Lamination In Pcb
By:PCBBUY 03/12/2024 11:11
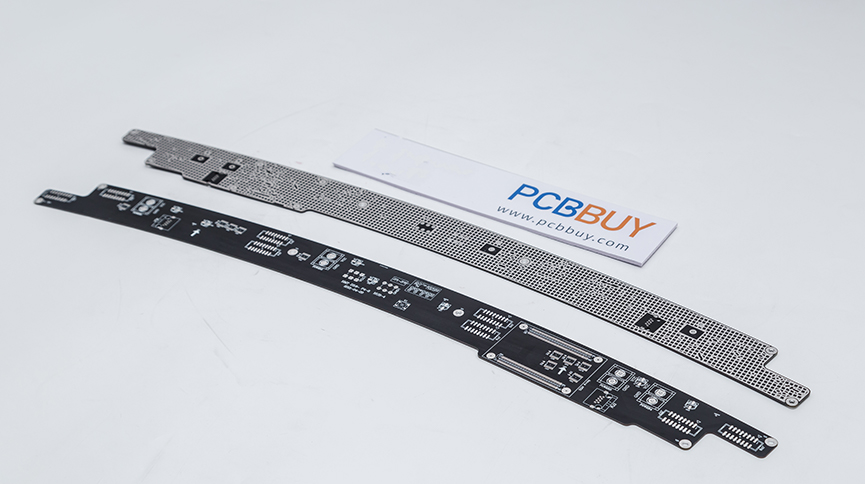
In the manufacturing process of electronic products, PCB lamination is a crucial step. It not only affects the quality and performance of the product but also has significant implications for the efficiency and cost control of the entire production process. This article will delve into the concept, purpose, process, and quality control of PCB lamination, aiming to provide readers with a deeper understanding of this critical process.
Concept and Purpose of PCB Lamination
PCB lamination, as the name suggests, is the process of bonding assembled electronic components with another circuit board. This process typically utilizes specialized high-temperature and high-pressure equipment for thermal curing, ensuring that electronic components are soldered onto the circuit board. The main purposes of lamination are as follows:
1. Securely fasten electronic components: Through lamination, electronic components can be securely fixed to the circuit board, preventing loosening or detachment during subsequent use. This helps to improve the reliability and stability of the product.
2. Ensure good electrical connections: The lamination process ensures a reliable electrical connection between electronic components and the circuit board, thereby ensuring the normal operation of the circuit. This is crucial for the performance and functionality of electronic products.
3. Achieve interconnection of multi-layer PCBs: For multi-layer PCBs, lamination can interconnect different layers of circuits, facilitating the transmission and processing of electronic signals. This helps to enhance product integration and performance.
Process of PCB Lamination
The process of PCB lamination typically includes the following steps:
1. Preparation: Firstly, electronic components need to be selected and tested to ensure their quality meets requirements. Simultaneously, the circuit board needs to be cleaned and treated to remove surface impurities such as dirt and oxides. These preparatory steps are essential for ensuring lamination quality and stability.
2. Component layout and arrangement: Before lamination, electronic components need to be logically laid out and arranged. This step involves considering factors such as electrical connections between components, heat dissipation requirements, and mechanical strength to avoid issues like cross-interference, electromagnetic interference, and mechanical stress. Proper layout and arrangement contribute to improved product performance and reliability.
3. Lamination operation: Once component layout and arrangement are completed, lamination can proceed. This step typically utilizes specialized high-temperature and high-pressure equipment. During lamination, precise control of parameters such as temperature, pressure, and time is necessary to ensure the quality and stability of solder joints. Additionally, attention should be paid to the correct sequence of lamination to avoid issues like misalignment or poor connections.
4. Quality inspection and testing: After lamination, the product needs to undergo quality inspection and testing. This step includes inspecting the quality of solder joints to ensure firm soldering without defects such as voids or cold solder joints. Additionally, electrical and mechanical performance testing is conducted to ensure compliance with design requirements and quality standards.
Quality Control of PCB Lamination
Quality control of PCB lamination is a crucial aspect of ensuring product quality and performance. Here are some recommended quality control measures:
Strict screening of components and circuit boards: Before lamination, rigorous screening and testing of components and circuit boards are necessary to ensure their quality meets requirements. This helps to reduce the rate of defective products and improve product reliability.
Precise control of lamination parameters: During lamination, precise control of parameters such as temperature, pressure, and time is essential. These parameters should be set based on the specific types of components and circuit boards to ensure the quality and stability of solder joints.
Strengthening employee training and skill enhancement: Lamination operations require certain professional skills and experience. Therefore, strengthening employee training and skill enhancement is an important way to improve lamination quality and efficiency. Through regular training and practical exercises, employees can master lamination techniques and operational standards, thereby improving product quality and stability.
Establishing a comprehensive quality inspection system: Establishing a comprehensive quality inspection system is a crucial means of ensuring the quality of PCB lamination. This includes establishing strict quality inspection standards and procedures, equipping with advanced inspection equipment and instruments, and cultivating professional quality inspection personnel. Through comprehensive quality inspection and control, problems can be promptly identified and resolved to ensure that product quality and performance meet requirements.
Continuous improvement and optimization of process flow: With the continuous advancement of technology and the changing market demand, the process flow of PCB lamination also needs continuous improvement and optimization. By introducing new technologies, equipment, and materials, lamination efficiency and quality stability can be improved. Meanwhile, based on market demand and customer feedback, timely adjustments and optimizations to product design and production processes can be made to meet market demand and enhance competitiveness.
Conclusion and Outlook
As one of the key processes in the manufacturing of electronic products, PCB lamination plays a crucial role in product quality and performance. Through the discussion and analysis in this article, we can gain a deeper understanding of the concept, purpose, process, and quality control of PCB lamination. In actual production processes, attention should be paid to details and standardized operations to ensure that each step meets requirements and standards. Additionally, measures such as strengthening employee training and skill enhancement and establishing a comprehensive quality inspection system should be implemented to improve lamination quality and efficiency. Looking ahead, with the continuous progress of technology and the evolving market demand, we believe that PCB lamination technology will become more mature and refined, providing a more solid foundation for the manufacturing and development of electronic products.
Industry Category