How to Remove Unwanted Copper from a PCB in Manufacturing Process?
By:PCBBUY 10/30/2021 09:48
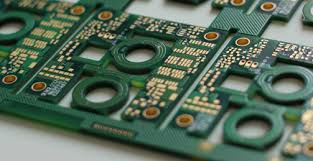
Do you know how to remove unwanted copper from a PCB? PCB is typically made by attaching a copper sheet to a substrate board, sometimes on both sides. The manufacturer then creates the circuits by removing copper so that only the required copper traces remain. This is called a subtractive method, and there are also additive techniques, usually for multilayer PCBs.
There are several types of subtractive methods for creating PCBs, including silk screening, photoengraving and PCB milling. In this passage, we are going to provide all the details of remove unwanted copper from a PCB, if you are interested in this topic, please check and read the content below for more.
If you want to order PCB product, please check and custom your order online.
How to remove copper from PCB edge trims?
The edge trim of PCBs consist of a plastic resin that contain large copper particles. The trim is shredded and ground to remove the plastic resin. A cyclone separator is then used to separate the copper metal particles from the plastic resin.
Another method is to use a stripping solution on the edge trim. This helps strip the copper, and it is removed as liquid form. The copper is then treated with reductants, which helps it regain its metal form. This method can also be performed for other precious metals in PCBs such as gold, platinum, and silver.
How to remove copper from PCB etching?
In this method, the etching solution is treated to weaken its acidic state. This allows for the copper ions to be discharged from the solution in the form of copper hydroxide. A filtering process similar to sludge recycling is used to transform the hydroxide. The hydroxide can also be converted into copper sulfate. This is achieved by first dissolving the hydroxide in sulfuric acid. The copper is allowed to cool and crystallize. It then undergoes centrifugation and drying.
How to reduce cost with removing copper from PCB?
Thanks to copper's even heat transfer capabilities, PCB manufacturers can install heat sinks onto the surface or build boards with one side entirely covered by a layer of copper, which also acts as a heat sink. Regardless of the method selected by copper circuit board manufacturers, they cut the assembly process short, which significantly reduces manufacturing expenses.
How to remove copper from PCB soldering process?
Following the etching process, remove the protective solder plate to expose the copper connections. Strip the tin and lead from the solder plate by immersing the printed circuit board in nitric acid or a hydrogen fluoride stripping solution. Use electrowinning to recover the copper and lead, as well as tin oxides, which are precipitated out and can be filter-pressed.
The hot air leveling process creates tin/lead solder dross that is suitable for recycling. Separate the tin by heating the dross in a reverberatory furnace at about 1400 to 1600 degrees Celsius, deslagging to remove iron, then putting it in a melting furnace with sulfur to remove the copper.
How to remove copper from PCB without chemicals?
In order to remove metal from circuit boards without chemical, Henan Doing Environmental Protection Technology Co., Ltd designed a PCB board crushing and separating machine. It is specially designed for processing various circuit boards. The mainly process of the machine is shredding, crushing, sieving and separation. Firstly, these PCB boards will become small particles through the shredder and crusher. Then these small particles will go through the magnetic separator, which will remove the iron.
After removing iron, these small particles will flow into the eddy-vibrating screen. The eddy-vibrating screen is mainly to control the size of metal and resin & fiber remain about 20-24 mesh. The bigger particles will be sent back to the crusher to further crushing. Then the air separator will do the first separation according to the different weight. Some particles of metals and non-metals have the similar weight, which cannot be separated by air separator. So we need an electrostatic separator to help us get a higher separation rate. Since both metal and plastic have different electrical conductivity.
How to remove copper from PCB using eco-friendly methods?
Conventional recycling methods have serious drawbacks. Pyrometallurgy, which separates metals by incinerating them at high temperatures, emits toxic gas products and is hard to control. Hydrometallurgy, which uses strong acid to leach the metals, results in large volumes of acid wastewater. Both require significant technical know-how and careful handling of the toxic byproducts.
The scientists turned to ball milling, an old technique for recovering metal from ores. The strong collisions of zirconia grinding balls hitting the wall of a zirconia ball-milling pot generate spikes of high energy, sparking solid-phase chemical reactions at room temperature. Copper metal generally wouldn’t be considered a good candidate for ball milling reactions because it is too stable, Hou says. But Hou and coworkers added a key oxidizing solid to the mix as well: potassium persulfate.
After crushing waste circuit boards to a coarse powder, the scientists milled the particles with solid potassium persulfate for 4 hours. Copper metal reacts directly with potassium persulfate in the high energy collisions of the ball mill to form cupric sulfate and copper oxide. Then they added the powder to water. In water, the copper compounds dissolve and the copper oxide reacts with potassium bisulfate, a breakdown product of the potassium persulfate, to form cupric sulfate. The powder containing the remaining solids from the circuit board—mostly brominated epoxy resin and glass fiber--is left behind. The researchers found they could transfer 99.8% of the copper from the waste circuit boards to the water with this approach. A final recrystallization step yielded purified cupric sulfate.
Industry Category