How to Reduce Electromagnetic Interference in PCB?
By:PCBBUY 03/22/2024 15:33
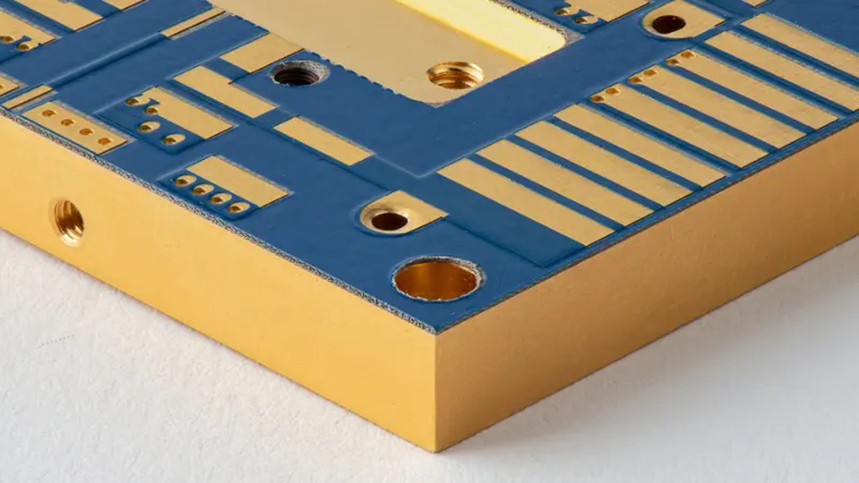
Some components will produce EMI no matter what design rules you follow — especially small, high-speed parts. Fortunately, shielding and filtering can keep this EMI’s effects to a minimum. Some shielding and filtering options include the following. Besides, unless your circuit board is a stand-alone device, the power supply is directly or indirectly connected to the power supply, which is also a common source of electromagnetic interference.
How to process the PCB trace layout?
Traces are conductive paths on a board, which contain flowing electrons while a circuit is active—that means they are just a bend or cross away from creating a fully radiating antenna.
Common best practices for trace layout include:
Avoid sharp right-angle bends. Capacitance increases in the 45° corner region changing the characteristic impedance and leading to reflections. This can be mitigated by rounding right angles.
Keep your signals separate. Keep high speed traces (e.g. clock signals) separate from low speed signals, and analog signals separate from digital signals.
Keep return paths short.
Route differential traces as close as possible. This increases the coupling factor, bringing influenced noise into the common mode which is less problematic for a differential input stage.
Use vias wisely. Vias are necessary because they let you take advantage of multiple layers in your boards when routing. Designers must be aware that they add their own inductance and capacitance effects to the mix, and reflections can occur from a change in characteristic impedance.
How to Reduce Electromagnetic Interference in PCB?
Some components will produce EMI no matter what design rules you follow — especially small, high-speed parts. Fortunately, shielding and filtering can keep this EMI’s effects to a minimum. Some shielding and filtering options include the following:
Component and board shielding: Physical shields are metallic packages that encapsulate all or part of a board. Their goal is to keep EMI from entering the board’s circuitry, though the specific methods vary based on the EMI’s source. For EMI that comes from within the system, component shields may be used to encase a specific component that produces EMI — thus connecting to ground, reducing the antenna loop size and absorbing EMI. Other shields may encase the entire board to protect against EMI from outside sources. A Faraday Cage, for example, is a thick protective enclosure designed to block RF waves. These devices are usually made of metal or conductive foam.
Low-pass filtering: Sometimes, a PCB can include low pass filters to eliminate high-frequency noise from components. These filters suppress the noise from these part, allowing the current to continue on the return path without interference.
Cable shielding: Cables that carry analog and digital currents create the greatest amount of EMI issues. They produce these issues by producing parasitic capacitance and inductance — a particular problem for high-frequency signals. Fortunately, shielding these cables and connecting them to ground at the front and back helps cancels out EMI interference.
Layer stackups: Make sure to use the proper layers and stackup configuration for your design. While fewer layers may reduce the board’s manufacturing costs, they may cause some of the challenges listed above. Your board will need adequate reference planes for clear signal return paths and a well-designed power delivery network to filter out the switching noises.
Component placement: Good signal and power integrity start with the proper placement of the components on the board. Sensitive nets that could potentially create noise need to be kept as short as possible, depending on how close their components are to each other. The same goes for high-speed transmission lines as well as power supplies. Simultaneously, enough room must be left between the components to get all of the trace routing completed. Be sure to place plenty of bypass capacitors as close as possible to large CPU and memory devices to absorb their power spikes.
Trace routing: Much of the trace routing will be guided by how well the components are placed, but there are some points to remember here as well. Keep high-speed transmission lines and controlled impedance lines on layers to use direct reference planes for signal return paths and shielding in a microstrip or stripline configuration. Be careful with split planes or other obstructions that might block the clear return paths on a reference plane. Keep routing as short and direct as possible except when traces have to be routed to a specific length. For power supplies, keep the traces as wide as possible and avoid right-angle corners in your routing.
Industry Category