How to choose the right material for dielectric constant in PCB?
By:PCBBUY 06/05/2023 14:45
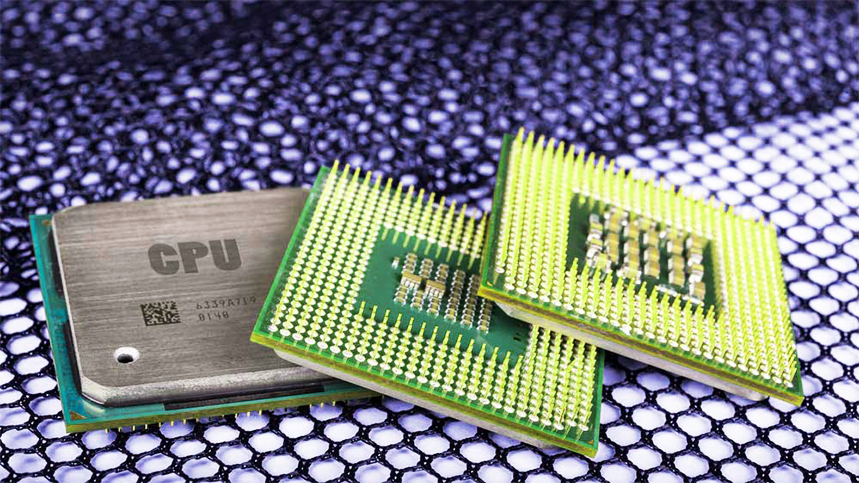
Circuit design itself requires an understanding of and training in electrical design. We won’t cover electrical theory or how to design different types of circuits here. And likewise, we won’t cover the operational details of the various CAD tools used in the PCB design process. Those systems range from schematic capture and circuit simulators to PCB layout, auto-routers, CAM systems, and analysis tools.
In the whole PCB manufacturing process, we may curious about the professional knowledge of dielectric constant in PCB. If you are searching for the detailed information of dielectric constant in PCB, please check and read the content below in this passage.
What is Dielectric Constant’s significance?
The PCB dielectric constant is measured as the stuff electrical absorbency to total space electrical permeability, and it is air; its quantity may be determined using modes condenser models.
The dielectric constant is a vital information component for constructing thin-film condensers and under other situations in which material may be anticipated to enter a loop. A coating condenser is produced of the sample film to detect it. The dielectric constant is the combination of the capacitor of the condenser as a dielectric with the voltage of a condenser as a dielectric condenser. The dielectric constant must be lowered for sheets that should be utilized to isolate electrically. Conversely, the dielectric constant must be high for films used as a dielectric in a condenser to reduce the condenser measurements. Altitude and stream frequency influence the dielectric constant.
How to choose the right material for dielectric constant in PCB?
Answering this question is really about considering the tradeoff between dielectric constant and other PCB substrate material properties. Some PCB substrate materials, such as Rogers high speed laminates or other ceramic materials, have more desirable optical properties but carry higher costs. These other materials can be more difficult to work with in a manufacturing process, thus they also carry higher fabrication costs. Certain PCB substrate materials are better for working with RF circuits and components and may be the best choice for mission critical applications that operate at extremely high speeds and high frequencies.
While we normally consider the imaginary part of the dielectric constant, the real part (i.e., the refractive index) is also important from a layout standpoint. The real part of the dielectric constant determines the speed at which an electromagnetic wave propagates through a material, while the imaginary part determines gain or loss in the material as the wave propagates. In terms of PCB design, the dielectric constant and trace geometry will determine how a signal propagates along a trace.
What are the considerations of choosing material for PCB dielectric constant?
Dielectric constant is the first number most engineers consider when sorting through different printed-circuit-board (PCB) materials. It is the number that guides the search, when needing a circuit-board material with a high dielectric constant or when a design requires a PCB material with a low dielectric constant. But what does dielectric constant really mean? And how can it affect a design if it is not “the right” dielectric constant? What happens to the circuit if it is designed and fabricated on a PCB material with a high dielectric constant and it should have been one with a low dielectric constant?
Many engineers are taught that a circuit material’s dielectric constant, or relative permittivity or Dk as it is also known, is a fixed value for a given material. In truth, the Dk values listed by materials manufacturers on their data sheets are numbers from a specific test method at a specific frequency, and the value will change under different conditions. For this reason, Rogers Corp. lists Dk values for their materials in reference to specific test methods, but will also provide “Design Dk” values for the materials that represent Dk values for the material under different conditions and values that can be used when designing or modeling a circuit, as in a commercial computer-aided-engineering (CAE) software program.
What are the properties of PCB dielectric constant?
The dielectric characteristics help us choose the finest one depending on its requirements. Some of the features are:
· Dielectric materials are typically non-metallic. The impedance of such compounds is thus high.
· The activation energy is significant and exceeds 3eV.
· Electrons are exceptionally highly bonded to the nucleus.
· The conductivity is extremely low due to the lack of electrons.
· Permeability – The polarising behavior or dielectric nature may be anticipated using the allowability rating.
· The dielectric constant is being used to quantify the dielectric polarisation intensity.
Decomposition temperature, or Td, is the temperature at which a PCB material chemically decomposes (the material loses at least 5% of mass). Like Tg, Td is expressed in units of degrees Celsius (ºC).
A material’s Td is an important ceiling when assembling PCBs, because when a material reaches or surpasses its Td, changes to its properties are not reversible. Contrast this to Tg, glass transition temperature, where properties will return to their original states once the material cools below the Tg range.
Choose a material where you can work in a temperature range that’s higher than Tg but well below Td. Most solder temperatures during PCB assembly are in the 200 ºC to 250 ºC range, so make sure Td is higher than this (luckily, most materials have a Td greater than 320 ºC).
Industry Category