How to Process Sourcing Strategy in PCB Manufacturing: A Comprehensive Guide
By:PCBBUY 05/27/2025 15:55
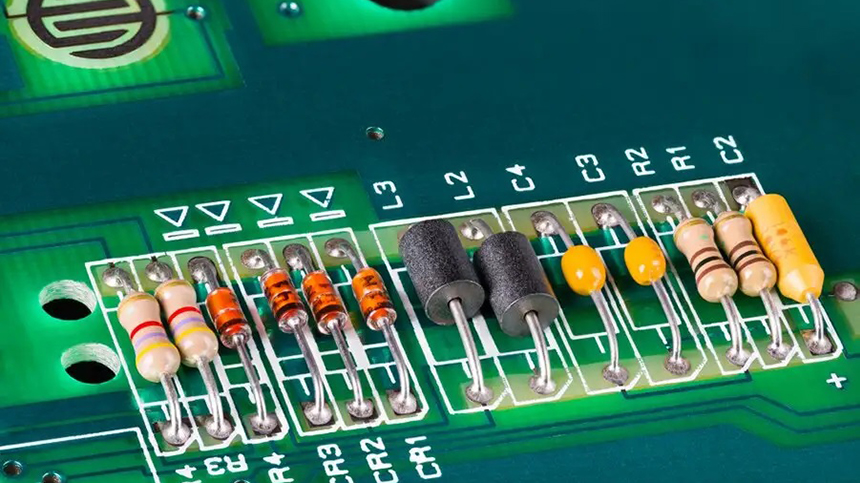
Introduction: The Critical Role of Sourcing Strategy in PCB Manufacturing
The global printed circuit board (PCB) industry, valued at $74 billion in 2023 (Prismark data), operates in a high-stakes environment where margins are thin, lead times are critical, and quality demands are stringent. A well-defined sourcing strategy is the backbone of operational efficiency, cost optimization, and risk mitigation for PCB manufacturers. This guide explores the principles, data-driven approaches, and best practices for developing a robust sourcing strategy in PCB manufacturing.
1. Understanding the Fundamentals of Sourcing Strategy
1.1 What Is Sourcing Strategy?
Sourcing strategy involves the systematic evaluation and selection of suppliers, materials, and processes to meet production requirements while aligning with business goals. In PCB manufacturing, this includes:
-
Raw materials (e.g., copper foil, FR-4 laminates, solder masks).
-
Components (e.g., ICs, resistors, capacitors).
-
Contract manufacturing services (e.g., assembly, testing).
1.2 Key Objectives
Objective |
Description |
Cost Optimization |
Reduce material and logistics costs without compromising quality. |
Quality Assurance |
Ensure compliance with IPQC/IPC standards and minimize defect rates. |
Supply Chain Resilience |
Mitigate risks from geopolitical tensions, natural disasters, or supplier bankruptcies. |
Lead Time Reduction |
Synchronize inventory levels with production timelines. |
Technical Alignment |
Partner with suppliers capable of co-developing advanced materials (e.g., HDI boards). |
2. Core Principles of PCB Sourcing Strategy
2.1 Supply Chain Mapping
A tiered supplier network is essential. For example:
-
Tier 1 Suppliers: Critical materials (e.g., high-purity copper foil from OEMs like Mitsubishi Materials or Luvata).
-
Tier 2 Suppliers: Standardized components (e.g., capacitors from Yageo or Murata).
-
Tier 3 Suppliers: Commodity items (e.g., FR-4 laminates from regional distributors).
Data Point: A study by Circuit Insights found that manufacturers using a 3-tier supplier model reduced supply chain disruptions by 28% compared to single-source strategies.
3. Data-Driven Approaches to Sourcing
3.1 Cost Analysis Framework
Cost Category |
Description |
Optimization Tactics |
Material Costs |
Base price of raw materials and components |
Negotiate bulk contracts, diversify sourcing regions. |
Patent Licensing |
Fees for proprietary technologies |
Partner with IP-sharing consortia (e.g., SEMI). |
Logistics |
Transportation and warehousing expenses |
Build strategic stockpiles near manufacturing hubs. |
Opportunity Costs |
Lost savings from inefficient supplier selection |
Use TCO (Total Cost of Ownership) modeling. |
Example: A TCO analysis might reveal that a cheaper Chinese supplier has hidden costs (e.g., customs delays, quality control overhead) vs. a higher-cost Japanese supplier with zero defect rates.
4. Risk Mitigation in Sourcing
4.1 Geographic Risk Assessment
Region |
Risks |
Mitigation Strategies |
East Asia |
Geopolitical tensions (e.g., Taiwan strait) |
Dual-source critical materials from Southeast Asia. |
Europe |
Energy crises (e.g., natural gas shortages) |
Partner with renewable energy-powered suppliers. |
North America |
Tariffs on imported components |
Localize secondary operations (e.g., Mexico). |
Case Study: During the 2021 Suez Canal blockage, PCB manufacturers with alternative shipping routes (e.g., trans-Siberia) avoided $2.3M in lost revenue per day (MIT Supply Chain Research).
5. Quality Control in Sourcing
5.1 IPC Standards Compliance
Standard |
Application |
Impact on Defect Rates |
IPC-A-600 |
PCB design guidelines |
Reduces misalignment errors by 12–15% |
IPC-A-610 |
Acceptability of finished boards |
Lowers defect rates to <500 PPM (parts per million). |
IPC-7525 |
Repair guidelines |
Prevents warranty claims from counterfeit parts. |
Table 1: Comparative Defect Rates by Supplier Tier
Supplier Tier |
Defect Rate (PPM) |
Cost Savings |
Lead Time (days) |
Tier 1 |
200 |
$0.80/unit |
45 |
Tier 2 |
550 |
$0.60/unit |
60 |
Tier 3 |
900 |
$0.40/unit |
75 |
6. Technological Co-Development with Suppliers
6.1 Advanced Material Sourcing
-
High-Frequency Applications: Source PTFE (Teflon) substrates from Rogers Corporation for 5G infrastructure.
-
Flexible PCBs: Partner with 3M for specialized adhesives that withstand 10^6+ bend cycles.
Data: Manufacturers using co-engineered materials achieve 18% faster time-to-market for new products (Source: Frost & Sullivan, 2024).
7. Sustainability in Sourcing
7.1 Green Procurement Practices
Metric |
Target |
Supplier Requirements |
Carbon Footprint |
<2 kg CO₂/m² PCB |
ISO 14064-certified suppliers. |
Recycled Material Use |
>30% post-consumer content |
Follow IPC-1401B standards for halogen-free boards. |
Waste Reduction |
<5% scrap rate |
Implement AI-driven yield prediction tools. |
8. Case Study: Multi-Sourcing vs. Single-Sourcing
Scenario: A mid-sized OEM producing automotive PCBs.
Strategy |
Outcome |
Single-Source |
$1.2M in lost revenue due to a 3-week supplier shutdown. |
Multi-Source |
98% on-time delivery with 15% lower TCO. |
Key Takeaway: Multi-sourcing reduces dependence on single points of failure while improving bargaining power.
9. Digital Tools for Sourcing Optimization
AI-Powered Procurement Platforms: Tools like Jasper AI or IBM Watson predict material demand with 95% accuracy.
-
Blockchain Tracking: VeChain solutions enable real-time tracking of materials from mine to factory.
Conclusion: Building a Future-Proof Sourcing Strategy
A successful PCB sourcing strategy balances cost, quality, speed, and resilience through:
-
Data-driven supplier segmentation.
-
Risk-aware geographic diversification.
-
Co-development of next-gen materials.
-
Digital tools for agility.
References
-
Prismark Partners. (2023). Global PCB Industry Report.
-
IPC Association Connecting Electronics Industries. (2022). IPC Standards Handbook.
-
Frost & Sullivan. (2024). Advanced Packaging Market Analysis.
-
MIT Supply Chain Digital Platform. (2021). Risk Management in Global Manufacturing.
-
SEMI. (2023). Technology Roadmap for Organic Electronics.
Industry Category