How to Use Solder Flux PCB in PCB Manufacturing Process?
By:PCBBUY 11/09/2021 09:56
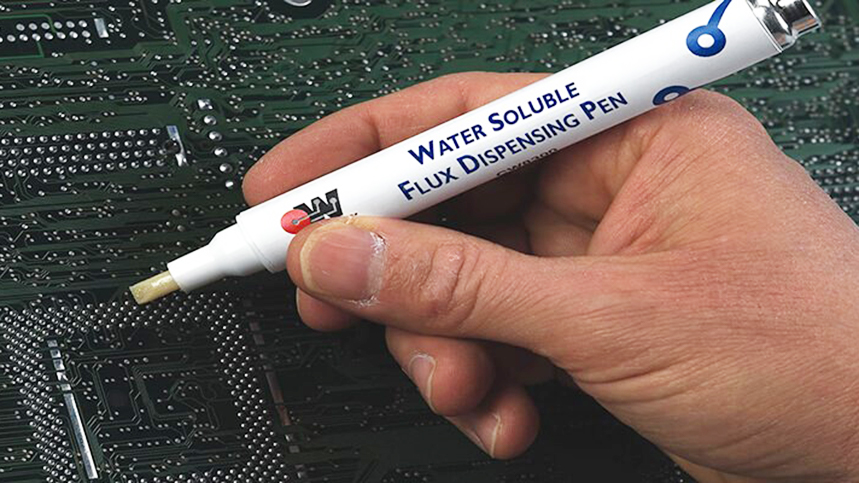
Flux is a chemical cleaning agent used before and during the soldering process of electronic components onto circuit boards. Flux is used in both manual hand soldering as well as the different automated processes used by PCB contract manufacturers. The main purpose of the flux is to prepare the metal surfaces for soldering by cleaning and removing any oxides and impurities. Oxides are formed when metal is exposed to air and may prevent the formation of good solder joints.
The flux also protects the metal surfaces from re-oxidation during soldering and helps the soldering process by altering the surface tension of the molten solder. In this passage, if you are curious about the methods of using solder flux PCB in PCB manufacturing process, please check and read the content for more information.
What are the types of solder flux in PCB manufacturing process?
There are three major types of solder flux based on electronics industry standard.
Rosin flux
one of the oldest types of flux, which is mainly made up of natural resin extracted from the oleoresin of pine trees and refined, however, the modern rosin is blended with different fluxes to optimize its performance. Flux is easy to flow particularly in a hot weather, make it quick to remove the oxides, and is good for removing foreign particles from the surface of the metal being soldered. Though rosin flux is acid as liquid, it will be inert and solid when it cools. Because rosin flux is inert as solid, it can be left on the circuit board without harming the circuit unless the circuit will warm to the point where the rosin may be liquid and eat away at the connection.
Organic acid flux
It’s also known as water soluble flux, which is made up of organic materials other than rosin or resin. There are some common weak acids used in organic acid flux, such as citric, lactic, as well as stearic acids. They are combined with solvents like isopropyl alcohol and water. Organic acid flux is more quick and stronger than rosin flux as cleaning the oxides off, in addition, it also has a good soldering with great flux activity, making it easy to clean the circuit board with regular water. However, it needs to remove the flux residue as soldering because the OA residue will make an effect on the operation and performance of a PCB with conductivity.
Inorganic acid flux
Another solder flux type that works better with stronger metals for instance brass, copper and stainless steel. You will need to clean the surface completely so that remove any corrosive residues from the surfaces if you use the inorganic acid flux. However, it will achieve a perfect solder joint if the residues are on the surface.
How is solder flux applied in PCB manufacturing process?
Solder flux can be applied on the board in a number of ways based on the soldering process being used.
Manual hand-soldering
Solder flux can be applied manually using a solder pen or in many cases flux is not mixed within the solder wire or solder bar. If the flux is mixed inside the solder, then simply heating the wire onto the surface with soldering iron is adequate. Alternatively, flux can be evenly spread on the surface of the board before applying the solder.
Wave Soldering
In this case, the flux is sprayed on the board prior to it going through the solder wave. Once in place, the flux cleans the components that are to be soldered. This removes any oxide layers that have formed. If the board is using a more corrosive type of flux, then the board will have to go through a pre-cleaning before the flux is applied.
Reflow Soldering
Solder flux used for the solder reflow process, is a paste composed of a sticky flux and small spheres of metal solder. Solder paste is a combination of a powder made up of metal solder particles and sticky flux that has the consistency of putty. They are generally mixed as a 50/50 ratio.
What is the importance of solder flux in PCB manufacturing process?
The main function or use of flux in any Printed Circuit Board Assembly or rework is to clean and remove any oxide and impurities from the board. These oxides deposited on the board may not permit good solder joints. If the solder joint is poor, there will be poor electrical conduction or poor flow of electricity through the circuit.
Solder flux helps to de-oxidize metals (copper tracks on the PCB and leads of electronic components) and helps better soldering and wetting. The activators in the flux promote wetting of the molten solder to the surface mount lands and component terminations or leads by removing oxides and other surface contaminants.
How to choose solder flux in PCB manufacturing process?
No-clean flux is a good choice for soldering where cleaning is to be avoided. The light residue can be left on the board, or removed with a flux remover. Rosin activated flux (RA) provides excellent solderability in a wide variety of applications. It is best to remove the residue after soldering for aesthetics and to avoid corrosion down-the-line. Rosin flux (R) or mildly activated rosin flux (RMA) can generally be left on the PCB after soldering unless aesthetics are a problem. Water soluble flux (OA) is a very active flux engineered to be removed easily with DI water, like in a batch or in-line system. It can also be removed with isopropyl alcohol (IPA). It is very important to clean off water soluble flux residues because they are highly corrosive.
You may also see options for “halogen-free” or “zero halogens”. These classifications are for companies that have green initiatives, or have to comply with halogen restrictions due to regulatory or customer restrictions. Halogens include chlorine, fluorine, iodine, bromine and astatine elements. These can come with trade-offs like cleanability, so if you aren’t required to eliminate halogens from your process, it is easier to stay with standard fluxes that contain halogens.
Industry Category