How to Select PCB Substrate?
By:PCBBUY 11/26/2024 17:03
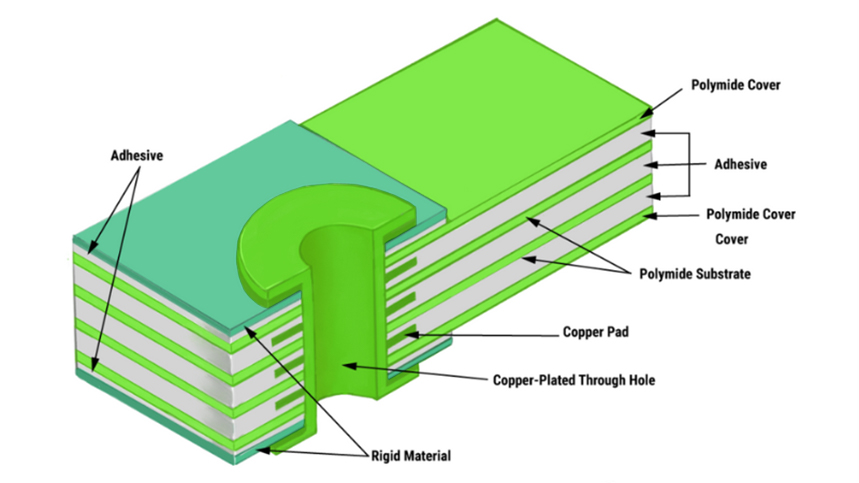
Printed Circuit Boards (PCBs) serve as the foundation of nearly all electronic devices, and the choice of substrate plays a critical role in determining the board's electrical, thermal, and mechanical performance. This guide covers the essential factors to consider when selecting a PCB substrate, common materials available, and their applications in modern electronics.
1. What is a PCB Substrate?
The substrate is the base material that supports the conductive layers of a PCB. It provides mechanical stability while influencing the circuit's thermal and electrical properties. Commonly made of materials like fiberglass or resin, it is integral to ensuring the PCB meets the demands of its intended application.
Key Components of a PCB Substrate
1. Base Material
Commonly made of fiberglass, epoxy resin, or other composite materials.
Provides durability and rigidity to the PCB structure.
2. Copper Cladding:
A thin layer of conductive copper is laminated to the substrate, creating the pathways for electrical signals.
3. Insulation:
Ensures electrical isolation between conductive layers.
2. Key Factors to Consider When Selecting a PCB Substrate
Selecting the right substrate depends on several performance requirements and environmental conditions:
a. Thermal Properties
-
Thermal Conductivity (kk): Indicates how well heat is dissipated. High-performance boards often require substrates with k>1.0k > 1.0 W/mK.
-
Glass Transition Temperature (TgT_g): The temperature where the substrate transitions from rigid to rubbery. For high-temperature applications, a TgT_g > 150°C is recommended.
-
Decomposition Temperature (TdT_d): The temperature at which the material starts to degrade. A TdT_d > 260°C ensures durability in extreme environments.
b. Electrical Properties
-
Dielectric Constant (DkD_k): Affects signal speed and impedance. For high-frequency applications, a lower DkD_k (~2.5-3.5) is ideal.
-
Dissipation Factor (DfDf): Measures dielectric losses. High-frequency PCBs benefit from a lower DfDf (< 0.005).
c. Mechanical Properties
-
Flexural Strength: Determines resistance to bending and deformation.
-
Coefficient of Thermal Expansion (CTE): Important for substrates exposed to temperature cycling.
d. Environmental Conditions
-
Moisture absorption, chemical resistance, and flame retardancy (measured by UL 94-V0 standards) influence the substrate's longevity.
e. Cost and Availability
While advanced materials like Rogers may outperform FR-4, they are often more expensive. Cost considerations must align with performance requirements.
3. Common PCB Substrate Materials
a. FR-4 (Fiberglass Epoxy)
-
Properties: TgT_g ~130-170°C, DkD_k ~4.2, affordable, widely used.
-
Applications: Consumer electronics, low-to-medium complexity designs.
b. Polyimide
-
Properties: High TgT_g (>250°C), excellent thermal stability, DkD_k ~3.5.
-
Applications: Aerospace, automotive, and high-temperature applications.
c. Rogers Material
-
Properties: Low DkD_k (~3.0), DfDf ~0.001, superior high-frequency performance.
-
Applications: RF circuits, telecommunications, and microwave designs.
d. Metal-Core PCBs (MCPCBs)
-
Properties: Incorporates aluminum or copper cores for improved heat dissipation.
-
Applications: LED lighting, power electronics.
e. Ceramic Substrates
-
Properties: High TgT_g, excellent thermal conductivity, low DkD_k.
-
Applications: Military, medical, and high-power devices.
Material |
TgT_g (°C) |
DkD_k |
Applications |
FR-4 |
130-170 |
4.2 |
General use |
Polyimide |
>250 |
3.5 |
High-temp |
Rogers |
>280 |
~3.0 |
RF circuits |
MCPCB |
150-200 |
Variable |
LED, power |
Ceramic |
>350 |
~6.0 |
High-power |
4. Chemistry Behind PCB Substrates
The chemistry of PCB substrates is crucial to understanding their performance under various operating conditions. Substrates consist of composite materials engineered to provide mechanical stability, thermal resistance, and electrical insulation while facilitating signal transmission. Here's a closer look at the chemistry behind these materials:
1. Fiberglass and Epoxy Resin in FR-4 Substrates
Chemical Composition:
· Fiberglass (Silicon Dioxide - SiO2SiO2):
Fiberglass provides the mechanical strength in FR-4. It is derived from molten silica, often with additional oxides such as boron trioxide (B2O3) to improve durability.
SiO2+Na2O→Na2SiO3 (a glass-forming reaction)
Epoxy Resin (Thermosetting Polymer):
Epoxy resins are cured polymers derived from bisphenol A (BPA) and epichlorohydrin, which form cross-linked networks when combined with hardeners like amines. These polymers provide excellent electrical insulation.
Thermal Properties:
Epoxy resin decomposes at temperatures above its decomposition temperature (TdT_d), typically around 300°C.
2. Polyimide Substrates
Chemical Composition:
-
Polyimides are polymers formed through the reaction of dianhydrides (e.g., pyromellitic dianhydride) and diamines (e.g., 4,4'-oxydianiline).
Properties:
-
High heat resistance (TgT_g often above 400°C) and excellent flexibility due to the aromatic ring structures.
3. Metal-Core PCBs
Chemistry of Core Materials:
· Aluminum (AlAl) or Copper (CuCu):
Metal cores serve as the heat-dissipating layer. Aluminum's oxide layer, formed naturally (4Al+3O2→2Al2O3), prevents corrosion and enhances thermal conductivity.
· The interface between the metal core and the substrate is often coated with dielectric polymers, ensuring electrical insulation while maintaining thermal conductivity.
4. Ceramic Substrates
Common Ceramics Used:
· Aluminum Oxide (Al2O3):
Formed through the sintering process of alumina powder. It has high thermal conductivity (20–30 W/mK) and excellent insulation properties.
2Al+3O2→Al2O3
· Aluminum Nitride (AlN):
Exhibits even higher thermal conductivity (180 W/mK) compared to Al2O3. Synthesized via direct nitridation:
2Al+N2→2AlN
5. Additives and Laminates
Flame Retardants:
-
Most PCB substrates include brominated flame retardants such as tetrabromobisphenol A (TBBPA), which decompose during high temperatures to release bromine radicals. These radicals inhibit combustion.
Copper Lamination:
-
Copper cladding on the substrate is performed via electrodeposition or lamination, ensuring uniform thickness. The surface oxidation of copper is prevented using an organic solderability preservative (OSP) layer or electroless plating:
Cu+H2SO4+H2O2→CuSO4+2H2O
6. Properties Derived from Chemistry
Material |
Thermal Conductivity (W/mK) |
Dielectric Constant (DkD_k)
|
Decomposition Temperature (TdT_d)
|
Key Applications |
FR-4 (Epoxy) |
0.3–0.4 |
4.2–4.7 |
300°C |
General-purpose PCBs |
Polyimide |
0.2–0.3 |
3.4–4.0 |
400°C |
Aerospace, flex PCBs |
Aluminum Oxide |
20–30 |
9.8–10.5 |
>1500°C |
High-frequency RF boards |
Aluminum Nitride |
180 |
8.0–9.0 |
>1500°C |
LED and power electronics |
The chemistry of PCB substrates is a blend of polymer science, metallurgy, and ceramics. Each material's molecular structure, synthesis process, and interactions define its unique properties, enabling PCBs to function reliably across various industries. Understanding these chemical principles helps in the selection of substrates tailored for specific applications.
5. Applications and Case Studies
The choice of substrate varies widely based on the industry:
a. Consumer Electronics
-
Use FR-4 due to cost-effectiveness.
b. Telecommunications
-
Opt for Rogers for its superior dielectric properties.
c. High-Power Electronics
-
Metal-core PCBs ensure efficient heat dissipation.
Case Study: High-Frequency Circuit
An RF design operating at 2.5 GHz required low DfDf. Switching from FR-4 to Rogers RO4350 resulted in a 20% reduction in signal loss.
6. Future Trends in PCB Substrates
As technology evolves, the demands on PCB substrates are increasing, necessitating advancements in materials to support smaller, faster, and more efficient devices. Here’s an exploration of the future trends shaping PCB substrates:
High-Frequency and High-Speed Materials
Rationale: With the rise of 5G, IoT, and high-speed communication, PCB substrates must handle frequencies exceeding 40 GHz. Traditional FR-4 materials are insufficient for these applications due to their high dielectric losses.
Key Developments:
-
Low-Dielectric Materials: Substrates like PTFE (Teflon) and liquid crystal polymers (LCP) are gaining traction due to their lower dielectric constant (DkD_k) and loss tangent (DfD_f), improving signal integrity.
-
Hybrid Substrates: Combining materials such as FR-4 and PTFE enables cost-effective solutions for high-frequency applications.
Enhanced Thermal Management
Rationale: Modern electronics, such as LED systems, power electronics, and high-performance computing, generate substantial heat. Substrates must manage thermal loads effectively to prevent device failure.
Emerging Solutions:
-
Metal-Core PCBs (MCPCBs): Substrates with aluminum or copper cores offer superior heat dissipation.
-
Advanced Ceramics: Materials like aluminum nitride (AlNAlN) and silicon carbide (SiCSiC) are being integrated for high thermal conductivity (up to 200 W/mK).
Eco-Friendly Materials
Rationale: Sustainability is becoming a critical factor in electronics manufacturing. PCB substrates must align with environmental regulations, such as RoHS (Restriction of Hazardous Substances) and WEEE (Waste Electrical and Electronic Equipment).
Innovations:
-
Halogen-Free Substrates: These materials eliminate brominated flame retardants, reducing environmental impact.
-
Biodegradable Substrates: Research is ongoing into bio-based polymers and fibers that can replace traditional substrates while remaining eco-friendly.
Flexible and Wearable Electronics
Rationale: The growth of wearable devices and flexible electronics requires substrates that can bend, twist, and conform to non-flat surfaces.
Advancements:
-
Polyimide Films: Used in flexible PCBs, they provide excellent flexibility and thermal stability.
-
Stretchable Substrates: Materials like thermoplastic polyurethane (TPU) and conductive elastomers are being explored for next-generation devices.
Thinner and Multi-Functional Substrates
Rationale: Miniaturization trends in devices necessitate thinner PCBs without compromising performance.
Future Directions:
-
Ultra-Thin Laminates: Substrates with thicknesses as low as 50 µm are being developed for compact designs.
-
Integrated Substrates: Multi-functional substrates that combine electrical, thermal, and structural roles reduce component count and simplify manufacturing.
Advanced Manufacturing Techniques
Rationale: Emerging manufacturing technologies are enhancing the capabilities of PCB substrates.
Notable Technologies:
-
Additive Manufacturing: 3D printing of PCB substrates allows for complex geometries and customized designs.
-
Nanomaterials Integration: Incorporating graphene and carbon nanotubes into substrates improves electrical conductivity and thermal performance.
Data-Driven Material Selection
Rationale: As simulation and modeling tools advance, selecting PCB substrates will become more precise.
Examples:
-
AI and Machine Learning: Predicting material performance under specific conditions helps in tailoring substrates to unique applications.
-
Digital Twins: Virtual replicas of PCB substrates enable optimization of material properties before physical production.
Industry-Specific Substrate Development
Rationale: Different industries require tailored substrates for optimal performance.
Examples:
-
Automotive Electronics: High-reliability substrates that can withstand extreme temperatures and vibrations.
-
Aerospace Applications: Lightweight substrates with radiation-resistant properties.
Comparison of Emerging Substrate Materials
Material |
Thermal Conductivity (W/mK) |
Dielectric Constant (DkD_k) |
Flexibility |
Eco-Friendliness |
PTFE |
0.2–0.3 |
2.0–2.2 |
Low |
Moderate |
Polyimide |
0.3–0.4 |
3.4–4.0 |
High |
Moderate |
Aluminum Nitride |
180–200 |
8.0–9.0 |
Low |
Low |
Biodegradable Polymers |
TBD |
TBD |
Moderate |
High |
The future of PCB substrates lies in innovation driven by performance requirements, sustainability goals, and advanced manufacturing techniques. Whether through the adoption of eco-friendly materials, the development of ultra-thin laminates, or the integration of high-performance ceramics, the industry continues to evolve, meeting the demands of increasingly complex electronics. These trends underscore the importance of research and collaboration in shaping the next generation of PCB substrates.
.
Conclusion
Selecting the right PCB substrate involves balancing electrical, thermal, and mechanical properties with cost considerations. Materials like FR-4 and Rogers dominate the industry due to their versatility, but emerging technologies are paving the way for innovative substrates. Understanding these factors ensures optimized performance for any PCB application.
Industry Category