How to Select Laser Routing for PCB Depaneling?
By:PCBBUY 09/23/2024 16:46
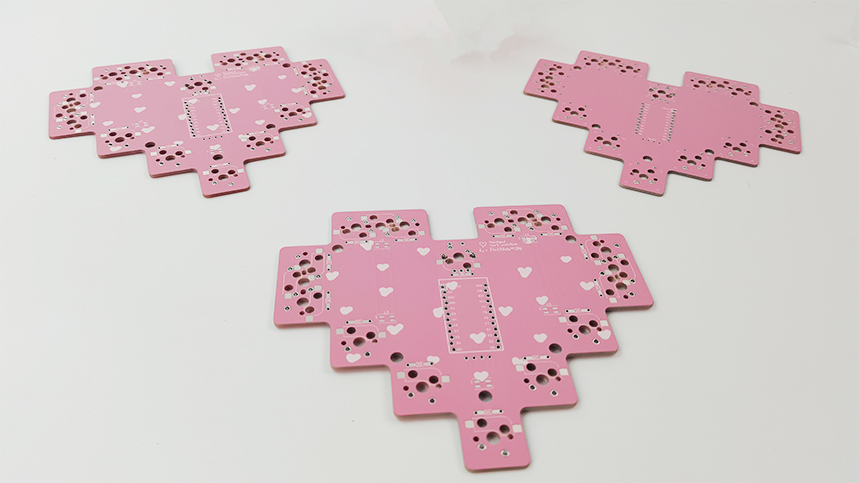
Printed Circuit Board (PCB) depaneling is an essential step in the production of electronic devices. As the industry moves towards higher densities, more compact designs, and greater complexity, traditional methods of depaneling are often insufficient. Laser routing has emerged as a precise, efficient, and non-contact solution. This article will delve into the process of selecting laser routing for PCB depaneling, including an in-depth explanation of its advantages, the types of PCB lasers used, and a comparison with other depaneling methods.
1. Introduction
PCB depaneling is the process of separating individual boards from a larger panel. With the evolution of PCB design towards higher densities, thinner materials, and delicate components, traditional depaneling methods may induce mechanical stress, leading to potential damage. Laser routing offers a non-contact, precise, and efficient alternative that has gained popularity in advanced electronics manufacturing.
2. Importance of PCB Depaneling
Depaneling is the final stage before testing and assembly, and improper methods can damage the board, leading to yield loss, component failure, or even scrapping entire panels. Depaneling requires a balance between speed, precision, and minimizing mechanical and thermal stresses. Traditional methods, such as routing or punching, can cause mechanical stress, particularly in thin or delicate boards. With higher demands for quality and precision, laser depaneling has become increasingly favored in modern production.
3. Traditional Methods of PCB Depaneling
3.1 Punching
In punching, a die is used to cut the PCB from the panel. This is a mechanical method that works well for large, low-complexity PCB boards, but it can introduce significant stress, especially in smaller or more delicate boards.
3.2 V-scoring
V-scoring involves cutting a shallow groove on both sides of the PCB to create a fracture line. The board is later broken along this score. While simple and cost-effective, it may cause mechanical stress and is not suitable for complex or dense PCBs.
3.3 Router Bit Depaneling
This method involves a spinning router bit to mechanically cut the PCB from the panel. It is more precise than punching or V-scoring, but still introduces mechanical stress, dust, and vibration, which can be problematic for sensitive components.
4. What is Laser Routing?
Laser routing is a non-contact method of depaneling that uses focused laser energy to ablate the material along predefined cut lines. The laser beam vaporizes the material, leaving a clean and precise cut. Laser routing is well-suited for complex PCB designs with intricate shapes, high component densities, and delicate substrates. It also allows for more design freedom, as it does not rely on predefined scoring or mechanical tools.
5. Types of Lasers for PCB Depaneling
5.1 CO2 Lasers
CO2 lasers operate at a wavelength of 10.6 micrometers and are best suited for cutting non-metallic materials such as FR4, polyimide, and other PCB substrates. They are widely used in industrial applications due to their power and efficiency.
5.2 UV Lasers
UV lasers, operating at wavelengths around 355 nanometers, offer finer precision than CO2 lasers. They can cut more intricate designs and are particularly useful for depaneling flexible PCBs, as well as sensitive components where heat generation must be minimized.
Laser Type |
Laser Type |
Suitable Materials |
Precision |
Thermal Impact |
CO2 Laser |
10.6 µm |
FR4, Polyimide, Epoxy |
Moderate |
Moderate |
UV Laser |
355 nm |
Flexible PCBs, Ceramics |
High |
Low |
6. Key Parameters for Selecting Laser Routing
6.1 Material Type
Different PCB materials have varying absorption characteristics for different wavelengths of laser light. CO2 lasers are effective for traditional PCB materials like FR4, while UV lasers are better suited for flexible materials like polyimide.
6.2 Board Thickness
Thicker boards may require multiple passes of the laser to fully penetrate the material. The choice of laser power and speed must account for the thickness of the board to ensure a clean cut without burning or damaging the substrate.
6.3 Tolerance Requirements
Precision is a critical factor in depaneling, especially for high-density boards where components are placed close to the edge. UV lasers provide higher precision and minimal kerf (material removed by cutting), which is ideal for fine-pitch designs.
7. Advantages of Laser Routing Over Traditional Methods
7.1 Precision and Accuracy
Laser routing provides superior accuracy compared to mechanical methods. The focused laser beam allows for fine cuts and intricate designs, with tolerances as low as ±20 microns. This is particularly beneficial for high-density PCBs with tight component spacing.
7.2 Non-Contact Process
Unlike mechanical methods that exert force on the board, laser routing is a non-contact process that minimizes mechanical stress. This is essential for fragile or densely packed boards that could be damaged by traditional depaneling techniques.
7.3 Reduced Stress on Components
Laser routing significantly reduces mechanical stress, preventing issues such as cracked solder joints, damaged components, or warped boards. It also minimizes dust and debris, which can interfere with sensitive electronics.
8. Application of Laser Routing for Different PCB Types
8.1 Rigid PCBs
For rigid PCBs made of materials like FR4, CO2 lasers are commonly used. The laser can cleanly cut through the material, creating precise edges without introducing mechanical stress.
8.2 Flexible PCBs
Flexible PCBs, often made from polyimide, benefit from UV laser depaneling due to its low thermal impact and high precision. The UV laser’s short wavelength allows for cleaner cuts without damaging the flexible material or causing deformation.
8.3 Rigid-Flex PCBs
Rigid-flex PCBs, which combine rigid and flexible sections, require careful handling during depaneling. UV lasers are preferred due to their ability to precisely cut the flexible sections without damaging the more rigid parts of the board.
9. Environmental Considerations and Safety in Laser Routing
Laser depaneling generates fumes and particulates that need to be properly managed. Adequate ventilation and filtration systems are required to prevent harmful byproducts from being released into the environment. Additionally, safety measures such as protective eyewear and enclosures must be implemented to protect workers from laser exposure.
10. Cost Analysis and Return on Investment (ROI)
Although laser routing equipment may have a higher initial cost compared to traditional depaneling methods, it offers long-term savings in terms of reduced waste, higher yield, and fewer damaged components. Additionally, the precision and flexibility of laser routing make it a valuable tool for complex designs, offering a faster return on investment (ROI) in high-volume production environments.
11. Laser Routing in High-Volume Production
Laser routing is highly scalable and can be used in both low- and high-volume production. In high-volume environments, the speed and accuracy of laser depaneling improve overall throughput while maintaining high-quality standards. Automated systems can integrate laser depaneling with pick-and-place machines for seamless manufacturing processes.
12. Chemical Interactions and Thermal Considerations
12.1 Effects of Laser on PCB Materials
When a laser cuts through PCB material, it generates heat, which can lead to localized thermal stress. However, UV lasers minimize this effect due to their low thermal input, reducing the risk of component or substrate damage.
12.2 Thermal Management during Laser Cutting
Managing the thermal effects of laser routing is crucial to prevent board warping or component damage. By adjusting the laser power and speed, manufacturers can control the amount of heat applied during the cutting process.
13. Best Practices for Implementing Laser Routing in PCB Production
13.1 Calibration and Maintenance
Regular calibration of laser equipment ensures consistent cutting quality. Maintenance, including cleaning optics and inspecting laser heads, is essential to avoid defects caused by misalignment or contamination.
13.2 Material Handling and Waste Management
Proper material handling minimizes the risk of damage to sensitive components during laser routing. Additionally, waste management systems must be in place to capture fumes, particulates, and any debris generated during the process.
Conclusion
Laser routing is a powerful and flexible method for PCB
depaneling, offering unmatched precision and minimal mechanical stress. Its non-contact nature and adaptability make it ideal for modern electronics manufacturing, particularly for complex, high-density, and fragile PCBs. By carefully selecting the appropriate laser type and optimizing process parameters, manufacturers can achieve high-quality depaneling while minimizing waste and improving overall production efficiency.
References
1. IPC-2221B, **Generic Standard on Printed Board Design**.
2. Ritter, D. J. (2017). **PCB Design and Manufacturing**.
3. Malek, M. (2019). **Laser Processing of Materials**.
Industry Category