PCB Design for Reliability
By:PCBBUY 08/19/2021 17:08
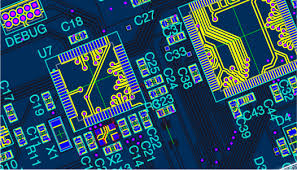
Essentially, DfR is a process that ensures a product, or system, performs a specified function within a given environment over the expected lifetime. Design for reliability ensures that products and systems perform a specified function within a given environment for an expected lifecycle. By putting DfR into practice, a product is allowed to run through its course of lifecycle reliably.
In this passage, we will tell you everything about how to use DfR principle in PCB design. If you are curious about it please check our content below for more knowledge.
Why to use Design for Reliability principle in PCB design?
In electronics, reliability is just as valuable, as it ensures that a product is safe, dependable, and marketable and that manufacturing companies don’t get overwhelmed with returned products that have failed. When you’re working on a PCB, design for reliability (DfR) is one concept that helps to improve reliability by addressing failure points before they become real-world problems.
· Learn what design for reliability (DfR) principles are.
· Understand the importance of design for reliability (DfR) concepts.
· Learn how to implement DfR principles during the PCB design process.
To prevent these types of issues, you’ll want to make using DfR principles a common practice, as it helps prevent PCBs from performance and reliability issues, particularly being a source of electromagnetic interference (EMI). While components may behave as they should in a lab setting, they are not guaranteed to do so in a considerably noisier electrical environment. Instances of corrupted signals are signs of EMI susceptibility, which is very difficult to mitigate once it’s in the field.
What are the main principles of Design for Reliability in PCB design?
When an engineer wants their design to be as efficient as possible, meeting their guidelines exactly. When it comes to elevators, because of the factor of safety for those is turned up to 11. Think of conservative design as a factor of safety for your PCB. There are two easy conservative principles you can apply here.
More Copper
When it comes to copper and reliability, more is more. Over time, copper can degrade, like when we were talking about high voltages. The thicker the copper layers you use, the less likely it is to fail.
Sometimes, users will put your board somewhere it’s not supposed to be and it will get too hot. Wider traces will help your board deal with extra heat and can carry more current. More copper may make your PCB more dependable, but be sure to evaluate how it affects your signal integrity as well.
Wide Spacing
Fine pitch components will always be more difficult to assemble and thus more prone to failure. If your board has to be reliable, avoid fine pitches. Closely grouped parts can also cause hotspots on your board, which will stress PCB materials and components themselves.
Whether your design has its wings in the air or its wheels on the ground, the PCB design process for reliability remains the same. When it comes to component selection, choose mature parts that have a long track record and multiple suppliers. You’ll want to use tried and true materials for your PCB as well, taking the operating environment and high voltages into consideration. Last but not least, you can add a factor of safety to factors like copper weights and spacing between components.
What are the considerations of Design for Reliability in PCB design?
Thermal management
It’s inevitable that the PCB will generate substantial heat when you’re designing,. It is important to know how well heat disperses to avoid rapid component degeneration.
Using thermal vias is one potential heat dissipation method. Thermal vias should be placed around heat-generating components; coupled with heatsinks and a cooling fan, they’ll allow engineers to avoid heat points building upon the components.
Component selection
Whether you’re choosing a microcontroller or a plain capacitor, it’s important to ensure what’s stated on the datasheet matches the design requirements. You’ll need to consider the most extreme scenario for the components, as that’s often where failure occurs.
For example, a microcontroller that runs at maximum speed consumes more power and produces more heat than one which runs at minimum capacity. These are issues that need to be addressed in the design. If you’re designing a PCB that runs in extreme environments, you may want to give up commercial-grade components and search for their industrial or military grade versions.
EMI mitigation
If your design relates to these terms: mixed-signals, RF, analog, and high-speed signals, you ought to pay attention to EMI radiation and susceptibility. Tips like keeping high-speed traces apart from analog signals are proven to prevent noise coupling from one trace to the other.
It’s also crucial to ensure that high-speed signals have a low-impedance return path that doesn’t traverse into the ground of other components. Plan the placement of components and separate the ground planes for analog, digital, and power modules. While doing so, avoid having ground loops in the PCB, as they can radiate noise.
Industry Category