PCB Component to Edge Clearance
By:PCBBUY 08/21/2021 10:02
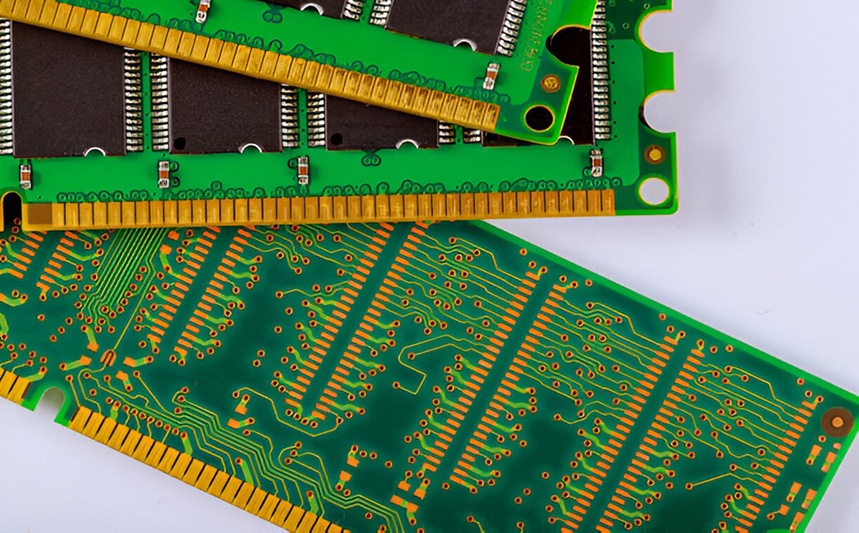
Components that are placed too close to the edge of the board run the risk of being damaged or causing problems with other aspects of circuit board manufacturing. The problem, of course, is that some components have to be close to or on the edge of the board in order to perform their function. To place your PCB parts so that they are in the most optimal locations, it is important to understand the concerns of placing components too close to the board edge.
In this passage, we will provide you all the details of PCB component to edge clearance, if you are going to learn more knowledge about it please check and read the content below.
What are the considerations of edge clearance on PCB?
The general guideline for component clearances around the edge of a printed circuit board is 0.100 inches. This will give an adequate amount of room for the test fixture and most assembly operations. Often this number is reduced by the manufacturer depending on the needs of the design. There are some areas of the board where specific clearances must be adhered to:
Panel V-grooves: For circuit board panels that will be scored with a V-grove for breakout, the parts must maintain a minimum of 0.075 inches to the edge of the board. This will give the cutting process enough room without damaging the components. For those parts that are taller, the minimum clearance grows to 0.125 inches to give those components a safe distance to the cutter.
Panel breakout tabs: For circuit boards that will be separated from panels using a breakout tab, components next to a tab must maintain a distance of 0.125 inches to the edge of the board. For taller components that minimum clearance grows to 0.250 to protect the components during depanelization.
Another edge clearance to remember is the copper to the edge of the board. For those components with larger connection areas, their solder joints may fracture with depanelization as well and must be held further back from the edge than other parts.
Special Considerations:
· Resistors: The recommended minimum edge clearance is 0.05”.
· Capacitors: The nearest point of the capacitor to the board edge should be no closer than 0.119”.
· Edge Connectors: If possible, use alternatives, such as connectors placed away from the board edge. If edge connectors are required, a good practice is tab routing or a combination of scored and tab routing.
What are the main rules of edge clearance on PCB?
Although it would be convenient to state definitively what the required component to board edge clearances should be, the truth is that these values vary between manufacturers. What we can do, though, is to lay out the different categories of clearances to be aware of along with some general values that you can use as a starting point:
Physical support: Some circuit boards require additional support during manufacturing due to the overall size, thickness, and weight of their components.
Copper: Although not a component, there also needs to be enough clearance between traces and power planes to the board edge. This is to protect the metal from twisting and lifting during depanelization.
Panels with V-grooves: Some circuit boards are separated from their panels by cutting V-grooves along the board outline.
Panels with breakout tabs: Other circuit boards are routed out of their panels before manufacturing and held in place with small breakout tabs until depanelization.
Drilled holes: Holes also are not a component, but they need to observe board edge clearance rules as well. It is recommended to maintain a minimum distance of 0.020 inches between the edge of the hole and the edge of the board.
Test points: ICT test points also need to be kept back from the edge of the board by 0.100 inches. This will ensure that there is enough room around the perimeter of the board for the vacuum seal of the test fixture.
Copper to PCB edge clearance
The minimal clearance between edge of board and pattern is.
For routed boards:
· 0.25mm (10mil) on outer layers
· 0.40mm (16mil) on inner layers
For boards with scoring (V-cut):
· 0.45mm (18mil) on outer and inner layers
If you require a copper area or plane to extend up to the board edge please clearly indicate this in the Mechanical Layer. Copper up to the board edge should only be used where absolutely necessary due to:
· There is a risk of a rough board edge as the copper may tear during contour routing (profiling).
· The copper can create electrical shorts between layers.
· Copper up to the board edge is NOT compatible with scoring (V-cut).
Industry Category