If you want to operate the product at high frequencies, polytetrafluoroethylene offers a low dielectric constant and serves the purpose well.
In terms of adhesive films, the best materials for this purpose include polyester, acrylic, and epoxy because of the high degree of flexibility. They also have excellent adhesion and are relatively resistant to heat and chemicals.
But here is the catch. These materials have a significant coefficient of thermal expansion, and this is why the internal thickness of the film should not exceed 0.05 mm.
What are the applications of rigid-flex PCB?
Flex connections have mechanical advantages over conventional ribbon cables in various applications but in some cases, they also have better chemistry.
A flex PCB can be formed in complex shapes in three dimensions with branches to multiple connectors, which would be impossible to achieve with a ribbon cable. Moreover, flex circuits can be interfaced with rigid boards without the relatively tall and bulky connectors flat cables require, or in the case of rigid-flex construction, they can be integral with the boards and eliminate external connectors altogether. Furthermore, the conductor density of flex PCB can far exceed that of ribbon cables.
Industry Category