How to select PCB materials?
By:PCBBUY 05/08/2021 17:48
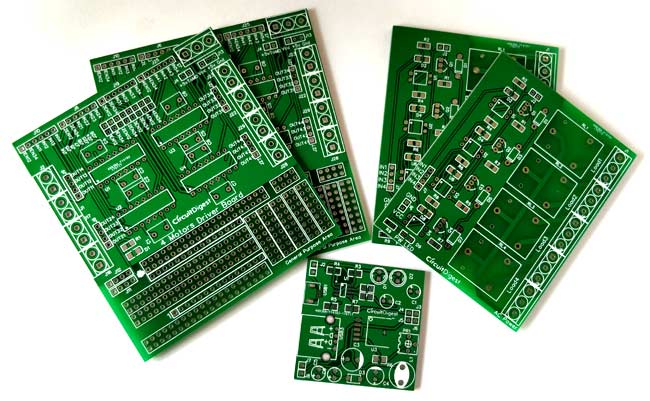
As the first step in PCB design process, PCB material selection is really important in the whole manufacturing process. Selecting the right PCB materials for your PCB design is very important as it can impact the overall performance of the PCB.
Before selection begins, there are many factors to be considered. Make sure material characteristics fit your specific board requirements and end application.
One of the main problems we face when manufacturing PCBs is the PCB designers’ frequent over-reliance on the material datasheets. The data sheets provide designers with a thorough description of a material’s electrical properties. However, the data sheets fall short when taking into account various real-world manufacturing concerns, and real-world manufacturing concerns matter because they impact yield and cost.
What are the PCB materials?
PCB material could be classified in several ways:
By Component location: single-sided, double-sided and embedded
By Stack-up: single layer and multi-layer
By Design: module-based, custom and special
By Bendability: rigid, flex and rigid-flex
By Strength: electrically strong and mechanically strong
By Electrical functionality: high frequency, high power, high density and microwave
By The board types can be used to select the circuit board material best suited for the design.
Single-sided PCBs include only one layer of a substrate, coated with a thin layer of copper. A protecting solder mask is laid down onto the copper layer. The silkscreen coat may be applied to the top to mark the elements of the board.
A double-sided PCB’s substrate includes metal conductive layers and elements attached to both sides (top and bottom).
Multi-layer PCBs enlarge the density and complexity of PCB designs by adding extra layers beyond the layers seen in the configuration of double-sided PCBs. These allow for extremely thick and highly-compound designs. Extra layers used are power planes that provide the supply to the circuit with power and decrease the levels of electromagnetic interference (EMI).
Rigid PCBs use a solid, rigid substrate material like fibre-glass that keeps the board from twisting. A motherboard within a computer is the best example of an inflexible PCB.
A flex PCB’s substrate is flexible plastic. It enables turning and shifting during use without harming the circuit(s) on the PCB. It can restore heavy wiring in superior gear where weight and space matter, such as satellites.
Rigid-flex boards consist of a rigid circuit board attached to a flex circuit board. These boards can fulfill compound design requests on demand.
How to select materials for PCB?
PCBs are manufactured in single- as well as double-sided varieties, some of which are copper-clad and others use aluminium for military and aerospace, automobile and medical industries applications. For these specific areas, material used should give maximum performance.
PCB board materials are selected for their light weight, quality or their ability to handle high amounts of power. Since material levels correlate to performance levels, it is crucial to determine which functions need to be compared with one another when selecting PCB board materials.
Majority of flex boards consist of Kapton, a polyimide film that has qualities such as heat resistance, dimensional consistency and dielectric constant of only 3.6. Kapton comes in three Pyralux versions: FR, non-flame retardant (NFR) and adhesive-less, high performance (AP).
Quality is important in the construction of any type of board for home electronics or industrial equipment. Components such as PCBs should offer superior performance for the expected lifespan. Electronic devices, microwaves and other household devices rely on PCB technology to stay in working condition.
LED PCB boards generate heat while in operation. Hence, LED chips are mounted on a base made of metals like aluminium, copper or a mixture of alloy, and coated with high reflective surfaces to achieve optimum heat management and to increase light output. This keeps the heat-generating components cool and improves their ability to dissipate heat. This results in increased performance and life of the LEDs.
Consequently, metal-core PCBs (MC-PCBs) are chosen for LED applications. These include a thin layer of thermally-conductive dielectric material that can transfer and dissipate heat with much greater efficiency than traditional rigid-PCBs. FR-4 materials include a thermal aluminium-clad layer to efficiently dissipate heat. Whereas, MC-PCB board materials are developed for higher power.
Industry Category