PCB Recycling Methods
By:PCBBUY 09/02/2021 09:38
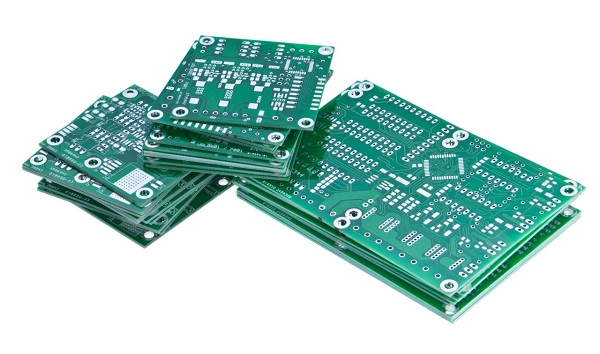
The manufacturing process for printed circuit boards is a difficult and complex series of operations. Due to the complexity of the process, various wastes are generated during PCB manufacturing. Solid wastes include edge trim, copper clad, protection film drill dust, drill pad, cover clad, waste board, and tin/lead dross. Liquid wastes include high concentration inorganic/organic spent solutions, low concentration washing solutions, resistor and ink.
Consequently, these spent solutions are characterized as hazardous wastes and subjected to tight environmental regulations. Nevertheless, some of the spent solutions contain high concentrations of copper with high recycling potential. These solutions have been subjected to recycling by several recycling plants with great economic benefit for many years.
In this passage, we will provide you everything about PCB recycling methods. Please check and read the content below for more about it.
What is the importance to recycle PCB?
Recycling printed circuit boards that are populated with many components could yield more valuable materials like:
· Gold
· Silver
· Platinum
· Palladium
How to process? The process extracts components affixed to the boards. Recycling PCB recovers approximately 99 percent of the precious and scarce metals from the recycling process.
The copper part of the board is completely recyclable as a metallic material. Recycling PCB helps reduce depletion of natural resources such as copper, as processors often reuse these boards multiple times. Although, after recycling, they must test the boards as the recycling process might damage certain parts of the board.
In addition, because of the excessive use of this type of circuit board in the electronic manufacturing industries, recycling printed circuit boards reduces solid waste, landfill and land pollution.
What are the main methods of PCB recycling?
PCBs can be recycled in three different ways, all of them with their pros and cons.
Thermal Recovering
The thermal recovering process heats up the PCB at a very high temperature with the idea of only recovering the metals present on the board (the FR-4 gets incinerated). This method can be easily implemented but produces deleterious gases such as dioxin and lead fume.
Chemical Recovering
The thermal recovering process involves putting the PCB in a bed of acid. The output recovers the metals but carbonizes (destroys) the FR-4 component. It also produces a high amount of wastewater which must be treated before sending it back to the environment.
Physical Recovering
Physical recovering is achieved by shredding and smashing the PCBs and then separating the metals from the non-metals. This process has no direct environmental impact but it is hazardous for the operators as the machinery is extremely loud, dust particles with heavy metals and glass fibre float in the factory which can cause respiratory diseases and an irritant odour is present because of the rise of temperature when the PCB is smashed and shred. In the following video from Suny Group, the physical recovering process can be appreciated
Size reduction and separation
A crushing stage is necessary for an easier further easier management of PCB waste. The PCB are cut into pieces of approximately 1 -2 cm2 usually with shredders or granulators giving the starting batch easily manageable for supplementary treatments. Further particle size reduction to 5-10 mm can be carried out by means of cutting mills, centrifugal mills or rotating sample dividers equipped with a bottom sieve. The local temperature of PCB rapidly increases due to impacting and reaches over 250°C during crushing, so a pyrolytic cleavage of chemical bonds in the matrix produces brominates and not brominates phenols and aromatic
Applications in composites
Physical recycling for non metallic fraction sorting from separation stage has been recently reviewed. The thermal stability of the non metallic fraction of PCBs is very important for physical recycling methods which must be suitable for moulding processes.
The thermosetting matrix more suitable for making composites with PCB quote scraps are phenolic resins, unsaturated polyester resins and epoxy resins. To ensure the surface smoothness, the size of non metallic fractions used was less than 0.15mm. The non metallic items so produced are used for trays, sewer grates, kitchen utensils, electronic switches etc. with properties comparable to that of composites with traditional filler. The 300-700 °C pyrolysis residues can be easily liberated for metal’s recovery and the glass-fibres can be re-compounded into new SMC and BMC structures as a filler replacement.
What are the effects of PCB recycling to environment?
The intention behind all PCB recycling processes is to not cause additional harm to the environment. While extreme heat changes metals both chemically and physically, the process also uses energy, and can release toxic dust and gas containing dioxin and lead.
Aside from using energy, pyrometallurgy also requires increased investment costs. Some of those costs cover the equipment needed to recycle metals. Other costs cover waste air processing that prevents hazardous dust and particulates from entering the air.
Although pyrometallurgy involves the use of high-tech methods, the process has taken an ugly turn. Firms have the tendency to send e-waste to Africa and China to use low-tech heating methods to remove impurities. In some of those locations, regulations do not apply. Instead, workers use open fires to burn non-metal waste materials while attempting to retrieve precious metals.
Industry Category