How to protect PCB from moisture?
By:PCBBUY 06/07/2021 18:10
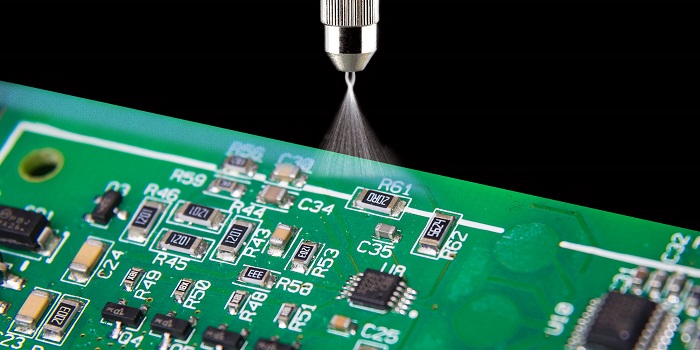
During the PCB manufacturing process, the design of PCB will affect whether moisture is more or less likely to be an issue. One of the most troubling issues with printed circuit boards involves the presence of moisture. If moisture exists within a PCB, the destabilization caused by it is liable to have a delaminating effect on the surface elements. Anytime soldering or rework is applied to the PCB, the delamination could easily expand as a result of the moisture contents.
In this passage, we will tell you everything about how to protect PCB from moisture, follow us and read the content we provide.
Moisture effect on PCB
The presence of moisture can lead to various functional failures on a PCB, depending on which components or conductive paths come into contact with it as diffusion takes hold. Moisture can fester in the epoxy glass, resin or glass interfaces and cracks in a board. Problems commonly associated with moisture include slowed circuit speeds and increased delay times with the functions of a corresponding device. If the problem exceeds a certain limit, the device might simply fail to activate.
Tests have been conducted that show the effects of moisture absorption and desorption in printed circuit boards. In a PCB with plated through-holes of varying density, trapped amounts of moisture have different desorption rates based on the distance between each hole. In PCBs that are heavily saturated, desorption can take hundreds of hours within high-temperature environments.
If a PCB is placed in an environment where the atmospheric moisture pressure exceeds the resistance of the board and its components, moisture can penetrate the PCB. To prevent moisture delamination from taking effect on a PCB, soldering should be performed only with high temperatures of less than 0.1 percent moisture content or with low temperatures of less than 0.2 percent moisture content. High-temperature soldering would hover around 260 degrees Celsius, while low-temperature soldering would be in the ballpark of 230 degrees Celsius.
How to remove moisture from PCB?
When measurements are made of a PCB’s ability to store electric energy, a change in moisture content can be detected within the board. Capacitance sensors are used in this process. Capacitance levels move in inverse proportion to hole density. If the latter is high, the former is low because there’s less distance between the moisture and the surface but more space for the moisture to escape.
In non-PTH PCBs, capacitance decreases at a more rapid pace. As such, less bake time is needed for these boards to have a low enough moisture level. On PTH boards, there’s less exposed surface room for the moisture to escape.
Due to the inverse effect of copper planes on the desorption process, they should be baked with consideration for their design. On one hand, you can empty moisture more effectively from a board by running the baking process for longer periods, but doing so could reduce the board’s solder ability and functional capacity. Consequently, bake time should be measured to avoid these possible side effects.
The process of moisture removal does not always yield predictable results. For example, a pair of identical copper planes could undergo a central flare-up of moisture as the baking gets underway, only to diffuse moments later. If this momentary swell of moisture occurs in an area of the board where delamination is most probable, it could be the unintended side effect of baking.
On some boards, moisture removal is simply not possible once the moisture has diffused through several layers. Therefore, it’s crucial to employ measures to prevent moisture from entering into the board during the initial process of assembly.
How to protect PCB from moisture?
During the manufacturing of PCBs, the lamination process should be conducted in a temperature-controlled environment where the air system is regulated with desiccant drying agents. It’s also crucial to wear fresh gloves during each work cycle to avoid the spread of contamination between different components.
The very process of PCB lamination has a dehydrating effect on the finished product. It’s during this stage that the prepregs and cores are put into place and the layers are bonded into a single board. Some manufacturers apply a low-pressure vacuum effect during this stage to prevent internal voids that could possibly trap moisture within the layers.
Among certain PCB fabricators, it’s common practice to bake the prepregs prior to lamination. The goal here is to prevent moisture pockets and blisters from forming on the finished board. This step is most useful when the prepreg has spent a certain length of time beforehand in an unregulated storage environment. Otherwise, this step is generally not necessary.
One of the most effective means of moisture prevention in a PCB is meshed copper planes, which inhibit moisture travel between layers as well as in and out of boards. Meshed copper planes also serve as a stronger bonding material between layers. However, their presence in a PCB can reduce the board’s electrical capacity.
Industry Category